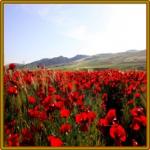
سلام به وب من خوش آمدید دوستان و همراهان عزیز از اینکه مهمان این وب هستید بسیار سپاسگزارم منتظر نظرات سازنده ی شما دوستان هستم
عنوان | پاسخ | بازدید | توسط |
![]() |
1 | 1215 | piskesvat |
![]() |
3 | 2709 | mehran99 |
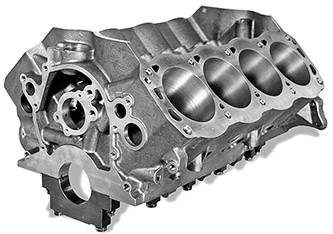
انواع فولاد و چدن
تهیه فولاد
محصول کوره ذوب آهن ، چدن است که معمولاً دارای ناخالصی کربن و مقادیر جزئی ناخالصیهای دیگر است که به نوع سنگ معدن و ناخالصیهای همراه آن و همچنین به چگونگی کار کوره بلند ذوب آهن بستگی دارد. از آنجایی که مصرف عمده آهن در صنعت بصورت فولاد است، از این رو ، باید به روش مناسب چدن را به فولاد تبدیل کرد که در این عمل ناخالصیهای کربن و دیگر ناخالصیها به مقدار ممکن کاهش یابند.
روش های تهیه فولاد
از سه روش برای تهیه فولاد استفاده میشود:
– روش بسمه: در این روش ، ناخالصیهای موجود در چدن مذاب را به کمک سوزاندن در اکسیژن کاهش داده، آن را به فولاد تبدیل میکنند. پوشش جدار داخلی کوره بسمه از سیلیس یا اکسید منیزیم و گنجایش آن در حدود ۱۵ تن است. نحوه کار کوره به این ترتیب است که جریانی از هوا را به داخل چدن مذاب هدایت میکنند تا ناخالصیهای کربن و گوگرد بهصورت گازهای SO2 و CO2 از محیط خارج شود و ناخالصیهای فسفر و سیلیس موجود در چدن مذاب در واکنش با اکسیژن موجود در هوا به صورت اکسیدهای غیر فرار P4O10 و SiO2 جذب جدارهای داخلی کوره شوند و به ترکیبات زودگداز Mg3(PO4)2 و MgSiO3 تبدیل و سپس به صورت سرباره خارج شوند. سرعت عمل این روش زیاد است، به همین دلیل کنترل مقدار اکسیژن مورد نیاز برای حذف دلخواه ناخالصیهای چدن غیرممکن است و در نتیجه فولاد با کیفیت مطلوب و دلخواه را نمیتوان به این روش بدست آورد.
– روش کوره باز (یا روش مارتن): در این روش برای جدا کردن ناخالصیهای موجود در چدن ، از اکسیژن موجود در زنگ آهن یا اکسید آهن به جای اکسیژن موجود در هوا در روش بسمه (به منظور سوزاندن ناخالصیهایی مانند کربن ، گوگرد و غیره) استفاده میشود. برای این منظور از کوره باز استفاده میشود که پوشش جدار داخلی آن از MgO و CaO تشکیل شده است و گنجایش آن نیز بین ۵۰ تا ۱۵۰ تن چدن مذاب است. حرارت لازم برای گرم کردن کوره از گازهای خروجی کوره و یا مواد نفتی تأمین میشود. برای تکمیل عمل اکسیداسیون ، هوای گرم نیز به چدن مذاب دمیده میشود. زمان عملکرد این کوره طولانیتر از روش بسمه است. از این نظر میتوان با دقت بیشتری عمل حذف ناخالصیها را کنترل کرد و در نتیجه محصول مرغوبتری بدست آورد.
