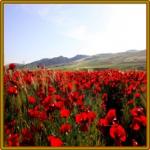
سلام به وب من خوش آمدید دوستان و همراهان عزیز از اینکه مهمان این وب هستید بسیار سپاسگزارم منتظر نظرات سازنده ی شما دوستان هستم
عنوان | پاسخ | بازدید | توسط |
![]() |
1 | 1215 | piskesvat |
![]() |
3 | 2709 | mehran99 |

مقدمه
الیاژهای Al-Si-Mg بویژه معروفترین الیاژ این گروه یعنیA356 کاربرد گسترده ای در صنایع خودروسازی و هوا فضا دارند. ازجمله دلایل این کاربردها را میتوان به مواردی چون نسبت استحکام به وزن بالا،مقاومت به خوردگی مناسب ،سیالیت و قابلیت ریختگی عالی ،مقاومت به ترک گرم،قابلیت جوشکاری مناسب و همچنین ضریب انبساط حرارتی پایین اشاره نمود الیاژ356 بطور معمول دارای 5/6-5/7 درصد وزنی سیلیسیم و 7/0-25/0 درصد وزنی منیزیم بوده و از طریق فرایندهای معمول ریخته گری تولید میشوند انجماد اهسته این الیاژ تولید ریز ساختار بسیار درشتی میکند که در نتیجه ان ساختار یوتکتیکی متشکل از تیغه های بزرگ سیلیسیم در یک زمینه پیوسته الومینیومی مشاهده میشود الیاژهای این نوع یوتکتیک به علت طبیعت صفحات سیلیسیم درشت دارای انعطاف پذیری وداکتیلیته پایین هستند.
الیاژهای Al-Si-Mg را بعنوان مواد کامپوزیتی مشتمل بر ذرات ناپیوسته و سخت سیلیسیم در زمینه الومینیم با قابلیت تغیرشکل بالا در نظر میگیرند خواص مکانیکی این الیاژها به شکل و اندازه دانه ،مشخصه های دندریتها، اندازه و شکل و نحوه توزیع ذرات فاز دوم (رسوبات) و مورفولوژی فاز سیلیسیم یوتکتیک از لحاظ شکل، توزیع واندازه وابسته است . با کروی شدن ذرات فاز سیلیسیم یوتکتیک خواص مکانیکی این الیاژها بویژه قابلیت تغیر شکل انها بطور قابل ملاحظهای بهبود میابد.
در شرایط معمول انجماد ، فاز سیتیسیم بصورت تیغه های خشن و سوزنی شکل میباشد این تیغه ها میتوانند به عنوان مراکز جوانه زنی و اشاعه ترک عمل نموده وباعث تضعیف خواص مکانیکی شوند . فاز سیلیسیم در الیاژهایAl-Si-Mg با مورفولوژی های مختلفی نظیر لایه ای، کروی و فیبری در ریز ساختار ظاهر میشوند. فرایند بهسازی سبب تغیر شکل و اندازه ذرات سیلیسیم شده و در نتیجه خواص مکانیکی را تغیر خواهد داد. تغیر مورفولوژی سیستم ازتیغه های سوزنی شکل به رشته ای باعث تقویت خواص مکانیکی و بویژه درصد ازدیاد طول کل از 7 درصد به 16 درصددر الیاژ A356 شده است خواص مکانیکی و رفتار شکست الیاژهای الومینیمA356 شدیدا وابسته به ریز ساختار انها بوده و توسط رسوباتMgSi و پراکندگی تیغه های سیلیسیم یوتکتیککنترل میشوند اصولا در الیاژهای Al-Si اندازه و توزیع تیغه های سیلیسیم در فاز یوتکتیک مربوطه بسیار حائز اهمیت است . در واقع تردی تیغه های Si مسئول اصلی خواص مکانیکی ضعیف در این دسته از الیاژها است از انجائیکه شکل پذیری و داکتیلیته الیاژهای Al-Si غالبا از ساختار ترد یوتکتیک انها متاثر میگردد بنابر این میتوان با کاهش مقدار فاز یوتکتیک یا تغیر مورفولوژی ان خواص فوق را بهبود بخشید.
