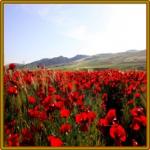
سلام به وب من خوش آمدید دوستان و همراهان عزیز از اینکه مهمان این وب هستید بسیار سپاسگزارم منتظر نظرات سازنده ی شما دوستان هستم
عنوان | پاسخ | بازدید | توسط |
![]() |
1 | 1215 | piskesvat |
![]() |
3 | 2709 | mehran99 |

مقدمه :
صنعت ذوب آهن و فولاد پيوسته خواهان مواد اوليه و به خصوص سنگ آهن با کيفيت بهتر مي باشد. از آنجايي که اغلب سنگ هاي معدني استخراج شده شرايط مورد نياز صنعت را برآورده نمي کنند، لذا فرآوري سنگ هاي آهن اهميت فراوان داشته و به طور پيوسته مورد بررسي و تحقيق به منظور توسعه و پيشرفت تکنولوژي مربوط به آن قرار دارد که اثر بسياري در کاهش هزينه ي ذوب و تصفيه و هزينه ي مصرف انرژي در کل توليد دارد. همچنين با انجام عمليات فرآوري، مي توان بعضي از روش هاي حرارتي را حذف و يا شدت آلايندگي آن را کاهش داد. مجموعه ي اين اهداف باعث شده است که امروزه فرآوري در صنايع معدني و متالوژي آهن از اهميت فراواني برخوردار بوده و در بسياري از موارد نيز کاربرد آن شرط اصلي براي انجام پذيري و اقتصادي بودن روش صنعتي باشد. شايان ذکر است که دامنه ي فرآوري و مراحل آن بستگي به سنگ معدن و پيچيدگي آن دارد. پيچيدگي سنگ مي تواند ناشي از عوامل متعددي همچون پيچيدگي ترکيب کاني شناسي، دانه بندي کانسنگ و پيچيدگي ناشي از هوازدگي باشد.


سنگ هاي استخراج شده طبيعي بدون خردايش قابل مصرف براي توليد آهن و فولاد نبوده و از طرف ديگر کاربرد کلوخه و گندله در کارآيي روش هاي توليد آهن و فولاد عملا غير قابل اجتناب است و توليد اين دو محصول واسطه نيز مستلزم خردايش سنگ معدن مي باشد. لذا اولين قدم، آزادسازي ذرات آهن دار از ذرات باطله ي سنگ آهن است که در اين راستا شکستن و خرد کردن کانسنگ هاي آهن يکي از مهم ترين عمليات فرآوري را تشکيل مي دهد. مراحل بعدي، جدايش کاني هاي مفيد آهن از کانيهاي مضر است که غالب روش هاي جداسازي، بر پايه ي خصوصيات فيزيکي کاني هاي مزبور بنا شده است.
روش هاي فرآوري کانسنگ آهن:
به طور کلي هر کارگاه فرآوري کانسنگ آهن شامل سه مرحله ي مجزا از يکديگر زير مي باشد:
1-سنگ شکني و خردايش
2-پرعيار کردن
3-جداسازي مايع از جامد
در هر يک از اين مراحل، روش هاي متفاوتي را مي توان به کار برد که در ادامه به طور مختصر مورد بررسي قرار مي گيرد.
سنگ شکني و خردايش سنگ آهن:
سنگ شکني و خردايش با هدف رساندن ابعاد بار به حد مطلوب و مورد نياز براي عمليات بعدي، اولين قسمت از کارگاه فرآوري و بيش از نيمي از هزينه ي فرآوري و بيش از 70 درصد انرژي مصرفي در کارگاه را به خود اختصاص مي دهد، لذا بررسي و کاربرد روش هايي که بتوانند در کاهش مصرف انرژي و هزينه اثر بگذارند، مي تواند در اقتصاد کارگاه نقش مهمي را ايفا نمايد. يکي از مهم ترين اهداف خردايش، آزادسازي کاني هاي باارزش از مواد باطله ي همراه در درشت ترين ابعاد ممکن است. بنابراين با کاهش ميزان خردايش، مصرف انرژي، ميزان نرمه و هزينه هاي جدايش کمتر و فرآيند نيز ساده تر مي شود. در حقيقت توليد يک محصول پرعيار ( پرعيارسازي کانسنگ هاي اکسيدي آهن ) ويا يک محصول آرايش ويا پيرايش يافته ( پيرايش کائولن با حذف ناخالصي هاي آهن ) در گروي مطالعه ي دقيق تعيين درجه ي آزادي است.


در مورد خردايش کانسنگ هاي آهن، فرآيند هاي متفاوتي وجود دارد که که مي توان به سيستم فکي و يا ژيراتوري براي توليد موادي با ابعاد درشت، ژيراتوري ثانويه و مخروطي براي توليد موادي با ابعاد متوسط و آسياهاي ميله اي و گلوله اي – قلوه سنگي براي موادي با ابعاد بسيار ريز اشاره کرد. فرآيند خردايش بيشتر در کارگاه هاي فرآوري سنگ آهن و در آسياهاي خودشکن و نيمه خودشکن به جاي آسياهاي کلاسيک ( ميله اي – گلوله اي ) انجام مي شود که اين عمل ضمن صرفه جويي در فضا، نيروي کار، هزينه و تجهيزات اضافي، ساييدگي آهن را نيز به دنبال ندارد. شايان ذکر است که در معدن آهن چادرملو، کانسنگ استخراج شده قبل از ورود به کارخانه ي کانه آرايي مربوطه وارد يک سنگ شکن از نوع ژيراتوري مي شود. سنگ هاي استخراجي پس از سنگ شکني مرحله ي اول مستقيما وارد آسياي خردشکن شده و دانه هاي درشت ضمن آنکه خود خرد مي شوند بقيه ي ذرات را نيز خرد مي کنند. اين آسياها داراي ضريب خردايش بسيار بالا بوده و با پذيرش سنگ هاي بزرگ ( حدود 300 تا 500 ميلي متر ) محصولي با ابعاد حدود 1 ميلي متر توليد مي کنند. آمار موجود نشان دهنده ي اين مطلب است که يک آسياي خودشکن کار يک تا دو مرحله سنگ شکني ( سنگ شکن هاي مرحله ي دوم وسوم ) و حداقل يک آسياي ميله اي و حتي قسمتي از کار يک آسياي گلوله اي را تماما انجام مي دهد و از اين طريق مي توان حداقل حدود 20 درصد از هزينه ي سرمايه گذاري کاهش داد. بدين ترتيب، وجود آسياي خودشکن باعث صرفه جويي 15 تا 20 درصدي در هزينه ي جاري خردايش مي شود.
در آسياهاي نيمه خودشکن، قسمتي از بار مورد خردايش را گلوله هاي فولادي تشکيل مي دهند. مقدار گلوله ي اضافه شده به آسياي نيمه خود شکن تا حدود 10 درصد حجم آسيا مي باشد ( اين مقدار در آسياي گلوله اي حدود 20 تا 25 درصد حجم آسيا مي باشد ). در اين آسياها نسبت قطر به طول آسيا در حدود 2 تا 5 بوده و بزرگ ترين آسياي موجود از اين نوع داراي قطري حدود 16 متر و قدرتي معادل با 11250 کيلووات مي باشد. شايان ذکر است که اين نسبت در مواردي که عمليات آسيا کني به صورت خشک است، در جهت کاهش مشکلات مربوط به خروج مواد، معمولا بيشتر بوده و حتي به 5 نيز مي رسد. سرعت دوراني اين آسياها تا 85 درصد سرعت بحراني بوده و بدين ترتيب با توجه به اينکه ماکزيمم ضربه توسط بار خرد کننده به بار در سرعت دوراني حدود 84 درصد سرعت بحراني وارد مي شود، ملاحظه مي گردد که عامل اصلي خردايش در اين آسياها ضربه مي باشد. از طرف ديگر توسط ضربه ذرات نسبتا درشت را مي توان خرد کرد و اثر ضربه خردايش نرم ناچيز خواهد بود، لذا از اين آسياها نمي توان انتظار خردايش نرم را داشت. لازم به ذکر است که نسبت طول به قطر در آسياي نيمه خود شکن خطوط توليد کارخانه ي کانه آرايي چادرملو در حدود 425/2 مي باشد.


با توجه به اينکه مقدار بيشتري از محصول کانه آرايي و خردايش سنگ آهن به منظور توليد گندله به کار برده مي شود و در نتيجه محصول خروجي از آسياي خودشکن يا نيمه خودشکن درشت تر از حدمطلوب براي گندله سازي ( حدود 40 تا 50 ميکرون ) است. همچنين خردايش نرم در آسياهاي مذکور، به دليل نياز به تقويت عمل فرسايش آسيا در جهت خردايش بيشتر، مقرون به صرفه نمي باشد لذا براي خردايش بيشتر، محصول خروجي آسياي خودشکن وارد آسياي گلوله اي ( با گلوله هاي نسبتا کوچک ) مي شود. لازم به ذکراست که در کارخانهي کانه آرايي آهن معدن چادرملو، خروجي آسياي نيمه خودشکن، بعد از يک مرحله جداسازي مغناطيسي شدت پايين در مورد کانسنگ مگنتيتي و چند مرحلهي جداسازي مغناطيسي شدت پايين و سپس يک مرحلهي جداسازي مغناطيسي شدت بالا در مورد کانسنگ هماتيتي، وارد آسياي گلوله اي مدارهاي مربوطه مي گردد.
بيشتر کانسنگهاي آهن ايران که مورد مصرف واحدهاي توليد فولاد قرار مي گيرند، مگنتيتي ميباشند لذا کاربرد آسياهاي گلولهاي به منظور خردايش نرم با پوشش داخلي مغناطيسي مي تواند راه حل جالبي براي خردايش پيشرفته باشد. لازم به ذکر است که معمولا بين پوشش فولادي خارجي آسيا و آسترلاستيکي، يک لايهي مغناطيس دائمي وجود دارد و در حجم آسترلاستيکي نيز مغناطيس هاي دائمي به طور يکنواخت پخش شده اند. اين امر باعث ميشود که آسترلاستيکي به جدار چسبيده و بدين ترتيب نصب آستر نياز به پيچ و مهره نخواهد داشت، از طرف ديگر وجود مغناطيس در پوشش داخلي آسيا باعث جذب ذرات نرم مغناطيسي ( سنگ آهن مگنتيتي ) در روي پوشش شده و آن را از خورندگي و فرسايش محافظت مي کند و بدين ترتيب لايهي محافظ که در روي آستر تشکيل مي شود عامل مهمي در طول عمر پوشش داخلي خواهد بود. کاربرد آستر مغناطيسي باعث کاهش ضخامت آستر و وزن آسيا مي شود و بدين ترتيب حجم مفيد آسيا افزايش يافته و مصرف انرژي آن نيز نسبت به واحد وزن محصول توليدي، کاهش مي يابد. اين نوع پوششها در آسياهايي که براي خردايش نرم به کار گرفته مي شوند و ابعاد گلوله هاي آنها نيز نسبتا کوچک است مي تواند به خوبي جانشين ساير انواع پوشش داخلي آسياها شود و شرط کاربرد آن، وجود خاصيت مغناطيسي در بار خرد شونده مي باشد که سنگ هاي آهن مگنتيتي مثال خوبي مي تواند براي اين امر باشد.