– روش الکتریکی: از این روش در تهیه فولادهای ویژهای که برای مصارف علمی و صنعتی بسیار دقیق لازم است، استفاده میشود که در کوره الکتریکی با الکترودهای گرافیت صورت میگیرد. از ویژگیهای این روش این است که احتیاج به ماده سوختنی و اکسیژن ندارد و دما را میتوان نسبت به دو روش قبلی، بالاتر برد. این روش برای تصفیه مجدد فولادی که از روش بسمه و یا روش کوره باز بدست آمده است، به منظور تبدیل آن به محصول مرغوب تر ، بکار میرود. برای این کار مقدار محاسبه شده ای از زنگ آهن به فولاد بدست آمده از روش های دیگر را به کوره الکتریکی اضافه کرده و حرارت میدهند. در این روش ، برای جذب و حذف گوگرد موجود در فولاد مقدار محاسبه شدهای اکسید کلسیم و برای جذب اکسیژن محلول در فولاد مقدار محاسبه شده ای آلیاژ فروسیلیسیم (آلیاژ آهن و سیلیسیم) اضافه میکنند.
انواع فولاد و کاربرد آنها از نظر میزان کربن به سه دسته تقسیم میشوند:
– فولاد نرم: با کمتر از ۰/۲ درصد کربن که بیشتر در مواردی مانند تهیه پیچ و مهره ، سیم خاردار و چرخ دنده ساعت و … بکار میرود.
– فولاد متوسط: با مقدار کربن بین ۰/۲ تا ۰/۶ درصد که عمدتاً در ساخت ریل و راه آهن و مصالح ساختمانی مانند تیرآهن مصرف میشود.
– فولاد سخت: با میزان کربن بین ۰/۶ تا ۱/۶ درصد که قابل آب دادن بوده و معمولاً در ساخت فنرهای فولادی، تیر، وسایل جراحی، مته و … بکار میرود.
عملیات حرارتی فولادها
عملیات حرارتی فولادها می تواند شامل موارد زیر باشد:
– کربندهی سطحی
– بازپخت کامل (آنیل)
– آنیل جهت کروی کردن سمنتیت (اسفرودایز)
– نرماله کردن (نرمالیزاسیون)
– کوئنچکردن
– برگشت دادن (تمپر کردن)
فازهای مختلف قابل تشکیل در فولاد
نمودار فازی آهن-کربن
نمودار تعادلی آهن-کربن (Fe-C) راهنمایی است که به کمک آن میتوان روشهای مختلف عملیات حرارتی، فرآیندهای انجماد، ساختار فولادها و چدنها و انواع فازهای قابل تشکیل در آنها را بررسی کرد.
قسمتی از این نمودار که در فولادها کاربرد دارد، قسمت آهن-کاربیدآهن (سمنتیت) است.
چون کاربید آهن یک ترکیب شبهپایدار است، بنابراین دیاگرام آهن- سمنتیت را سیستم آهن-کربن شبهپایدار مینامند. حالت پایدار کربن در فشار اتمسفر، کربن آزاد (گرافیت) است.
قسمتهایی که در نمودار با حروف یونانی مشخص شدهاند، نشانگر محلولهای جامد از نوع بیننشینی هستند.
تحولات همدما (ایزوترم) در سیستم آهن-کربن شبه پایدار
خطوط افقی در نمودار، نشان دهنده استحالههای همدما است که عبارتند از:
• استحاله یوتکتیک : دما ۱۱۴۸درجه سانتیگراد، غلظت کربن ۴/۲درصد
• استحاله یوتکتوئید : دما ۷۲۸درجه سانتیگراد، غلظت کربن ۰/۸ درصد
• استحاله پریتکتیک : دما ۱۴۹۵درجه سانتیگراد، غلظت کربن ۰/۱۸ درصد
البته باید توجه داشت که غلظتها و دماهای ذکرشده برای آهن-کربن خالص بوده و با حضور عناصر آلیاژی دیگر، این پارامترها تغییر میکنند.