معمولا برای دستیابی به خواص مکانیکی مطلوب در الیاژهای ریختگی Al-Si-Mg از اصلاح روشهای ریختگی برای حذف عیوب و تقویت فاز الومینیم با ایجاد ساختمان گلبولی و روشهای بهسازی سیلیسیم استفاده میشود.
بهسازی آلیاِِژهایAl- Si-Mg
بهسازی یکی از عملیاتی کیفی مذاب است که برای افزایش داکتیلیته و استحکام فلزات و الیاژها به کار میروددر این فرایند با افزایش عناصری نظیر سدیم واسترانسیم وانتیموان به الیاژ Al-Si-Mg سبب میشود تا سیلیسیم از حالت سوزنی و خشن به حالت خمیری ولایه ای تبدیل شود که درنتیجه بهبود خواص مکانیکی پدید میاید .
الیاژهای Al-Si-Mg مواد مهندسی خیلی خوبی مطرح شده اند که به علت قابلیت خیلی خوب ریختگی نسبت استحکام به وزن بالا و بهترین مقاو مت در برابر خوردگی استفاده وسیعی در صنعت اتومبیلسازی صنایع دفاعی وصنایع فضایی دارند بهسازی جزو عملیاتی است که برای بالا بردن خواص این الیاژ و مخصوصا برای افزایش درصد ازدیاد طول نسبی مناسب میباشد
بهسازی سیلیسیم یوتکتیک میتواند توسط سرعت سرد کردن وعناصر بهساز بدست اید ولی بدست اوردن بهسازی کامل با افزایش سرعت سرد کردن بسیار مشکل است به خوبی معلوم گردیده که عناصر گروه اول و دوم جدول تناوبی بهسازهای خوبی برای الیاژهایAl-Si-Mgهستند این عناصر به مذاب اضافه میشوند تا سیلیسیم را از حالت سوزنی یا ورقهای به حالت الیافی وولایه ای تبدیل کنداسترانسیم به صورتهای خالص نمک وامیژان و انتیموان بصورت خالص فلزی و امیژان بکار میرود.درالیاژهای بهسازی شده ریز تخلخل در سراسر قطعه ریختگی پراکنده شده که درنتیجه ان خواص مکانیکی کاهش می یابد.
بررسی ریز ساختار الیاژ Al-Si-Mg و ارتباط ان با خواص مکانیکی
مطالعات انجام شده نشان میدهد که خواص مکانیکی الیاژ Al-Si-Mg در شرایط ریختگی به ترتیب اهمیت متاثر از مشخصههای ریزساختاری همچون ظرافت ذرات سیلیسیم موجود در مناطقق یوتکتیکی فاصله بازوهای دندریت مقدار ناخالصیها ریزمکهاو حظور فازهای موجود در زمینه شامل اخالهافازهای بین فلزی و غیره میباشد عوامل یاد شده بطور مستقیمبر خواص مکانیکیالیاژ تاثیر میگذارند در عین حال عواملی هم باعث تغیر مولفه های بالا میشوند که عبارتند از:
سرعتهای متفاوت انجماد مذاب اصلاح ساختار و بهسازی الیاژ بهوسیله اضافه نمودن عناصربهساز انجام عملیات گاز زدایی وعملیات حرارتی که منجر به حصول شرایط پیر سختی یا یکنواختی ترکیبی ساختار میشود
بر اساس مطالعات و ازمایشات انجام شده برسی اثرات ناشی از سرعت سرد کردن مذاب بر ریز ساختار وخواص مکانیکی الیاژ مورد بحث نشان میدهد ارطباط مستقیمی بین پارامترهای سرعت سرد کردن مذاب الیاژو مشخصه هایریزساختاریو خواص مکانیکی میباشدبه طوری که تغیرات سرعت سرد کردن مذاب الیاژموردبحث میباشد به عبارت بهترافزایش سرعت سرد کردن منجر به کاهش فاصله بازوهای بین دندریتی و همچنین کاهش میزان ریز مک در ریزساختارالیاژ میگردد و همچنین شرایط افزایش خواص استحکامی نظیراستحکام تسلیم و استحکام نهایی و همینطورافزایش خاصیت فرم پذیری الیاژ همانند درصد ازدیاد طول نسبی را سبب میشود.