1-روش هاي فيزيکي که بر اساس اختلاف وزن مخصوص کاني با باطله ي سنگ معدن قرار دارد.
2-روش هاي مغناطيسي که بر اساس خاصيت مغناطيسي کاني هاي آهن دار به کار مي روند.
3-روش هاي فيزيکي- شيميايي که بر اساس خواص سطحي کاني هاي آهن دار قرار دارد.
4-روش هاي شيميايي که بر اساس خواص شيميايي کاني هاي آهن دار قرار دارد.
روش هاي فيزيکي:
روش هاي فيزيکي پرعيار کردن بر اساس اختلاف وزن مخصوص کاني آهن دار و باطله ي آن پايه گذاري شده اند. کاني هاي آهن دار معمولا داراي وزن مخصوص بالاتر از 4 مي باشند. باطلهي سنگ آهن معمولا از کاني هاي آهکي ( کلسيت ) با وزن مخصوص 7/2 و سيليس و کوارتز با وزن مخصوص 65/2 تشکيل شده است. بازده و کارآيي اين روش ها بستگي به اختلاف وزن مخصوص باطله و کاني دارد. از آنجايي که اين اختلاف در مورد کاني هاي آهن دار و باطله قابل توجه است لذا بيشتر روش هاي فيزيکي پرعيار کردن را مي توان در مورد سنگ هاي معدني آهن به کار برد. اين روش ها متعدد بوده و در زير به بعضي از آنها اشاره مي کنيم.
پر عيار سازي از طريق دانه بندي:
در اثر خردايش، سنگ آهن به بخش هاي مختلف دانه بندي تقسيم مي شود که توزيع آهن اين بخش ها متغير است و اين موضوع مي تواند براي پرعيارسازي کانسنگ آهن مورد استفاده قرار گيرد. توزيع آهن در بخش هاي مختلف دانه بندي بستگي به سختي کاني آهن دار و باطله ي همراه دارد. چنانچه سختي کاني آهن دار بيشتراز باطله ي همراه باشد در اثر خردايش، باطله ي بيشتر خرد شده ومقدار آهن در بخش هاي دانه ريز کم خواهد بود. وبالعکس اگر سختي باطله بيشتر باشد در اين صورت کاني آهن ددار بيشتر خرد شده و در بخش هاي دانه درشت عيار آهن پايين خواهد بود. به عنوان نمونه از سنگ هاي آهن تاکونيت مي توان نام برد که باطله ي همراه آهن بسيار سخت بوده و در اثر خردايش معمولا قسمت هاي آهن دا خرد شده و در بخش هاي درشت ( در حد سانتي متر ) عيار آهن بسيار پايين است و مي توان با سرند کردن ساده و جدا کردن دانه هاي درشت، عيار آهن را در محصول باقي مانده چند درصدي بالا برد و بالعکس در معادن آهن قيصر کاليفرنيا، باطله ي مربوطه نرم بوده و در بخش زير 75 ميکرون مقدار آهن بسيار پايين مي باشد. با نرمه گيري از محصول خرد شده و خارج کردن آن ازمسير مي توان عملا عيار آهن را بالا برد. اين روش به تنهايي براي پرعيارسازي سنگ آهن براي مصارف صنعتي کافي نبوده و و عملا مرحله ي اول پرعيار سازي را تشکيل مي دهد و محصول حاصله پس از حذف بخش فقير از آهن مجددا مورد عمليات پرعيارسازي قرار مي گيرد.
شايان ذکر است که در کارخانه ي فرآوري سنگ آهن چادرملو از روشي مشابه روش فوق الذکر استفاده مي شود. در اين کارخانه، باطلهي جداکنندههاي مغناطيسي شدت پايين پس ازطي يک سري سيکلون هاي آبگير، وارد مدار جدايش مغناطيسي شدت بالا مي شود. سيکلون هاي مذبور در اين مدار، علاوه بر وظيفهي آب گيري، نقش يک پرعيار کنندهي کانسنگ آهن از طريق دانه بندي را نيز ايفا مي کنند به اين صورت که سرريز آنها که حاوي درصد کمتري آهن است و عامل لخته سازي در مدارجداکننده ي شدت بالا مي باشد از بقيه ي مواد جدا مي شود.
پرعيارسازي از طريق مالش:
در اين روش، سنگ آهن در درون استوانهي دواري مورد عمل قرار مي گيرد. دانه هاي سنگ آهن در اثر حرکت درون استوانه روي يکديگر اثر فرسايشي داشته و باعث مي شود که کانيهايي که در سطح کاني هاي آهن دار وجود دارند از سطح جدا شده و به صورت نرمه درآيند و سپس با نرمه گيري مي توان آنها را جدا کرد. در اين مورد، عيار آهن تغيير چنداني نمي کند ولي اين روش مي تواند ناخالصي هاي نامطلوب را به خصوص زماني که اين ناخالصي ها به صورت يک فيلم نازکي بر روي سطح کاني آهن دار قرار گرفته است کم و بيش حذف کند. از اين روش براي کاهش مقدار آلومين سنگ آهن مي توان استفاده کرد. آلومين در سنگ هاي آهن اغلب به صورت رس مي باشد که داراي سختي بسيار کمي بوده و بيشتر روي کاني هاي آهن دار را به صورت نواري مي پوشاند. با فرسايش و اصطکاک دانه هاي آهن با يکديگر اين نوار نرم از روي سطوح کاني جدا مي شود. براي جدا کردن بهتر بايستي عمل مالش در محيط تر صورت گيرد. از اين روش در معادن آهن هندوستان استفاده مي شود که عيار آلومين در سنگ معدن اوليه در حدود 5 درصد بوده و به کمتر از 2 درصد کاهش مي يابد.
پرعيارسازي از طريق جيگ:
به طور کلي روش هاي فيزيکي کمتر در مورد سنگ آهن به کار برده مي شود. متداول ترين اين روش ها روش جيگ مي باشد. ذرات در اين روش با حرکت متداول آب به صورت بالارونده و پايين رونده به مدت بسيار محدودي به صورت معلق در آب درمي آيند و بر حسب وزن مخصوصشان دانه بندي مي گردند. ذرات سنگين در کف و ذرات سبک در سطح جمع مي شوند. چنانچه ذرات داراي ابعاد يکسان باشند، در اين صورت دانه بندي بر اساس وزن مخصوص انجام مي شود و ذرات با وزن مخصوص بالاتر در کف قرار گرفته و از دانه هاي با وزن مخصوص کمتر جدا خواهند شد. هر چند که اختلاف وزن مخصوص ذرات کاني و باطله بيشتر و اختلاف ابعاد ذرات کمتر باشد کارآيي جيگ بالاتر و جدايي کامل تر خواهد بود. علاوه بر دو عامل اساسي اختلاف وزن مخصوص و ابعاد، عوامل ديگري نيز مانند اثر ذرات بر يکديگر، وزن مخصوص و ويسکوزيته ي پالپ، شکل ذرات و درجه ي آزادي آنها در کارآيي جيگ موثر مي باشند. جيگ دستگاهي است که با ذرات نسبتا درشت کار مي کند و ابعاد مناسب براي آن بين 1 تا 10 ميلي متر است. در هر حال دانه بندي دقيق ذرات مهم ترين عامل کارآيي جيگ مي باشد ولي عيب عمده ي جيگ ظرفيت محدود آن است، لذا کاربرد جيگ در مواقعي مي باشد که مسئله ي سرمايه گذاري از اهميت بالايي برخوردار بوده و ظرفيت کار نيز محدود باشد.


در گذشته براي پرعيار سازي سنگ هاي آهني از ميزهاي لرزان استفاده مي شد ولي امروزه اين دستگاه ها به کلي از صنعت کانه آرايي سنگ آهن خارج شده و اسپيراال ها جانشين آنها شده اند. اسپيرال ها دستگاه هاي مارپيچي شکلي هستند که به صورت عمودي قرار دارند. ذرات سبک و سنگين به صورت پالپ نسبتا رقيق از بالا بر روي دستگاه ريخته مي شوند . ذرات سنگين در کف در تماس با سطح بشقاب قرار مي گيرند. در اثر حرکت دوراني آب، نيروي گريز از مرکزي بر روي ذرات وارد مي شود که باعث رانده شدن ذرات با وزن مخصوص کم و معلق در آب به طرف جدار خارجي دستگاه و خروج آنها از طريق روزنه هايي که در کنار بشقاب ها بدين منظور تعبيه شده اند، مي شود در حالي که ذرات با وزن مخصوص بالا در روي سطح بشقاب قرار گرفته و نيروي اصطکاکي موجود بين سطح و ذرات مانع از رانده شدن آنها به طرف جدار مي گردد و بدين ترتيب جدايي انجام مي گيرد.
شايان ذکر است که معمولا اين دستگاه ها به صورت سري قرار داده مي شوند طوري که هر سري شامل چند اسپيرال مي شود. اسپيرالها در مواقعي که درجهي آزادي کاني در ابعاد کاربردي بالا است، کارآيي مناسبي دارند. ابعاد مناسب ذرات براي پرعيار شدن در اسپيرال ها بين 1/0 تا 2 ميلي متر است. از اين دستگاه ها براي پرعيارسازي آهن در معادن کانادا استفاده مي شود.