آلوتروپهای آهن
- آهن آلفا
- آهن گاما
- آهن دلتا
آهن آلفا (α)
آهن آلفا یکی از آلوتروپهای آهن است. این آلوتروپ از دمای ۲۷۳- تا ۹۱۰ درجه سانتیگراد پایدار است. این آلوتروپ دارای ساختمان بلوری مکعبی مرکزپر (bcc) است.
ثابت شبکه آهن آلفای فرومغناطیس، ۲/۸۶ آنگستروم است.
آهن گاما (γ)
آهن گاما یکی دیگر از آلوتروپهای آهن است که در محدوده دمایی ۹۱۲ تا ۱۳۹۴ درجه سانتیگراد پایدار بوده و ساختمان بلوری Fcc (مکعبی وجوه مرکزپر) دارد.
آهن دلتا (δ)
آهن دلتا دیگر آلوتروپ آهن است که از دمای ۱۴۰۱ تا ۱۵۳۹ درجه سانتیگراد (نقطه ذوب آهن) پایدار است.
آهن دلتا دارای ساختمان بلوری مکعبی مرکزپر (bcc) بوده و دارای خاصیت پارامغناطیس می باشد. ثابت شبکهی آن نیز بزرگتر از آهن آلفا است. ثابت شبکه آهن دلتا، ۲/۹۳ آنگستروم است.
فازها و ساختارهای مخلتف در نمودار فازی آهن- کربن
- فریت
• آستنیت
• سمنتیت
• لدبوریت
• پرلیت
• بینیت
• مارتنزیت
فریت
به محلول جامد بیننشینی کربن در آهن آلفا α-Fe (آهن مکعبی مرکزپر) فِریت گفته میشود. حداکثر غلظت کربن در فریت حدود ۰/۰۲ درصد وزنی و در دمای ۷۲۷ درجه سانتیگراد است. مقاومت کششی فریت در حدود psi ۴۰۰۰۰ است.
آستنیت
آستنیت (به انگلیسی: Austenite) محلول جامد بیننشینی کربن در آهن گاما (آهن مکعبی وجوه مرکزپر) است. نام این فاز از ویلیام چاندلر روبرتز- اوستن، متالورژیست انگلیسی، گرفته شدهاست. حداکثر حلالیت کربن در آهن گاما، ۲ درصد در دمای ۱۱۴۷ درجه سانتیگراد است. آستنیت در دمای محیط پایدار نیست.
سمنتیت
سِمِنتیت یا کاربید آهن یک ماده مرکب شیمیایی با فرمول Fe3C و دارای ۶/۷۶ درصد کربن با ساختار بلوری ارتورومبیک است. سمنتیت فازی بسیار سخت و شکننده است.
لدبوریت
لدبوریت (به آلمانی: Ledeburit) به مخلوط یوتکتیکی آستنیت و سمنتیت گفته میشود که از مذابی با ۳/۴ درصد کربن در دمای ۱۱۴۷ درجه سانتیگراد تحت یک واکنش یوتکتیکی حاصل میشود. از آنجایی که آستنیت در دمای محیط پایدار نبوده و بر اساس یک واکنش یوتکتوئیدی به پرلیت تبدیل میشود، بنابراین ساختمان لدبوریت در دمای محیط بصورت پرلیت و سمنتیت خواهد بود. نام این ساختار از کارل هاینریش آدولف لدبور متالورژیست آلمانی گرفته شدهاست.
پرلیت
پرلیت به مخلوط یوتکتوئیدی فریت و سمنتیت گفته میشود. پرلیت تحت یک تحول یوتکتوئیدی از آهن گاما با ۰/۸ درصد کربن در ۷۲۳ درجه سانتیگراد حاصل میشود. مقاومت کششی پرلیت سه برابر فریت یعنی حدود psi۱۲۰۰۰۰ است.