آخال زدایی الیاژهای Al- Si- Mg
الیاژهای Al بدلیل میل ترکیبی بالا با اکسیژن همواره حاوی میزان قابل ملاحظه ای از اخالهای اکسیدی به همراه سایر اخالها مانند اسپینل ها ترکیبات بین فلزی بوریدها نیترید ها و کاربید ها میباشد این اخالها علاوه بر کاهش خواص مکانیکی سیالیت و قابلیت ماشینکاری موجب جوانه زنی حبابهای گازی گردیده و درصد تخلخل را افزایش میدهند که در نوع خود عیب بسیار بزرگی محسوب میشود اخالها از طریق اتمسفر کوره پوسته اکسیدی سطح قطعات پاره شدن سطح لایه مذاب روان سازها ابزار ریخته گری وغیره وارد مذاب میگردند واز انجا که مماتعت از ورود انها به داخل مذاب تقریبا غیر ممکن میباشد بخش وسیعی از مطالعات بر نحوه جدا سازیاز مذاباستوار گردیده است فلاکس زدن و فیلتر کردن دو روش عمده و اساسی در فرایند آخال زدایی می باشد روش اول بر اساس کاهش وزن مخصوص و نیز کاهش تر شوندگی آخال منجر به حذف آن می شود. و فیلتر نیز همچون صافی با درصد تخلخل مشخص آخال ها را به خود جذب می نماید. فلاکس زنی در اکثر موارد به وسیله گاز کلر و نیتروژن و فیلتر کردن با استفاده از فیلتر سرامیکی برای این آلیاژ ها مورد استفاده قرار می گیرد.
اخال ها در این آلیاژها عمدتا اکسیدی کاربیدی نیتریدی تبریدی ایدی و ترکیبات بین فلزی می باشد. تا کنون 15 گونه آخال های مختف در آلیاژهای Al شناسایی شده اند که سبک ترینشان AlO و سنگین ترین آن AlO یا کوراندوم می باشد. و در بین آنها سایر گو نه های اکسیدی در سطح مذاب شناور می باشد. سیالیت آلیاژ مورد بحث ارتباط تنگا تنگ و مستقیمی با مقدار آخال های موجود در مذاب دارد. با انجام عملیات آخال زدایی می توان سیالیت و خواص مکانیکی آلیاژ را به طور گسترده ای افزایش داد.
ترکیب شیمیایی و کاربرد خواص
ترکیب منیزیم (2/1 تا 6/0) و سیلیسیم (4/0 تا 3/1 ٪) در آلومینیم اساس آلیاژهای کارشده با سختی پذیری آلومینیم ـ منیزیم ـ سیلیسیم سری 6XXX را تشکیل می دهد. در بیشتر موارد مقدار منیزیم و سیلیسیم اسما به اندازه ای است که بتواند فازهای نیمه پایدار بین فلزی MgSi را به وجود آورد ولی سیلیسیم می تواند بیشتر از مقدار لازم برای تشکیل MgSi به کار رود. منگنز و کرم اغلب به آلیاژهای 6xxx افزوده می شود تا استحکام را افزایش و اندازه دانه ها را کنترل کنند. مس نیز استحکام این آلیاژ را افزایش می دهد. اما مگر مقدار آن از 5/0٪ تجاوز کند مقاومت به خوردگی را کاهش می دهد.
اولین آلیاژ آلومینیمی که مقدار MgSi آن موازنه شده بود آلاژ 6053 بود که در سالهای 1930 توسعه پیدا کرد و دارای 2٪ MgSi 25/0٪ Cr است. پس از آن آلیاژ 6061 بود ک آلیژی با ترکیب 5/1 ٪ MgSi ،2/0 ٪ Cr ، Cu 27/0 ٪ است. آلیاژ 6061 آلیاژی سازه ای داری استحکام متوسط با کاربرد عمومی است. آین آلیاژ امروزه در طیف وسیعی به کار می رود و یکی از مهمترین آلیاژهای آلومینیم است. آلیاژهای پر استحکام Al-Mg-Si مانند 6066 و 6070 با مقدار سیلیسیم بیشتری در سالهای 1960 معرفی شدند.