در اين روش، يک پالپ با ذرات بسيار کوچک و با وزن مخصوص بالا معلق در آب ساخته ميشود که وزن مخصوص پالپ کمتر از وزن مخصوص کاني آهن و بيشتر از وزن مخصوص باطله ميباشد. در اثر اين پديده، دانههاي باطلهي همراه دانه هاي آهن ( با وزن مخصوص کمتر از پالپ ) شناور و جدا ميشوند. اين دستگاه ها با ذرات نسبتا درشت 1 تا 5 ميلي متر کار ميکنند. کاربرد ذرات کوچک تر باعث افزايش دانسيته و ويسکوزيتهي پالپ مي شود و بدين ترتيب مانع از جدايي باطله از کانسنگ ميشود. ذرات معلق در پالپ بايد قابليت جدايش را داشته باشند و معمولا از ذراتي تشکيل ميشوند که داراي خاصيت مغناطيسي هستند ( فروسيليسيم – مگنتيت ) و قابليت جدا کردن توسط جداکنندهي مغناطيسي و مصرف مجدد را نيز دارند. چنانچه در نظر باشد از اين روش براي پرعيار کردن سنگهاي آهن استفاده شود بايد سنگ معدن فاقد مگنتيت باشد. در غير اين صورت، بايد اين مواد توسط جداکنندهي مغناطيسي با ميدان ضعيف جدا شوند.
دستگاههاي واسطهي سنگين معمولا با پالپي با وزن مخصوص 7/2 تا 3 تن بر متر مکعب کار ميکنند و به اشکال مختلف استوانهاي و کلاسيفاير مکانيکي و سرانجام به صورت هيدروسيکلون در صنعت وجود دارند. کارآيي اين دستگاهها بستگي به درجهي آزادي کاني و ابعاد به کار برده شده دارد.
چنانچه توزيع ذرات به صورت دانه ريز باشد، دستگاه کارآيي خود را از دست مي دهد.
روشهاي مغناطيسي پرعيار کردن:
متداولترين روش پرعيارسازي سنگهاي آهن به خصوص اکسيدهاي آهني که مانند مگنتيت داراي خاصيت مغناطيسي قوي هستند، روش پرعيارسازي سنگهاي آهن به خصوص اکسيدهاي آهني که مانند مگنتيت داراي خاصيت مغناطيسي قوي هستند، روش پرعيارسازي از طريق مغناطيسي است که ارزان ترين و کارآمدترين روش پرعيار کردن و حذف ناخالصي هاي آهن ميباشد. شايان ذکر است که اکثر ناخالصيهاي کانسنگ هاي آهن مانند انواع فسفاتها و ترکيبات گوگرددار ( به استثناي پيروتيت که داراي خاصيت مغناطيسي است ) فاقد خاصيت مغنا طيسي بوده و در صورتي که درجهي آزادي مناسبي داشته باشند، جدا و حذف ميشوند. در پرعيارسازي به روش مغناطيسي، کليهي ذرات تشکيل دهندهي يک کانسنگ تحت تاثير نيروي مغناطيسي قرار ميگيرند. نيروي مغناطيسي تنها بر روي ذرات حاوي خواص مغناطيسي اعمال ميشود و نيروي ثانويه و يا ترکيبي از نيروهاي مختلف نه تنها بر روي ذرات مغناطيسي بلکه بر روي ذرات غيرمغناطيسي در جهات مختلف نيز موثرند. نيروهاي غيرمغناطيسي عمدتا شامل نيروهاي ثقلي، گريز از مرکز و مقاومت سيال مي باشند و نيروهايي نظير اصطکاک، الکترواستاتيکي ( ناشي از حرکت و مالش ذرات )، واندروالس موئينگي نيز به طور جانبي در اين فرآيند جدايش موثر ميباشند.


همان طوري که مي دانيم ضريب مغناطيس پذيري مگنتيت 3000 تا 7000 مرتبه بيشتر از کوارتز و 100 تا 2700 مرتبه بيشتر از هماتيت مي باشد. در مورد آپاتيت، اين ضريب کوچکتر بوده و نسبت ضريب خاصيت مغناطيس پذيري مگنتيت به آپاتيت بسيار بزرگتراست. لذا مي توان نتيجه گرفت که در صورت آزاد بودن دانههاي آپاتيت از مگنتيت امکان جدايي اين دو کاني از يکديگر توسط جداکنندهي مغناطيسي وجود دارد.
جداکنندههاي مغناطيسي بر اساس ميزان شدت جريان مغناطيسي مورد نياز جهت جدايش و نوع سيال به 6 دستهي زير تقسيم ميشوند:
جداکنندههاي مغناطيسي خشک با شدت کم:
از اين نوع جداکنندهها براي پرعيارسازي ذرات نسبتا درشت و شديدا مغناطيسي استفاده ميشود که به فرآيند کوبينگ نيز معروف است. اين روش ارزان و بسيار کارا بوده و ميدان مغناطيسي در آنها بيشتر دائمي ميباشد و در مواردي که کانسنگ آهن به صورت مگنتيت است متداولترين روش براي پرعيار کردن و جداسازي کانيهاي نامطلوب از سنگ آهن ميباشد. اين نوع جداکنندههاي مغناطيسي از يک استوانهي گردان تشکيل شدهاند که در داخل مجهز به 3 تا 6 آهنربا با قطبهاي معکوس نسبت به همديگر و از نوع دائم و يا ( به ندرت) الکترومغناطيسي هستند که به طور ثابت نصب شدهاند. در بعضي موارد، استوانهي دوار به عنوان يک غلطک( قرقره) عمل ميکند که در انتهاي يک نوار نقاله که از روي آن عبور ميکند، نصب ميشود. در جداکنندههايي که استوانه با سرعتي بيش از 60 دور در دقيقه ميچرخد، علاوه بر نيروي مغناطيسي، نيروي غالب، نيروي گريز از مرکز است. بر اين اساس، چنانچه چرخش استوانه کمتر از 358 دور در دقيقه باشد، ذره به بخش مغناطيسي هدايت ميشود. بنابراين با تنظيم و کنترل چرخش استوانه ميتوان به يک جدايش گزينشي دست يافت و بدين ترتيب کنسانترهي پرعياري ( باطله ي بسيار کم عيار ) را تهيه نمود. در عمل چنانچه ابعاد ذرات ريزتر از 25 ميکرون باشند، نيروي چسبندگي که ناشي از ماهيت الکترواستاتيکي بين ذرات است سبب ميشود که ذرات به همديگر بچسبند و جدايش انتخابي صورت نگيرد. در چنين شرايطي لازم است که با افزايش سرعت چرخش استوانه، دبي بار با ورودي به دستگاه نيز افزايش يابد ولي ضخامت لايهي مواد در سطح استوانه بايد ثابت بماند.


جداکننده هاي مغناطيسي خشک با شدت بالا:
در اين جداکنندهها، به منظور جدايش ذرات، نيروي جاذبهي مغناطيسي عمدتا در جهت عکس نيروهاي مخالف ( نيروي ثقل و يا گريز از مرکز ) اعمال ميشود. در اين دستگاهها ميدان مغناطيسي که روي ذرات اثر ميکند در حدود 7/0 تا 2 تسلا ( 7000 تا 20000 گوس ) ميباشد. ايجاد يک چنين ميدان مغناطيسي توسط مغناطيسهاي دائمي امکان پذير نبوده و تنها توسط عبور جريان از داخل سيم پيچ و ايجاد ميدان مغناطيسي در هستهي مرکزي آن امکان پذير است. ميدان مغناطيسي ايجاد شده در اين دستگاهها آن قدر قوي است که مي تواند ذرات با خاصيت مغناطيسي کم مانند هماتيت و سيدريت را جدا کند. اين تجهيزات معمولا گران قيمت بوده و مصرف انرژي آنها زياد مي باشد. شايان ذکر است که اين دستگاه ها کمتر کاربرد دارند. به منظور ايجاد گراديان بالا، مراحل خاصي ( با شياردار کردن روتور و يا لايه لايه کردن آن ) و يا شکل هاي مختلفي از ميدان ( دايرهاي، مارپيچي و غيره ) لازم است. از آنجا که هر سه نيروي اصلي، مغناطيسي، ثقلي و گريز از مرکز متناسب با حجم ذره است لذا، پارامتر ابعاد ذره در امر جدايش، به ويژه هنگامي که نيروهاي ثانويه نيز با اهميت هستند تاثيرگذار ميباشد.
همچنين از آنجايي که طي جدايش مواد، ذرات مغناطيسي در بار اوليه حرکتي رو به بالا دارند لذا با يک مرحله جدايش ميتوان به کنسانترهاي با عيارمورد نظر دست يافت. شايان ذکر است که اين نوع جداکنندهها براي ابعاد زير 50 ميکرون مناسب نيستند و داراي بازيابي کمتري هستند. از انواع مختلف اين نوع جداکنندهها ميتوان جداکنندهي مغناطيسي با نوار متقاطع، جداکنندهي غلطکي القايي، جداکنندهي مغناطيسي ديسکي ( حلقهاي ) و جداکنندهي مغناطيسي غلطکي با آهن رباي دائم را نام برد.
جداکنندههاي مغناطيسي تر با شدت کم:
جداکنندههاي مغناطيسي تر با شدت کم در طراحي هاي اوليهي خود به دليل پارهاي از مشکلات مانند مشکلات مربوط به تغييرات بار ورودي، نوع مخزن، شرايط جريان پالپ و اندرکنش ذرات از يک سو و عدم به کارگيري دقيق ترکيب مناسبي از شدت و گراديان ميدان مغناطيسي از سوي ديگر، در مورد جدايش کانسنگهاي حاوي مواد فرومنيتيتي چندان موفق نبوده ، ولي با پيشرفت تکنولوژي، مدل هاي تجربي خاصي براي پرعيارسازي کانسنگهاي آهن با اين نوع جداکنندهها بر اساس آزمايشهاي اوليه ي لولهي ديويس ارائه شده است.
جداکنندههاي مغناطيسيتر با ميدان ضعيف، نسبت به نوع خشک، داراي بازده بالايي ( در حدود 90 درصد ) بوده و عيار آهن در محصول خارج شدهي آن به حدود 70 درصد ميرسد. از متداول ترين انواع اين نوع جداکنندهها مي توان به نوع نواري و استوانه اي اشاره کرد. ظرفيت اين دستگاه ها به علت ريزي دانهها کمتر از حالت خشک بوده و به ازاي هر متر عرض چرخ يا نوار در حدود 15 تن در ساعت ميباشد