بینیت
بینیت (به انگلیسی: Bainite) محصولی ریزساختاری ناشی از تجزیهی یوتکتوئیدی است. این ساختار هنگامی ایجاد میشود که یک فاز دما – بالا هنگام سرمایش، به دو فاز متفاوت تجزیه میگردد. تفاوت این ساختار با پرلیت در مورفولوژی آن است. بینیت زمانی به وجود میآید که سرعت رشد دو فاز متفاوت باشد. با اینکه ساختار بینیت در بسیاری از آلیاژهای غیرفلزی نیزیدهشدهاست، اما تحقیقات در این زمینه عمدتاً بر روی آلیاژهای فولادی متمرکز بوده است.
مارتنزیت
مارتنزیت (به آلمانی: Martensite) بطور کلی به ساختارهای بلورینی گفته میشود که توسط استحاله مارتنزیتی به وجود بیایند. اما این اصطلاح بیشتر به فاز مارتنزیت در فولادهای سختشده اطلاق میگردد. اگر آستنیت به قدری سریع سرد شود که هیچ یک از استحالههای بر پایه نفوذ در آن اتفاق نیافتد و فوق سرمایش تا حدی ادامه یابد که ساختار Fcc پایدار نباشد، این ساختار بصورت برشی به bcc تبدیل میشود که از کربن فوق اشباع شده است. فاز حاصل را مارتنزیت مینامند. مارتنزیت از نام متالورژیست آلمانی آدولف مارتنز گرفته شده است.
انواع فولاد
بر مبنای یک تعریف قدیمی، فولاد ها آلیاژهایی از آهن و کربن هستند که در اکثر حالات دارای انعطاف پذیری و شکل پذیری مناسبی می باشند. مقدار کربن در فولاد تا حدود ۱/۷ درصد متغیر بوده و از طرف دیگر عناصری نظیر منگنز و سیلیسیم در مقادیر کمتر از ۱ درصد و گوگرد و فسفر در مقادیر جزیی به عنوان ناخالصی در فولاد موجودند.
امروزه تعریف فوق نمی تواند تمام فولاد ها را شامل شود زیرا فولاد هایی وجود دارند که مقدار عناصر آلیاژی در آنها گاه از مرز ۵۰ درصد نیز تجاوز می کند.
ترکیبی از استحکام بالا و قابلیت چکش خواری، فولاد ها را از دیگر آلیاژها و مواد فلزی متمایز می سازد. فولاد ها در مقابل اعمال تنش های متغیر و نیروهای ضربه ای بسیار مقاوم بوده و از طرف دیگر امکان استفاده از آنها در درجات حرارتی زیر صفر (۱۰۰- درجه سانتیگراد) و بالا(تا ۸۰۰ درجه سانتیگراد و گاه بالاتر از آن) وجود دارد. استفاده از عناصر آلیاژی نظیر نیکل، کبالت، مولیبدن و تنگستن، این خانواده از آلیاژهای صنعتی را برای مصرف در درجات حرارتی بالا مناسب نموده است.
چون تعداد و تنوع فولاد ها بسیار زیاد است و خواص آنها اعم از : مکانیکی، فیزیکی، شیمیایی و متالورژیکی نیز بسیار متنوع می باشد و به علاوه با فرایندهای مختلفی نظیر : ریخته گری، مکانیکی (شامل نورد، کشش، فشار و …) عملیات حرارتی (باز پخت، آب دادن، برگشت دادن و … )، عملیات شیمیایی (مانند سمانتاسیون، نیتروراسیون و … )، تغییر حالت می دهند، لذا مطالعه کامل فولاد ها بسیار مفصل و طولانی است؛ به همین علت در این قسمت فقط به مطالعه فولاد های ریختگی که در متالورژی صنعتی از اهمیت ویژه ای برخوردارند پرداخته می شود.