برای اینکه عمل اکستروژن و ایجاد شکل های مختلف به ستدی انجام شود ، آلیاژ 6063 توسعه یافت. استحکام این آلیاژ اندکی کمتر است و MgSi٪ دارد. این آلیاژ را می توان به هنگام عملیات اکستروژن بلافاصله پس از خروج از دستگاه آب داد و در نتیجه از هزینه عملیات گرمایی حل سازی جلوگیری کر. انواع آلیاژهای 6063 مثل 6463 به دلیل مشخصه های نهایی بهتر توسعه یافت. در آلیاژ 6463 ، مقدار آهن را در حد کمی نگه می دارند در نتیجه جلای آلومینیم پس از اکسایش آندی افزایش می یابد.
خواص مکانیکی
آلیاژهای Al-Si-Mg کار شده استحکام متوسطی دارند ، زیرا فقط مقدار خیلی کمی ( بین 1 تا 2 درصد) MgSi برای رسوب سختی می تواند به صورت آلیاژ در آید. آلیاژ های مستحکمتر این خانواده 6066 و 6070 می باشند که مقدار سیلیسیم آنها بیش از مقدار لزوم برای ایجاد 1 تا 2 ٪ وزنی MgSi است.
در آلیاژ های Al-Si-Mg معمولا عملیات حل سازی در دمایی حدود 520 درجه انجام می شود. از آنجایی که این دما خیلی کمتر از دمای ذوب اوتکتیک این آلیاژها می باشد بنابر این اگر اندکی بیش از مقدار لازم نیزگرم شوند احتمال ذوب اینها کم است. عملیات حل سازی در آلیاژ 6061 را می توان در دماهایی بیش از 520 درجه نیز انجام دادکه با مقداری افزایش در استحکام همراه است زیرا در دمای 520 درجه تمام MgSi حل نمی شود.
بیشترین استحکام در آلیاژهای Al-Si-Mg وقتی به دست می آید که پیر شدن مصنوعی بلافاصله پس از آبدهی انجام شود. اگر این آلیاژ در دمای اتاق به مدت 1 تا 7 روز پیرشود بین 3 تا 4ksi از استحکام کم می شود. با وجود این وقتی که آلیاژ به مدت یک ماه یا بیشتر در دمای اتاق نگه داری شود استحکام مقداری افزایش می یابد ولی این افزایش در مقایسه با حالتی که قطعه بلافاصله بعد از آبدهی پیر شود بسیار کم است.
مقاومت به خوردگی
مقاومت به خوردگی این آلیاژ ها در تمام محیط های طبیعی و در اغلب شرایط مصنوعی عالی است. مقاومت به خوردگی این آلیاژ ها زمانی بهترین است که آلیاژ سریعا آبدهی و تا حالت مطلوب به طور مصنوعی پیر شود.
ساختار میکروسکوپی نمونه
الیاژریختگی المینیوم- سیلیسیم- منیزیم در دسته الیاژهای سه تایی قرار دارد این الیاژ در حالت ریختگی شامل یک فاز گسترده دندریتی المینیوم الفا و فاز دوم شامل ناحیه انجمادی یوتکتیک است ناحیه یوتکتیک شامل تیغه های سیلیسیم و رسوب های α-AlFeSi,MgSi در زمینه الومینیم می
باشد. شکل زیر ریز ساختار الیاژ AL-Mg-Si را نشان می دهد.مشاهده میشود در این حالت ساختار متشکل از الومینیم الفا(زمینه)و تیغه های بزرگ و سوزنی شکل سیلیسیم که بدون جهت گیری خاص در زمینه الومینیمی توزیع شده است
آزمایش سختی
ازمایش سختی به وسیله دستگاه برینل انجام گرفت که در ان از ساچمه های به قطر 2.5 و بار62.5 که به مدت ده ثانیه به قطعه اعمال شد استفاده گردید که نمونه ریخته شده در قالب ماسه ای خشک دارای سختی 60 برینل و نمونه ریخته شده در قالب ماسه ای تر دارای سختی47برینل بود در قالب ماسه ای خشک به دلیل افزایش قابلیت هدایت حرارتی قالب و در نتیجه افزایش تعداد دانه در واحد سطح سختی افزایش میابد.
آزمایش سیالیت
الیاژهای سه تایی AL-Mg-Si بدلیل حضور سیلیسیم از سیالیت نسبتا خوبی بر خوردار هستند برای امتحان سیالیت نمونه ریخته شده ازنمونه اسپیرال استفاده شد که تقریبا تمام طول نمونه اسپیرال به وسیله مذاب پر شده بود.