1-افزايش قطر و طول استوانه منجر به افزايش ظرفيت استوانهي آن ميشود.
2-افزايش گراديان مناطيسي، افزايش بازدهي و بازيابي ذرات ريز فرومنيتيتي را به دنبال دارد.
3-افزايش عمق نفوذ مواد مغناطيسي در پالپ عاملي در تسهيل بازيابي ذراتي با ابعاد درشت ميباشد.
جداکنندههاي استوانهاي :
جداکنندههاي استوانهاي از نظر نوع تانک، به سه دسته تقسيم ميشوند که عبارتند از:
1-جداکنندههاي هم جهت با جريان پالپ
2-جداکنندههاي هم جهت با چرخش استوانه
3-جداکنندههاي غير هم جهت با چرخش استوانه
جداکنندههاي هم جهت با جريان پالپ:
در اين نوع از جداکننده ها، مواد پرعيارشده در جهت حرکت پالپ جريان مي يابد و طي آن ذرات مغناطيسي جذب استوانه شده و به طرف جلو رانده مي شوند و ذرات غيرمغناطيسي از بخش انتهاي دريچهي تخليهي باطله از آن خارج ميگردند. در اين جداکنندهها، کنترل سطح پالپ اهميت خاصي دارد. کنترل سرريز، توسط موانع قابل تنظيم انجام ميگيرد و حجم سرريز بايد 10 تا 20 درصد جريان باطله باشد. بنابراين به منظور دستيابي به جددايش مطلوب لازم است که بار اوليه به طور ثابت وارد دستگاه شود تا در سطح آب تغييري ايجاد نشود. عدم کنترل دقيق سطح پالپ، تلفات مواد مغناطيسي در باطله را به دنبال دارد. از اين نوع جداکنندهها براي پرعيارسازي ذرات ريز 8 ميلي متر استفاده ميشود. شدت ميدان مغناطيسي ايجاد شده و درصد جامد پالپ ورودي در اين جداکنندهها به ترتيب تا 7/0 تسلا و مابين 30 تا 50 درصد وزني مي باشد.
جداکنندههاي هم جهت با چرخش استوانه:
در اين نوع جداکنندهها، بار اوليه از يک محفظهي مخصوص عبور مي کند و جهت چرخش استوانه مخالف جهت جريان پالپ است. ذرات مغناطيسي در بدو ورود جذب استوانه ميشوند و تخليهي باطله نيز سريع صورت مي گيرد. از آنجايي که باطله به طور کامل در طول قوس ميدان مغناطيسي جريان مييابد لذا ميزان تلفات مواد مغناطيسي کمتر است. ابعاد بار اوليه بايد کوچک تر از 5 ميلي متر و حجم سرريز بايد 10 تا 20 درصد کل جريان باطله باشد. اين نوع جداکنندهها با اينکه داراي بازيابي و ظرفيت بالايي هستند ولي تنها براي مراحل کوبينگ ( کوبر ) و اوليه ( رافر ) پرعيارسازي استفاده ميشوند و محصول کنسانترهي حاصله در اين جداکنندهها بايد مورد شستشو قرار گيرد و لذا در مواردي که کنسانترهاي با کيفيت بالا مد نظر باشد به کار گرفته نميشوند.
جداکنندههاي غير هم جهت با چرخش استوانه:
در اين نوع جداکنندهها که به جداکننده هاي استيفن سون معروفند، جريان پالپ مخالف جهت چرخش استوانه است. بار اوليه نزديک به انتهاي استوانه وارد و سپس ذرات مغناطيسي جذب استوانه شده و با آب شستشو خارج ميشوند، ولي باطله از بخش انتهايي و مخالف حالت قبل از تخليه خارج مي گردد. چنين جرياني از باطله سطح پالپ را نيز کنترل ميکند. جداکننده هاي استيفن سون جداکنندههاي مناسبي براي پرعيارسازي ذرات غير مگنتيتي زير 800 ميکرون بوده و در مراحل شستشو و نهايي پرعيارسازي مورد استفاده قرار مي گيرند.
لازم به ذکر است که جداکنندههاي مغناطيسي مدار مگنتيت کارخانهي کانه آرايي آهن معدن چادرملو از نوع شدت پايين و يا متوسط ( در بخشي از خط توليد شماره ي 2 ) و هم جهت با جريان پالپ مي باشد.
اين جداکنندهها، تفاوتهاي زيادي با سه نوع عنوان شده در بالا دارند. به عبارت ديگر در اين نوع، پالپ از داخل ماتريس عبور ميکند ولي در موارد قبلي، بار اوليه از سطح نوار نقاله و يا غلطک( استوانه ) عبور داده ميشود. ماتريس وسيلهاي است که اجزاي اصلي آن را مواد فرومنيتيتي با شکلي خاص تشکيل ميدهند و توسط يک ميدان مغناطيسي خارجي خاصيت آهن ربايي به خود مي گيرد. جداکنندهي جونز از مهمترين اين نوع جداکنندهها ميباشد. اين جداکننده از يک بخش گردان تشکيل شده است که در داخل آن يک سري جعبههايي در ميدان مغناطيسي قوي وجود دارد و درون آنها صفحات و يا اليافي از آهن نرم قرار گرفتهاند. مواد مغناطيسي جذب اين الياف شده و مواد غيرمغناطيسي جذب آنها نشده و و جدا و خارج ميشوند. در اثر گردش، بخش گردان اين جعبه ابتدا به قسمت شستشوي اوليه ميرسد که آب با فشار کم بر روي مواد جذب شده اثر ميکند و مواد نيمه مغناطيسي را از روي الياف يا صفحات به عنوان محصول مياني جدا ميکند .


شدت ميدان مغناطيسي بر روي ذرات بستگي به فاصلهي ذرات از منبع ميدان مغناطيسي دارد و با افزايش اين فاصله شدت ميدان به شدت کاهش مييابد. به هر حال مناسبترين فاصله در حدود 1 تا 2 سانتي متر ميباشد. جنس دستگاه و به خصوص قسمتهايي که در جوار منبع مغناطيسي قراردارند بايد از مواد غيرمغناطيسي ( فولاد استينتي، مواد سراميکي و ... ) باشند و اين امر باعث گران تمام شدن قيمت اين نوع دستگاهها مي شود. در صنعت، انواع و اقسام ديگري از جداکنندههاي مغناطيسي وجود دارد که اساس آنها يکسان بوده و در پارهاي از مشخصات مانند سيستم باردهي و سيستم شستشو و غيره با يکديگر تفاوت دارند.


به طور کلي دستگاههاي تر نسبت به دستگاههايي که به صورت خشک کار ميکنند مزيت فراوان دارند. به خصوص بازده اين دستگاهها و عيار محصول حاصله بالاتر ميباشد. در عوض، مصرف انرژي اين دستگاهها زياد بوده و به علاوه محصول حاصله بايد بعدا خشک گردد.
از انواع مختلف ديگر اين نوع جداکنندهها ميتوان جداکنندههاي مغناطيسي گيل، جان، کرپکو و کروپ سول را نام برد.
جداکنندههاي مغناطيسي تر با گراديان زياد:
بسته به ميزان مواد مغناطيسي موجود در بار اوليه، اين جداکنندهها در دو مدل پيوسته و غير پيوسته ساخته ميشوند و نسبت به ديگر جداکنندههاي مغناطيسي در سالهاي اخير توجه بسياري از افراد را به خود جلب کردهاند. از پارامترهاي موثر در بازدهي جدايش اين نوع از جداکنندهها مي توان به تاثيرپذيري مغناطيسي ذرات، توزيع ابعادي بار اوليه، شدت ميدان مغناطيسي، نوع و ارتفاع بارگيري ماتريس، حجم و شدت جريان آب شستشو و آب تحت فشار و بالاخره آماده سازي باراوليه اعم از نرمه گيري، تفرق، پايداري ذرات، pH و حذف ذرات فرومنيتيتي از بار اوليه اشاره کرد. از متداولترين انواع جداکنندهها مي توان به جداکنندههاي مغناطيسي با گراديان زياد آريز، مدل باکس مگ، مدل پيوسته ( سالا- کاروسل مدل پيچک ) و مدل غير پيوسته اشاره کرد. شايان ذکر است که جداکننده ي مغناطيسي موجود در مدار هماتيت کارخانهي کانه آرايي معدن چادرملو از نوع پيوستهي سالا- کاروسل مي باشد.