لازم به توضیح است که امروزه ریخته گری فولاد اهمیت زیادتری پیدا کرده و بسیاری از قطعات فولادی که قبلاً با آهنگری و پرس تهیه می گردید، اکنون به روش ریخته گری تولید می شود. فولاد ها ممکن است بر حسب: ترکیب شیمیایی (ساده کربنی، کم آلیاژ و پر آلیاژ)، جنس و یا دقت در کنترل جنس (متوسط، خوب و عالی)، روش تهیه (زیمنس مارتن، بسمر، توماس، ال دی و الکتریکی) یا از نقطه نظر کاربرد تقسیم بندی شوند. از لحاظ کاربرد و مصرف، فولاد ها را می توان به صورت زیر تقسیم بندی کرد:
ریختگی، ساختمانی، جوش پذیر، خوش تراش، ابزار، ماشین سازی، لوله های بدون درز، نیتروراسیون، ساچمه، فنر، زنگ نزن، نسوز، مغناطیسی (سخت و نرم)، غیر مغناطیسی، آلیاژی مقاومت دار (الکتریکی)، مقاوم به سایش، کاربردهای خاص (زنجیر، مفتول، کابل و … )، مقاوم به سرما و غیره.
فولادهای ریختگی به دو دسته اصلی شمش های ریختگی و اشکال ریختگی فولادی تقسیم می شوند. شمش های فولادی مورد استفاده مستقیم نداشته بلکه پس از انجام عملیات بعدی نظیر کار مکانیکی (نورد، کوبش و … ) به محصولات تمام شده ای نظیر ورق، نبشی، سپری، تیرآهن و قطعات مهندسی نظیر میل لنگ، شاتون، اتصالات و شیرها، گلوله های آسیاب و … تبدیل می گردند. فولاد هایی که صرف تولید شمش می شوند نیاز به قابلیت شکل پذیری مکانیکی دارند؛ به همین دلیل، فولاد های کارپذیر نامیده می شوند. اشکال ریختگی فولادی که عموماً واژه قطعات ریختگی فولادی در مورد آنها به کار می رود، قطعات ریختگی در شکل های مختلف از ساده تا پیچیده اند که روی آنها (بعد از ریخته گری) عملیات مکانیکی خاصی انجام نمی گیرد. البته روش جدید تولید قطعات ریختگی (از جمله قطعات فولادی) از طریق فرآیند همزمان ریختگی و کار مکانیکی در محفظه قالب به نام ریخته گری کوبشی از این قاعذه مستثنی می باشد. تولید فولاد های کار پذیر که بعداً تحت عملیات مکانیکی قرار می گیرند به مراتب بیشتر از قطعات ریختگی است.
قطعات فولادی بسیار متنوع بوده و در وزن های ۱۵۰ گرمی تا ۲۰ تنی موجودند. استحکام کششی آنها نیز از ۴۰۰ تا ۲۰۰۰ نیوتن بر میلیمتر مربع تغییر کرده و از انعطاف پذیری کافی نیز برخوردارند. امروزه فولادهای جدید بالاترین استحکام ممکن را در میان خانواده فلزات و آلیاژها به خود اختصاص داده اند. از این میان می توان فولادهای ماریجینگ (Maraging) که محتوی نیکل، کبالت، مولیبدن، تیتانیم و آلومینیوم هستند را نام برد که دارای استحکام کششی حدود ۲۱۰۰ نیوتن بر میلیمتر مربع می باشند. انواع جدیدتر فولاد های با استحکام بالا فولاد های TRIP و فولاد های آسفورمد (Ausformed) هستند که دارای استحکام شگفت آور ۳۵۰۰ نیوتن بر میلیمتر مربع یعنی حدود ۷ برابر استحکام فولاد های معمولی می باشند. لذا هنگامی که تولید قطعات با استحکام های بسیار بالا مورد نظر باشد انتخاب فولاد تنها پاسخ مناسب به نیاز های صنایع خواهد بود.
قطعات ریختگی فولادی دارای موارد مصرف زیادی در صنایع ماشین سازی، خودروسازی، کشاورزی، راه آهن و راه سازی، صنایع نفت، پتروشیمی و شیمیایی، صنایع متالوژی نظیر واحد های آهن و فولاد، نورد، صنایع معدنی و سیمان و صنایع دفاعی می باشد. نمونه هایی از این قطعات شامل: پوسته توربین ها، انواع چرخ دنده های کوچک و بزرگ، چرخ قطار، اکسل خودروهای سنگین، ناخنک های ماشین های خاک بردار، فک سنگ شکن ها، زره آسیاب ها، مواد معدنی، مته های حفاری، غلطک های نورد، میل لنگ موتورهای دیزلی و … می باشد.
به علل قابلیت اطمینان و دوام بیشتر در شرایط کار حساس و امکان نازک کردن جداره قطعات ریختگی فولادی به علت بالا بودن استحکام آنها مصرف قطعات فولادی رو به افزایش است.
یک مزیت شاخص در فولادها به ویژه در مقایسه با چدن ها سهولت جوشکاری آنها است. در حقیقت فولاد ها را می توان بدون آن که مشخصات آنها تنزل یابد جوشکاری کرد. این خصوصیت، ساخت آن دسته از قطعات صنعتی که قسمتی از آن ریختگی و قسمتی کار شده است را از طریق اتصال با روش جوشکاری میسر ساخته است. تجربه نشان داده است که بسیاری از قطعات ریختگی فولادی در صورتی که عاری از حفره های انقباضی، گازی و ترک های حرارتی باشند دارای خواص مکانیکی مشابه فولاد های کوبشی (آهنگری یا فورج شده) هستند، ضمن آن که قیمت پایین تری نیز دارند. این واقعیتی است که تولید قطعات فولادی عاری از معایب سطحی داخلی نیاز به کنترل شدید در طی فرآیند تولید، طراحی قطعه و انتخاب آلیاژ مناسب دارد.
قطعات ریختگی فولادی را می توان از طریق ترکیب شیمیایی، ساختار قطعات، روش تولید و موارد مصرف آنها تقسیم بندی نمود. در زیر انواع روش های تقسیم بندی فولاد های ریختگی تشریح شده است.
فولاد ها به دو دسته فولاد های کربنی و آلیاژی تقسیم می شوند. فولاد های کربنی نیز خود به سه دسته فولاد های کم کربن تا ۰/۲ درصد کربن)، فولاد های کربن متوسط (۰/۲ تا ۰/۵ درصد کربن) و فولاد های پر کربن (بالای ۰/۵ درصد کربن) تقسیم می گردند. فولاد های آلیاژی نیز به سه گروه کم آلیاژی (تا حدود ۲/۵ درصد عناصر آلیاژی)، میان آلیاژی (۲/۵ تا ۱۰ درصد عناصر آلیاژی) و پر آلیاژی (بالای ۱۰ درصد عناصر آلیاژی) تفکیک می شوند. در بیشتر موارد، فولاد های آلیاژی را به دو دسته کم آلیاژی (تا ۰/۵ درصد عناصر آلیاژی) و آلیاژی (بالای ۰/۵ درصد عناصر آلیاژی)تقسیم بندی می نمایند.
فولاد های ریختگی بر حسب نوع ساختار میکروسکوپی آنها به صورت زیر دسته بندی می شوند:
نوع هیپویوتکتوئید (فرو یوتکتوئید): که دارای فریت آزادند (نه فریتی که به همراه سمنتیت تشکیل پرلیت می دهد). چنین ساختاری ویژه فولاد های کربنی و کم آلیاژی است. ذکر این نکته ضروری است که مفهوم فوق آن نیست که در ساختار میکروسکوپی این نوع فولاد فقط فریت آزاد وجود دارد بلکه وجود فریت آزاد قطعی بوده و در کنار آن فاز های دیگری نظیر برلیت و غیره نیز وجود دارد.
نوع هایپریوتکتوئید (فرایوتکتوئید): در ساختار این نوع فولاد، کاربید آزاد (نظیر Fe3C) که اصطلاحاً کاربید ثانویه نامیده می شود وجود دارد. نظیر فولاد های پر کربن (۰/۸۳ تا ۱/۷ درصد کربن)، فولاد های میان آلیاژی و فولادهای پر آلیاژی.