استفاده از جداکنندههاي مغناطيسي با گراديان زياد در صنايع فرآوري مواد معدني کاربرد وسيعي داشته ولي استفاده از آنها معايبي را نيز به دنبال دارد که از آن جمله ميتوان به موارد زير اشاره کرد:
1-مشکل گرفتگي مجراها در اثر اشباع مغناطيسي و غير کارآمد بودن عمل شستشو در جدايش ذرات فرو و فري منيتيتي از ماتريس
2-مشکلات مربوط به نصب آنها به دليل سنگيني و حجيم بودن آنها
3-مصرف بالاي آب و نياز به آبي غير يونيزه جهت دستيابي به حداقل ميدان مغناطيسي
اين جداکنندهها که از جنس آلياژهايي که از نوع نيوبيوم- تانتاليوم هستند و قادر به ايجاد ميداني تا 14 تسلا ميباشند که اين مقدار در مقايسه با مقادير مربوط به جداکنندههاي ديگر کاملا قابل محسوس است و در مدلهاي متعددي همچون ابررساناهاي ماتريسي و جداکنندههاي گراديان باز طراحي ميشوند
روشهاي پرعيارسازي از طريق فلوتاسيون :
صنعت فراوري مواد معدني در ده سال گذشته شاهد پيشرفتهاي چشمگيري بوده است كه بدون ترديد، سلول فلوتاسيون ستوني يكي ازبارزترين آنها ميباشد. با اينكه سلول فلوتاسيون ستوني در اوايل دهه پنجاه ميلادي براي اولين بار مطرح گرديد. ولي به دليل مشكلات فني و عمليات خاص تا اواخر دهه هشتاد در صنايع معدني جايگاه خوبي نداشت . دهه نود ميلادي دوران شكوفايي سلول ستوني بود تا جايي كه از آن براي فراوري اكثر مواد معدني از جمله زغال سنگ ، مس، سرب، موليبدن و ححتي مركبزدايي از كاغذهاي باطله به طور وسيع استفاده ميشود. امروزه به ندرت ميتوان كارخانه فرارويمواد معدني پيدا كرد كه در مدار فلوتاسيون خود از سلول ستوني استفاده نكرده باشد.

ماشينهاي مكانيكي اولين سلولهاي هستند كه در كارخانهجات فلوتاسيون مورد استفاده قرار گرفتهاند. اين ماشينها از سه قسمت تشكيل شدهاند.
1-سلول فلوتاسيون با شكل مشخص هندسي ( متوازي سطوح ويا استوانهاي) كه نشاندهنده شكل كلي سلول است
2-وسيلهاي براي هدايت جريان هوا به داخل سلول (ديافراگم، منتشر كننده، شفت با محور توخالي)
3-روتور و استاتور كه به ترتيب نقش همزن و كنترل كننده تلاطم محيط پالپ در بخش فوقاني سلول را به عهده دارند.
ماشينهاي مكانيكي بايستي به انجام عمليات زير باشند.
1-ذرات را به حالت تعليق درآورند
2-حبابهاي هوا را در محيط پالپ پراكنده سازند
3-شرايط مناسب را براي تماس بين ذرات آبران و حبابهاي هوا ايجاد كنند
4-انتقال كليه ذرات وارد شده به داخل سلول را به دو بخش كنسانتره و باطله هدايت كنند.
5-امكان انتقال سريع ذرات قبل از خردايش، بر اثر سايش در اطراف همزن
6-ايجاد محيطي نسبتاً آرام در بخش فوقاني سلول به منظور جلوگيري از رها شدن ذرات آبران از سطح حباب
7-قدرت كافي براي متفرق كردن مجدد ذرات پس از قطع برق
8-كنترل ارتفاع ستون كف و سطح پالپ در داخل سلول
9-كنترل حباب هوا و كاهش ابعاد درشت به ابعاد ريز
10-كنترل انرژي و نگهداري ساده
11-خروج مرحلهاي ذرات درشت باطله كه ممكن است به سختي به بخش باطله حمل شود
12-تجهيزات لازم براي انتقال كف به مراحل شستشو و يا باطله به بخش رمقگير


معروفترين شركتهاي سازنده اين سلولها عبارتند از دنور، گالگير، ويمكو، اتوكمبا و سالا هستند.
استفاده از سلول مكانيكي در صنعت فرآوري مواد معدني عموماً با مشكلاتي از قبيل موارد زير مواجه است
1-روشهاي بسيار مختلف طراحي و عدم شناخت مزيت هر كدام از اين روشها
2-عدم كنترل دقيق هوادهي و در نتيجه آشفتگي در سلول
3-غير قابل پيش بيني بودن بزرگ مقياس كردن آنها
4-نياز به اپراتوري مداوم و دقت وتوجه زياد به عملكرد متالوژيكي آنها
5-فرسوده شدن سريع آنها
6-عدم وجود استراتژي كنترل كلي مناسب .
تاريخچه سلول ستوني :
اولين ستون فلوتاسيون دراوايل سال 1960 توسط بوتين اختراع شد. توصيف اوليه ستون و آزمايشهاي مربوطه توسط ولر 1966 و بوتين 1967 ارائه شد. اين طرح گاهي ستون كانادايي ناميده ميشود.
اولين آزمايشهاي ستوني جهت بازيابي سيليس از آهن طي فلوتاسيون معكوس در مراحل سلولهاي اوليه – رمق گير به انجام رسيده است. كنسانتره آهن توليدي از اين ستون نسبت به كنسانتره بدست آمده در مراحل اوليه و رمق گير در سلولهاي معمولي بهتر است همچنين سريز حاصله بهتر از سريز توليد شده در چند مرحله از سلولهاي شستشو بوده است . بنابراين، استفاده از ستون در مرحله شستشو نتايج بهتري را نسبت به سلول مكانيكي پديد ميآورد.

بزرگ مقياس كردن ستون به سرعت از قطر 2 اينچ به قطر 12 اينچ توسط كمپاني كانادايي Iron ore صورت پذيرفت. در آن موقع اين كمپاني تنها استفاده كننده از ستون در كانادا در زمينه كانسنگ آهن بوده است تا اينكه يك توليد كننده مس در كانادا نمونههاي از كانسنگ سولفيدي را جهت آزمايش به كمپاني ارسال نمود . با حصول نتايج بهتر استفاده از ستون فلوتاسيون صنعتي در ابعاد بزرگ به قطر 36 اينچ توسط توليد كننده مس در كانادا خريداري شد . با صورت گرفتن آزمايشهاي مختلف و تغييرات متعدد نهايتاً ستون اصلاح شدهاي به قطر 18 اينچ ارائه گرديد. اولين كاربرد ستون اخير در مراحل اوليه – رمق گير بود كه در اين مرحله باطلهاي توليد ميشد كه معادل باطله نهايي كارخانه بود و همچنين كنسانتره اوليه رمق گير معادل كنسانتره نهايي كارخانه بود. سرانجام از ستون در مرحله كلينر استفاده شد . و كنساتره بدست آمده كه عيار عيار آهن آن 5 درصد بيشتر از كنسانتره نهايي كارخانه بود .
4- ظرفيت زياد هر واحد عملياتي:
در سلولهاي فلوتاسيون مكانيكي اختلاف ايدهآل پالپ باعث ميان بر زدن پالپ ميشود كه اين باعث رقيق شدن كنسانتره با كانيهاي باطله ، ته ريز با كانيهاي با ارزش ميگردد. در سلول فلوتاسيون غير هم جهت به دليل جريان پيستوني پالپ و حبابهاي هوا ، در ناحيه بازيابي ميان بر زدن مواد اتفاق نميافتد. به دليل كارآيي متالوژيكي بهتر فلوتاسيون ستوني ، يك ستون ميتوان جايگزين يك رديف سلول مكانيكي گردد. كه در نتيجه اين كار مدارهاي پيچيده سلولهاي معمولي ساده ميشود.
5- بزرگ مقياس كردن نامحدود:
بزرگ مقياس كردن سلولهاي فلوتاسيون تا حد معيني داراي دقت مطلوب است و بالاتر از آن اندازه بزرگ مقياس كردن به دليل هيدروديناميك پيچيده پالپ امكانپذير نيست. از طرف ديگر بزرگ مقياس كردن ستون فلوتاسيون ستوني تنها مستلزم عمليات ساده رياضي است و هيچ تغييري در اساس مكانيزم فلوتاسيون ايجاد نميكند. بنابراين ميتوان گفت كه هيچ حدي براي بزرگ مقياس كردن ستون فلوتاسيون وجود ندارد . اين موضوع براي كارخانهجات فراوري جديد كه بايد سنگهاي معدني با عيار پايين و تناژ زياد را عمل آوري كنند مهم است.
جهت كاهش هزينههاي ماشينهاي فلوتاسيون روند كنوني به سمت توليد ماشين هاي بزرگ پيش ميرود. همانطور كه در بالا اشاره شد ستونهاي فلوتاسيون را بدون هيچگونه محدوديت ميتوان بزرگ مقياس كرد و ماشينهاي فلوتاسيون بزرگي را توليد كرد. همچنين ستون هيچ مكانيزم اختلاط مكانيكي ندارد كه اين سبب حذف موارد هزينه بر از قيبل موتورهاي الكتريكي و همزنهاي ويژه مقاوم در مقابل فرسايش ميشود. بعلاوه شرايط آرام داخل ستون ، نياز به ديوار هاي داخلي مقاوم را مرتفع ميسازد. اين عوامل سبب كم هزينه بودن ستون فلوتاسيون ميشوند. هزينه ها را با بكارگيري ستونهايي با مقطع دايرهاي به جاي مستطيلي ميتوان بيشتر كاهش داد.
7-اشغال فضاي افقي كم
به دليل اينكه ستون فلوتاسيون يك واحد عموديست كاربرد آن در كارخانههاي جديد به واسطه كم كردن سطح مورد نياز، سرمايهگذاري اوليه را كاهش ميدهد. زمانيكه به دليل خاص طراحي متراكم و استفاده هر چه بيشتر از فضاي كارخانه مورد نياز باشد. با جايگزين كردن ستونهاي بجاي ماشينهاي فلوتاسيون مكانيكي معمولي ،در صورت نياز ميتوان براي افزايش ظرفيت مدار از فضاي بدست آمده استفاده كرد.
شايان ذکر است که فرآوري سنگ فسفات حاوي مدول هاي کلوفان نياز به عمليات نرمه گيري دانه هاي زير 150 مش دارد و اين در حالتي است که مقدار قابل توجهي از کل P2O5 در اين بخش متمرکز است. همچنين در فلوتاسيون کلوفان بايستي از روغن هاي هيدروکربني خنثي استفاده شود و آماده سازي پالپ با دانسيتهي بالا صورت گيرد که اين به تخلخل و سطح مخصوص بالاي کلوفان برميگردد. لازم به ذکر است که آپاتيت نسبت به کلوفان بسيار نجيبتر بوده و حتي بدون اين شرايط نيز به خوبي فلوته ميشود. مطالعات الکتروسينتيک نشان ميدهد که ZPC آپاتيت در pH=5-8 و ZPC هماتيت در 6/8 – 7/6 = pH قرار دارد. بنابراين در pH بين نقطهي بار صفر آپاتيت و هماتيت از يک کلکتور کاتيوني جهت فلوتاسيون آپاتيت ميتوان استفاده کرد. سطح هماتيت در <pH هماتيت ZPC بار منفي دارد که در اين حالت يون هاي آمين با بار مثبت بر روي آن جذب ميشوند. فلوتاسيون انتخابي آپاتيت از هماتيت ( همانند مدار فرآوري هماتيت کارخانه ي کنسانتره ي آهن معدن چادر ملو ) ميتواند با بازداشت انتخابي هماتيت توسط سيليکات سديم تحت شرايطي خاص انجام پذيرد که بستگي به وجود مقادير مناسبي از سيليکاتهاي پليمريزه و ( يا ) ذرات ريز سيليس کلوئيدي با دانههاي ريز در محلول سيليکات دارد