فولاد هایی که دارای ساختار کاملاً فریتی و یا نیمه فریتی هستند محتوی مقادیر بالایی کروم، تنگستن، مولیبدن، وانادیوم و سیلیسیم اند. فولاد ها با ساختار آستنیتی و نیمه آستنیتی دارای مقادیر زیادی منگنز، نیکل، کبالت و مولیبدن می باشند. اکثر قطعات فولادی تحت عملیات حرارتی قرار می گیرند. ساختار میکروسکوپی به دست آمده از این عملیات مبنای تقسیم بندی قطعات قرار می گیرند. قطعات فولادی عملیات حرارتی شده به صورت زیر طبقه بندی می شوند.
نوع پرلیتی که ویژه فولاد های کربنی، کم آلیاژی و میان آلیاژی است و دارای مخلوطی از فریت و پرلیت است. نوع مارتنزیتی که از طریق سرد کردن قطعات در آب یا روغن به دست آمده و شامل فولاد های پر کربن و فولاد های کم آلیاژی است. فولاد های هادفیلد (محتوی منگنز بالا)، فولاد های پر آلیاژی مقاوم در مقابل حرارت و دارای ساختار میکروسکوپی آستنیتی می باشند.
فولاد ها بر اساس روش تولید به انواع فولاد زیمنس مارتین (اسیدی و بازی)، فولاد های کنورتور و فولاد های کوره برقی (اسیدی و بازی) تقسیم بندی می گردند.
مذاب کوره های زیمنس مارتین به علت خواص خوب، قیمت پایین و ظرفیت زیاد کوره صرف تولید قطعات بزرگ و سنگین ریختگی می شود. فولاد های کوره برقی عموماً از طریق ذوب در کوره های برقی قوسی تهیه شده و فولاد های پر آلیاژی در کوره های القایی تهیه می شوند.
بسته به نوع مصرف (نظیر اجزاء هیدرولیک، توربین ها، ماشین های الکتریکی، قطار ها، قالب و …) قطعات ریختگی را می توان به فولاد های ابزار (فولاد های پر کربن و فولاد های پر آلیاژی) و فولاد های مخصوص نظیر فولاد های مقاوم در مقابل خوردگی، سایش، حرارت و اکسایش، اسید ها و انواع دیگری که در خانواده فولاد های پر آلیاژی قرار می گیرند تقسیم بندی نمود.
فولاد های کربنی
فولاد های کربنی بیشترین حجم تولید قطعات ریختگی فولادی را به خود اختصاص می دهند. این نوع فولاد ها متشکل از: کربن، منگنز، سیلیسیم، فسفر و گوگرد می باشند. کربن بیشترین تأثیر را در خواص مکانیکی قطعات تولیدی بر عهده داشته و فسفر و گوگرد عناصر نامطلوب می باشند، به استثنای فولاد های خوش تراش که به منظور سهولت تراش فولاد، درصد گوگرد را در آنها حدود ۱ درصد در نظر می گیرند. گوگرد از سیالیت مذاب فولاد کاسته و تمایل به ایجاد ترک های حرارتی گرم را (که در جریان انجماد قطعه پیش می آید) افزایش می دهد. فسفر نیز موجب تنزل مقاومت قطعات ریختگی در مقابل ضربه شده و با افزایش مقدار آن در فولاد مقاومت قطعات در برابر ضربه شدیدا(به خصوص در درجات حرارتی پایین)کاهش می یابد. به دلایل فوق مجموع فسفر و گوگرد در فولاد نبایستی از مرز ۰/۱ درصد تجاوز نماید.