شايان ذکر است که حضور سيليکات سديم داراي مزيتهاي ديگر هم ميباشد که عبارتند از:
1-کف ايجاد شده نسبت به حالت قبل پايدارتر خواهد بود زيرا سيليکات سديم باعث ايجاد يک پوشش محافظ بر روي حبابهاي هوا شده و با افزايش ويسکوزيتهي سطح، پايداري بيشتر کف را باعث ميشود.
2-باعث افزايش نرخ فلوتاسيون فسفات شده و جدايي انتخابي را افزايش ميدهد.
از جملهي بازدارندههاي ديگر به کاررفته به عنوان بازدارندهي اکسيدهاي آهن در فلوتاسيون معکوس هماتيت و بازدارندهي باطله ( کربناتها و کانيهاي آهن دار همراه ) در فلوتاسيون مستقيم آنيوني آپاتيت ميتوان به انواع نشاستهها اشاره نمود. ترکيب نشاسته به صورت (C6H10O5)n مي باشد که n تعداد واحدهاي دي گلوکز ( بالغ بر 100 واحد ) است. تاثير و مکانيزم واکنش مابين نشاسته و هماتيت در فلوتاسيون کانسنگ آهن همراه با باطلهي سيليکاتهي توسط آقايان مونتس- سوموتوماريو، هاوت و کونگولو بررسي شده است.

دلايل اين عمل انتخابي، توانايي خوب سطح هماتيت جهت تشکيل باندهاي هيدروژني با بازدارنده و همچنين اين حقيقت است که سطح کوارتز بساير منفي تر از سطح هماتيت بوده و ماکروملکولها به آرامي در اثر جذب OH- ، منفي ميشوند.
-ترکيب آميلوس که پليمري خطي مشخص کنندهي واحدهاي دي گلوکز به هم متصل شده توسط باندهاي 4 و آلفا منهاي يک گلوکوزيديک است.
-ترکيب آميلوپکتين که پليمري مشتق گرفته شده با زنجيرهاي حاصل از اتصال شاخه ها به هم توسط باندهاي 6 و آلفا منهاي يک گلوکوزيديک است. شايان ذکر است که آميلوپکتين با ملکولي مشتق گرفته شده و بزرگ تر در آزمايشهاي ميکروفلوتاسيون، بازدارندهي مفيدي براي هماتيت نسبت به آميلوس ميباشد. بر اساس تحقيقات آزمايشگاهي مشخص شده که در يک حالتي از کانسنگ، هيچ گونه نشاستهي تعديل شدهاي به کارآيي آميلوپکتين وجود ندارد.

فلوتاسيون تيپيك
لازم به ذکر است که ترکيب نفت در نشاستهها، نقش عمدهاي در سيستمهاي فلوتاسيون بازي ميکند. نفت نام گروهي از ترکيبات تري اکريل در گليسرون ميباشد. اثرات بازدارندگي نفتي با خلوص بالا، در نشاستهها بر کفهاي فلوتاسيون در بسياري از کارخانجات فرآوري کانسنگهاي آهن در کشورهاي برزيل و ... به اثبات رسيده است. شايان ذکر است که اين روند بر حسب نوع کانسنگ متغير ميباشد. به طور تجربي، توصيهي حد بالايي از نفت در نشاستههاي مورد مصرف جهت بازداشت کانسنگهاي آهن در سيستمهاي فلوتاسيون به مقدار5/1 درصد معقول به نظر ميرسد. پروتئينها، پليمرهايي با وزن ملکولي بالا و متصل شده به هم به وسيلهي زنجيرههاي آمينو اسيد توسط باندهاي پپتيد ( پپتيدها ترکيبات Amides-NHCO حاصله از واکنش مابين آمين و آمينواسيدها هستند ) از جمله بازدارندههاي هماتيت در فلوتاسيون معکوس هستند. شايان ذکر است که دادنباو، نام گروهي از پروتئينهاي بازدارندهي طبيعي آلي ميباشد. آقاي کوري نشان داده است که ژلاتين، محصول فرعي ذرتي شامل 63% پروتئين و 17% نشاسته، يک مادهي بازدارندهي هماتيت ميباشد. با اين وجود، ژلاتين نسبت به پروتئينهاي بسيار دانه ريز داراي کارآيي کمتري ميباشد.
فلوتاسيون با کلکتورهاي آنيوني :
براي پرعيارسازي سنگهاي آهن از روشهاي مختلف فلوتاسيون مستقيم ( با استفاده از کلکتورهاي آنيوني ) نيز ميتوان استفاده کرد. اکسيدها و سيليکات ها توسط تعداد زيادي از کلکتورهاي آنيوني مانند کربوکسيلاتها ( اسيد هاي چرب )، سولفوناتها و بعضي از معرفها قابل فلوتاسيون هستند. اسيد اولئيک و اسيد آبتيک که بخش اصلي روغن تال را تشکيل ميدهند به طور گسترده مورد استفاده قرار ميگيرند. جذب اين کلکتورها ممکن است به طريقه ي فيزيکي يا شيميايي صورت گيرد. کلکتورهاي مصرفي در مورد کانيهاي آهن معمولا اسيدهاي چرب ميباشند. تجربه نشان داده است که سولفوناتهاي نفتي کلکتورهاي مناسبي براي شناورسازي هماتيتها ميباشند. در حالي که اين کلکتورها براي شناورسازي اکسيدهاي آهني آبدار مانند ليمونيت تاثير چنداني ندارد.

در مورد جدايش هماتيت از ناخالصيهاي همراه، دو روش صنعتي زير پيشنهاد شده است:
-فلوتاسيون مستقيم هماتيت در pH هاي 2 تا 4 (ZPC>pH) با استفاده از سولفوناتها.
-فلوتاسيون مستقيم هماتيت در pH هاي 6 تا 8 با استفاده از اسيدهاي چرب.
آقايان هان و همکاران(1973) با اندازه گيري ZPC هماتيت، جذب شيميايي اسيد لوريک به هماتيت در ZPC<pH را پيش بيني کردهاند. همچنين آنها پي بردند که در ZPC>pH و با به کارگيري اسيد لوريکي با غلظت 10 مولار، بار منفي بر سطح هماتيت به وجود ميآيد. همچنين آنان طبق مطالعات بسياري که بر روي مکانيزم جذب اسيد اکتيل هيدروکسامات بر هماتيت انجام دادند بدين نتيجه رسيدهاند که مکانيزم جذب مذکور از نوع شيميايي ميباشد.
آقايان باکلند و همکاران (1980) با بررسيهايي که انجام دادند به جذب يونهاي لورات بر سطح هماتيت که بر حسب مقدار pH ميتواند شيميايي و يا فيزيکي باشد، پيبردند.
آقايان لاسکاوسکي و همکاران (1988) يک سري تحقيقات بر مبناي ZPC انجام دادهاند که در اين راه، پتانسيل زتاي مورد نياز جهت ته نشيني فقط اسيد لوريک را مورد اندازه گيري قرار دادند و به اين نتيجه رسيدند که نقطهي ايزوالکتريک هماتيت و اسيدلوريک به ترتيب نهايتا 6 و 3 ميباشد. همچنين آنها به اين مطلب پيبرده اند که اتصال هماتيت- اسيد لوريک در 3<pH<6 ثابت نبوده و دائما در حال تغيير ميباشد.
جذب شيميايي کلکتورها با وزن ملکولي بالا بر روي اکسيدها و سيليکاتهاي آهن ناشي از هيدروليز کاتيونهاي اين کانيها است. کمپلکسهاي هيدروکسي بر روي سطح فعال تشکيل شده و در حقيقت کمپلکسهاي هيدروکسي حتي بر روي سطوح با بار مثبت جذب ميشوند.
. بر اين اساس، مکانيزم جذب براي کاتيون فلزات چند ظرفيتي به سه گونهي زير پيشنهاد شده است:
1-تشکيل آب به وسيلهي ترکيب يون هيدروکسيل کمپلکس هيدروکسي با يون هيدروژن جذب شده.
2-پيوند هيدروژني کمپلکس هيدروکسي با سطح.
3-تشکيل و جذب هيدروکسيد فلز بر روي سطح جامد
تحقيقات آزمايشگاهي زيادي بر روي فلوتاسيون هماتيت از کانهي آهن با استفاده کلکتور اسيد اولئيک و يا اولئات سديم و پتاسيم انجام شده است. همچنين فلوتاسيون هماتيت با استفاده از اسيد دودکانوئيک ( اسيد لوريک )، دودکانوئيک هيدروکسامات، سديم دودسيل سولفونات (SDS) و سديم دودسيل بنزيل سولفونات (SDBS) و نمک هاي دودسيل آمين مورد بررسي قرار گرفته شده است.
پرعيارسازي از طريق فرآيند اسيدشويي:
توزيع فسفر در کل کانسنگهاي آهن به خصوص کانسنگ گوتيت، روشهاي فيزيکي پرعيارسازي را غيرموثر جلوه داده و به کارگيري روشهاي جدايش شيميايي از طريق اسيدشويي را موجب شده است. فاز فسفر در هماتيت نسبت به گوتيت، روش هاي فيزيکي پرعيارسازي را غيرموثر جلوه داده و به کارگيري روش هاي جدايش شيميايي از طريق اسيدشويي را موجب شده است. فاز فسفر در هماتيت نسبت به گوتيت داراي حلاليت کمتري مي باشد. گوتيت مي تواند در اثر عمل برشته شدن به هماتيت تبديل شود که همين امر موجب آن خواهد شد که کانسنگ بهتر در يک اسيد شسته شود. در روند برشته شدن دو عامل دما و زمان برشتهشدن نقش اساسي را ايفا مي کنند. همچنين شايان ذکر است که غلظت اسيد مصرفي نقش اساسي در بازيابي آهن داشته و نبايد از يک حد بهينه اي زياد باشد.

-فسفرزدايي کانسنگ آهن پرفسفر منطقه ي پيلبارا واقع در غرب استراليا: آقايان گودن و همکاران با توجه به اينکه مقدار بيشتري فسفر موجود در کانسار در فاز درگير با گوتيت است روشهاي شيميايي را به جاي روشهاي فيزيکي پيشنهاد داده اند. آنان با به کارگيري اسيدهاي مختلفي همچون اسيد سولفوريک، اسيد نيتريک و اسيد هيدروکلريک و محلولهاي هيدروکسيد سديم، مقدار فسفر کانسنگ را از 12/0 درصد تا 05/0 درصد کاهش دادند. زمان بهينهي برشته شدن در اين تحقيق نيم ساعت و دماي ليچينگ مابين 40 تا 60 درجهي سانتي گراد، غلظت اسيد حداکثر 2/0 مولار تعيين شده بود.
-آقاي وانگ مقدار فسفر کانسنگ آهني در چين را در اثر فرآيند اسيدشويي همراه با باکتري تيوباسيلوس و اسيد نيتريک به ترتيب از 36/0 تا 18/0 و 05/0 درصد کاهش داده است.
جداسازي مايع از جامد:
اکثر روشهاي پرعيارسازي سنگ اهن به روش تر مي باشد. اصولا روش هاي خشک پرعيارسازي سنگ آهن داراي راندمان بالايي نميباشند. فقط گاهي اوقات در مورد سنگ آهن دانه درشت از جداکنندهي مغناطيسي خشک استفاده مي شود. در روشهاي تر، محصول پرعيارشدهي نهايي همراه با مقدار قابل توجهي آب ميباشد که رطوبت آن را بايد توسط روشهاي مختلف بي آب کردن در چند مرحلهي متوالي به حدي کاهش داد که براي حمل و نقل و يا عمليات صنعتي بعدي مناسب باشد. به طور کلي، عمليات بي آب کردن و کاهش رطوبت کنسانترهي آهن به سه مرحله تقسيم مي شود که شامل عملياتهاي ته نشين کردن، فيلتر کردن و خشک کردن ميباشد.
ته نشين کردن، اولين مرحله در جداسازي فاز مايع از جامد ميباشد که عملا قسمت عمدهي فاز مايع از محصول نهايي جدا ميشود. به طور کلي مقدار آب بازيابي شده به 75 تا 80 درصد آب موجود در محصول نهايي پرعيار شده در اين مرحله ميرسد.
در اين روش از اختلاف وزن مخصوص مايع و جامد استفاده ميشود. هرقدر اين اختلاف وزن مخصوص بيشتر باشد سرعت ته نشين سريع تر بوده و بازيابي مايع، کامل تر وبيشتر خواهد شد. عوامل موثر ديگري نيز در ته نشيني ذرات آهن موثر ميباشند که در بين آنها ميتوان از اثر ابعاد ذرات، شکل آنها و وجود مواد کف کننده و کلوئيدي نام برد. هر يک از عوامل مذکور ميتوانند سرعت ته نشيني ذرات را کاهش داده و يا به کلي متوقف کنند. رسوب ذرات ريز عملا بسيار کند بوده و وجود مواد کف کننده ميتواند باعث جذب حباب هوا بر روي سطوح ذرات شده و مانع از رسوب آنها گردد. سرانجام خاصيت کلوئيدي ذرات ميتواند آنها را به صورت معلق نگه داشته و بدين ترتيب زمان رسوب آنها را بسيار طولاني کند. شايان ذکر است که در کارخانهي کانه آرايي آهن معدن چادرملو از اين روش در قسمت هاي مختلف شامل انواع مختلف تيکنرها جهت افزايش غلظت مواد ورودي مدار فلوتاسيون و مدار فيلتراسيون و همچنين افزايش غلظت باطلهي خروجي کارخانه در جهت کاهش مصرف آب استفاده مي شود.
اضافه کردن بعضي از مواد شيميايي در هر يک از حالت هاي فوق باعث رفع مشکل و تسريع ته نشيني ميشود، مثلا ممکن است تنظيم pH و يا افزودن مواد شيميايي باعث تجمع ذرات ريز و رسوب سريع آنها شده و همين روش ميتواند باعث حذف کف شود و بدين ترتيب رسوب ذرات تسهيل يابد. در هر حال روش ته نشين کردن ذرات، نسبتا ارزان و داراي ظرفيت بالايي ميباشد. عمليات رسوب و جداسازي در تيکنرها انجام ميشود. به منظور تسهيل خروج ذرات جامد از تيکنرها، کف حوضچهي تيکنر داراي شيب بوده و يک سيستم پاروي گردان ذرات راسب شدهي کف را توسط پرههاي خود به قسمت خروجي هدايت ميکند.
در مورد سنگهاي آهن ميتوان گفت که اين مواد داراي وزن مخصوص بالايي بوده و عملا رسوب آنها در تيکنر نسبتا ساده و سريع ميباشد. مخلوط آب و جامد وارد شده به تيکنر ميتواند درصدهاي جامد متفاوتي داشته باشد ولي به طور معمول در مواد خارج شده از دريچهي مرکزي تيکنر درصد مواد جامد حدود 50 تا 65 درصد خواهد بود.
امروزه تيکنرهايي که به نام لاملار معروف هستند وارد صنعت فرآوري آهن شده اند. اين دستگاه از يک سري صفحات با شيب 45 تا 60 درجه تشکيل شده اند که فاصلهي بين اين صفحات در حدود 50 تا 75 ميلي متر ميباشد. مزيت اصلي اين دستگاهها افزايش سطح رسوب به ازاي واحد سطح و همچنين عدم نياز به سيستم گردانندهي پارو و سرانجام حجم و جاي گيري بسيار کمتر آن است. شايان ذکر است که تفاوت بارز ميان اقسام مختلف از اين نوع تيکنر در صنعت اغلب در سيستم باردهي آن ميباشد.
جداسازي از طريق فيلتر:
محصول خروجي از تيکنر هنوز حاوي مقدار قابل توجهي آب ميباشد، لذا براي کاهش رطوبت، از فيلتر استفاده ميشود. عبور آب از سطح فيلتر در اثر ايجاد اختلاف فشار در دو طرف آن ميسر است به طوري که آب از طرفي که فشار بيشتر است به سمتي که فشار کمتر است رانده ميشود. با عبور آب از فيلتر، ذرات جامد در روي سطح فيلتر لايهاي را تشکيل ميدهند که مانع از عبور آسان ملکول آب شده و براي عبور نياز به فشار بيشتري خواهد بود و در نتيجه با ضخيم شدن قشراين لايه، عمل فيلتر کردن ديگر مقرون به صرفه نبوده و بايستي متوقف گرديده و لايهي گل را از سطح آن جدا کرد. غلظت جامد در پالپ يکي از عوامل اصلي در فيلتر کردن بوده و با کاهش مقدار جامد در پالپ مصرف انرژي و ظرفيت فيلتر کاهش مييابد، لذا فيلتر کردن مخلوطهاي رقيق در بيشتر موارد مقرون به صرفه نميباشد و بدين جهت قبل از فيلتر کردن از تيکنر به منظور رساندن غلظت مواد جامد به حد مناسب استفاده ميگردد.

در فيلترهاي خلا مقدار اختلاف فشار در دو طرف صفحهي فيلتر محدود بوده و معمولا از 500 تا 600 ميلي متر جيوه تجاوز نميکند و با توجه به اهميت اين اختلاف فشار در کارآرايي فيلتر، در صنعت فيلترهاي فشاري ساخته شده اند که مخلوط آب و و ذرات جامد را با فشار به سطح فيلتر وارد ميکنند. شايان ذکر است که اختلاف فشار در نوع معمولي اين فيلترها حدود 10 تا 15 اتمسفر بوده و در نوع لولهاي تا 100 اتمسفر نيز ميرسد. سرانجام از فيلتر شني ميتوان نام برد که عبارت است از لايهاي شني با دانه بندي معين که بيشتر براي صاف کردن آب و حذف مواد معلق آن به کار برده ميشود.

-کاربرد فيلتر خلاء همراه با تزريق بخار آب خشک به داخل فيلتر استوانه که ميتواند رطوبت باقي مانده در محصول را تا حدود 3 تا 4 درصد کاهش دهد.
-کاربرد توام فيلتر خلاء همراه با کاربرد هواي فشرده ي خشک. در اين روش در اثر عبور هواي خشک از لابه لاي بار با فشار نسبتا زياد، رطوبت محصول به کمتر از 8 درصد کاهش مييابد.
در هر حال مقدار رطوبت محصول کنسانترهي آهن فيلتر شده به طور معمول 8 تا 15 درصد ميباشد.
جداسازي از طريق خشک کردن:
روشهاي ته نشين کردن و فيلتر کردن قادر به حذف تمامي آب کنسانتره نبوده و همواره مقداري آب در محصول نهايي فيلتر شده باقي ميماند. چنانچه وجود اين آب براي عمليات بعدي نامطلوب باشد حذف آن به طريقهي خشک کردن الزامي است. معمولا سيال خشک کنندهي هوا ميباشد که تا درجهي حرارت معيني گرم شده است و هنگام عبور از لابه لاي ذرات خشک شونده حرارت خود را به آن منتقل کرده و بخار آب ايجاد شده را همراه خود به خارج منتقل ميسازد. اين روش تبادل انرژي و جرم، خشک کردن مستقيم ناميده ميشود. ممکن است عمل خشک کردن به صورت غيرمستقيم نيز انجام شود در اين حالت انرژي حرارتي در محيط بستهي ديگري توليد شده و اين انرژي از طريق ديوارهي اين محيط بسته جرم کنسانتره منتقل ميگردد.
در اين روش تبادل انرژي بين سيال خشک کننده و کنسانتره برقرار بوده ولي تبادل جرم بين آنها برقرار نمي باشد و بخار آب ناشي از تبادل انرژي به صورت مستقل از سيال خشک کننده خارج ميشود.
انواع مختلفي از خشک کن ها در صنعت به کار برده ميشوند که متداولترين آنها خشک کنهاي استوانهاي و معمولا گردان ميباشند. در روش حرکت عکس بار، عملا بار تا حذف کامل آب خشک مي شود در حالي که در حالت هم جهت، حذف کامل آب ميسر نبوده و بار خروجي 1 تا 2 درصد رطوبت دارد. بالعکس درجهي حرارت بار خروجي در روش هم جهت محدود بوده و براي باري که درجهي حرارت زياد باعث تغييرات فيزيکي و شيميايي آن مي شود مناسبتر است و سرانجام در روش حرکت غيرهم جهت، کنسانتره بايد دانه بندي رقيق تر داشته و اختلاف ابعاد ذرات نبايد از حدي تجاوز کند.
روش هاي استخراج معادن روباز:
استخراج روباز قديميترين روش استخراج و يا بهرهبرداري از معادن است. بيش از دو سوم مواد معدني جامد جهان به طريق روباز استخراج مي شوند. اصولاً به دلايل فني و اقتصادي سعي مي شود كه كانسارهاي سطحي و بسياري از كانسارهاي نزديك به سطح به طريق روباز استخراج شوند. زيرا مزاياي معادن روباز ، هزينه كم استخراجي ، نبود مسائل مربوط به نگاهداري فضاهاي زيرزميني، تهويه ، روشنايي، استخراج روباز را پر جاذبه مي كند.

اغلب معادن سنگ هاي ساختماني و فلزات با عيار كم و كليه معادن زغال و ليگنيت بعضي از معادن آهن به طريق روباز استخراج مي شوند. معادن آهن چغارت، سرب و روي انگوران و خاك نسوز آباده به اين روش استخراج مي شوند.
در معادن روباز امكان به كار انداختن ماشين آلات بزرگ و به طور كلي مكانيزه كردن عمليات استخراجي ميسرتر است. و بدين وسيله مي توان هزينه استخراجي را كاهش داد. ماشين هاي چالزني بزرگ، بيل هاي مكانيكي پرقدرت، نوارهاي باربري پر توان و بالاخره كاميون هاي پر ظرفيت جملگي كار بهره برداري از معادن روباز را اقتصادي تر مي كند.

ابعاد معادن روباز :
عامل اصلي تعيين ابعاد معدن روباز شكل كانسار است ولي غالبآً براي استخراج كامل ماده معدني خاكبرداري لازم مي شود. و بنابراين وسعت معدن عملاً بيش از از ابعاد كانسار مي شود. هرگاه ماده معدني وسيع باشد كارگاه معدني روباز قسمتي از سطح كانسار را تشكيل مي دهد.

روش استخراج :
متداولترين روش استخراج معادن روباز روش استخراج پله اي است. در اين روش كانسار را به صورت پله درآورده و آن گاه پله مورد استخراج قرار مي گيرد. ابعاد پله عبارتند از ارتفاع پله، عرض پله، شيب دامنه، طول پله است كه اينها به شرايط طبيعي كانسار و عوامل فني ربط دارد.

ارتفاع پله اغلب به قدرت و توان بيل هاي مكانيكي باركننده بستگي دارد. از نقطه نظر حفاري و آتشباري نيز ارتفاع پله تعيين كننده است. ارتفاع پله در صورتي كه ضخامت طبقه مورد استخراج يا خاكبرداري محدود باشد، طبيعتاً از طرف طبيعت كانسار تعيين شده است . در عمل ارتفاع پله بين 2 تا 25 متر كه در صورت مساعد بودن كانسار ارتفاع 10 تا 15 متري مناسب تجربه شده است .
در بعضي از معادن دو نوع پله وجود دارد كه يكي مربوط به ارتفاع خاكبرداري و ديگري وابسته به ارتفاع ماده معدني است. ارتفاع اين دو ممكن است يكسان باشد. ولي اغلب به علت تفاوت قشر باطله و ضخامت ماده معدني با هم تفاوت دارند. شيب پله و يا تعيين زاويه در پله ها بستگي به سختي سنگ و فن آتشباري دارد. در صورتي كه سنگ كوهبري سخت باشد زاويه شيب پله بزرگتر و حالي كه خاك يا نرم باشد شيب كمتر انتخاب مي شود.
مقدار شيب پله بين 25 تا 85 درجه انتخاب مي شود. زاويه شيب دامنه جبهه كار معادن روباز كه نسبت به سطح افق تعيين مي شود براي سنگ هاي مختلف متفاوت است .
جدول زير به طور خلاصه و ساده مقدار زاويه را براي سنگ هاي گوناگون نشان مي دهد.

II : سنگ با سختي كم مانند شيست و يا رس متراكم
III : سنگ با سختي متوسط سنگ هاي آهكي دولوميتي
IV : سنگ هاي خيلي سخت مانند سنگ هاي آهكي متراكم و ماسه سنگ و كوارتزيت
درباره شيب دامنه بايستي گفت كه قدرت جوش خوردگي و چسبندگي سنگ ها يا قطعات به يكديگر نيز در انتخاب شيب موثر است.
هر چند روش استخراج معادن روباز به پلکاني منحصر مي شود ولي شيوه هاي باز کردن آن ، طرز ايجاد پله ، تعداد پله و ابعاد آن متفاوت است .
اهم شرايط و عواملي که بايستي قبل از طرح باز کردن مورد مطالعه قرار گيرد به شرح زير مي باشد .

2- شيب کانسار
3- وضع چين خوردگي وگسل ها
4- خواص مکانيکي و فيزيکي کانسار و سنگ هاي جانبي و خاک ها
5- وجود و عدم آب
6- راه سازي ، و ارتباط معدن به شبکه راه ها
البته امکان بررسي کليه نکات هميشه ميسر نيست و فقط مواردي که اکتشاف به طور کامل باشد مي توان معدن را مطابق اصول و به طور کلاسيک باز کرد. در عمل معادن روباز نيز مانند بسياري از معادن زيرزميني در حين استخراج اکتشاف مي شوند . و اغلب پس از مدتي مجدداً طرح مورد تجديد نظر قرار گرفته و در صورت لزوم تغييراتي به آن داده مي شود.

باطله برداري :
استخراج و جابه جا کردن خاک ها و سنگ ها باطله را باطله برداري مي گويند . تقريباً در اغلب موارد کانسارهايي که به صورت روباز استخراج مي شوند همراه با مقدراي خاکبرداري اند . سن ها و خاک هاي باطله که به صورت کلي بر روي ماده معدني قرار دارند عبارتند از :

2-سنگهاي جانبي ماده معدني که در استخراج جابجا مي شوند.
روش هاي مکانيکي باطله برداري به طور کلي با روش هاي مکانيکي استخراج کانه تفاوت چنداني ندارد و به سختي سنگ بستگي دارد.
براي استخراج معادن آهن از جمله روش هاي كه استفاده مي شود روش كلاسيك روباز است . در اين روش با احداث چندين پله در باطله و ماده معدني،به ماده معدني دسترسي مي يابند و آنرا استخراج مي كنند. تصوير افقي پله ها معمولاً دايره يا بيضي است و پله هاي مختلف به وسيله جاده مورب به يكديگر ارتباط دارند. باطله و مواد معدني، معمولاً به داخل كاميون ها ويژه تخليه مي شود.

روش كلاسيك روباز در مورد كانسارهاي تك لايه اي، چند لايه اي ، و تودهاي تا حدودي متفاوت است كه به شرح آن مي پردازيم.
كانسارهاي تك لايه :
اين روش در مورد كانسارهاي تك لايه اي شكل شيبدار بكار مي رود. بسته به ضخامت لايه و باطله، يك با چند پله در مواد باطله و ماده معدني احداث مي شود به گونه اي كه پله هاي باطله به اندازه كافي جلوتر از پله هاي ماده معدني باشد. پس از آماده شدن معدن پشروي پله ها به موازات هم صورت مي گيرد. در شروع كار، از محدوده معيني از معدن - كه وسعت آن براي انجام عمليات بعدي كافي باشد- باطله برداري مي شود
باطله حاصل از اين محدوده، در نزديكترين محل گود ممكن ريخته شده و در صورت لزوم محل باسازي مي شود. پس از آماده شدن اين قسمت استخراج آن آغاز مي شود و پس از اينكه به اندازه كافي فضاي خالي به دست آمد، باطله برداري قسمت هاي ديگر شروع مي شود. و باطله آنها را در محل استخراج شده مي ريزند. در اين روش استخراج، استفاده از بيل مكانيكي بسيار متداول است و علاوه بر آن از اسكريپر نيز استفاده مي شود.
كانسارهاي چند لايه
در مواردي كه كانسار مركب از چند لايه شيبدار باشد، در مورد هر لايه، پله جداگانه اي احداث مي شود. پس از آنكه پله مربوط به پايين ترين لايه آماده شد عمليات استخراجي آغاز مي شود. بديهي است پله هاي باطله برداري زيادتر مي شود به هر حال عمليات استخراجي تا آنجا ادامه مي يابد كه با توجه به نسبت خاكبرداري، استخراج ماده معدني مقرون به صرفه باشد.

كانسارهاي توده اي :
روش كلاسيك روباز ، عمدتاً براي استخراج كانسارهاي تودهاي به ويژه آهن و مس به كار ميرود. در مواردي كه كانسار به صورت تودهاي با ابعاد كما بيش مساوي و ضخامت مواد پوشاننده آن كم باشد و يا در مورد كانسارهاي تودهاي با گسترش وسيع ولو اينكه در عمق قرار داشته باشد روش كلاسيك روباز بسيار مناسب است.

منبع:ايران سنگ آهن