با افزایش مقدار کربن در فولاد، استحکام نهایی، سختی و تنش تسلیم قطعات افزایش یافته و در مقابل از درصد ازدیاد طول نسبی، درصد کاهش سطح مقطع و مقاومت در مقابل ضربه آنها کاسته می شود. منگنز در فولاد اکسیژن زدا بوده و نقش مهم دیگر آن خنثی نمودن تأثیر مضر گوگرد (جلوگیری از پیدایش FeS) با ایجاد MnS است. مقدار منگنز در این نوع فولاد ها معمولاً بین ۰/۳ تا ۰/۸ درصد است. سیلیسیم نیز نظیر منگنز عنصری اکسیژن زدا بوده و به منظور کنترل گاز های محتوی مذاب مورد استفاده قرار می گیرد.مقدار سیلیسیم در این نوع فولاد ها بین ۰/۲ تا ۰/۵ درصد است.
منگنز و سیلیسیم در فولاد به صورت محلول بوده لذا در زیر میکروسکوپ قابل رﺅیت نیستند. هر دوی این عناصر قابلیت سختی پذیری قطعات ریختگی را نیز (در جریان عملیات حرارتی و سرد کردن) افزایش می دهند. سولفور منگنز به صورت فازی خاکستری رنگ در ساختار میکروسکوپی قطعات فولادی دیده می شود. فسفر برخلاف حالت چدن ها که به صورت فاز استدیت در ساختار میکروسکوپی قطعات قابل رویت است در قطعات فولادی به علت محلول بودن آن در فولاد قابل مشاهده نیست.
بسته به شرایط مصرف و ویژگی های فولاد های کربنی قطعات ریختگی را می توان در سه گروه زیر تقسیم بندی نمود:
گروه اول فولاد های ریختگی برای مقاصد عمومی نظیر پایه ها و اجزای غیر حساس ماشین آلات.
گروه دوم برای مقاصد اختصاصی و تولید قطعات صنعتی و مهندسی نظیر شیر ها و اتصالات، چرخ دنده ها و …
گروه سوم قطعات مورد استفاده برای کاربردهای ویژه هستند. کار این گونه قطعات تحت شرایط حساس بوده و رعایت اصول ایمنی و اطمینان از سلامت کار آنها ضروری است. نظیر چرخ قطار، اکسل ها، سیستم های تعلیقی نظیر سگ دست خودرو ها و …
تفاوت گروههای فوق در میزان فسفر و گوگرد محتوی فولاد است. حداکثر مقدار مجاز گوگرد و فسفر در گروههای سه گانه فوق به قرار زیر است:
گروه اول : ۰/۰۵- ۰/۰۷ درصد گوگرد و ۰/۰۵ تا ۰/۰۸ درصد فسفر.
گروه دوم: ۰/۰۴۵ – ۰/۰۶ درصد گوگرد و ۰/۰۴ تا ۰/۰۷ درصد فسفر.
گروه سوم : ۰/۰۴۵ – ۰/۰۵ درصد گوگرد و ۰/۰۴ تا ۰/۰۵ درصد فسفر.
مقدار کربن، منگنز و سیلیسیم فولاد ها در سه گروه فوق یکسان بوده و خواص مکانیکی قطعات تولیدی نیز مشابه خواهد بود. ترکیب شیمیایی فولاد های ساده کربنی در محدوده زیر قرار می گیرند.
منگنز ۰/۵ – ۱، سیلیسیم ۰/۲ – ۰/۸، فسفر حداکثر ۰/۰۵ و گوگرد حداکثر ۰/۰۶ درصد
فولاد های کم کربن
این فولاد ها معمولاً محتوی ۰/۱۲ تا ۰/۲ درصد کربن، ۰/۳۵ تا ۰/۶۵ درصد منگنز، ۰/۱۵ تا ۰/۲۵ درصد سیلیسیم، حدود ۰/۰۶ درصد فسفر و نزدیک ۰/۰۵ درصد گوگرد هستند. این نوع فولاد ها دارای سیالیت کم و تمایل به ایجاد ترک های گرم در قطعات ریختگی می باشند. استحکام کششی این نوع فولاد ها در حالت نرماله شده حدود ۴۰ تا ۴۲ کیلوگرم بر میلیمتر مربع (۳۹۴ تا ۴۱۰ نیوتن بر میلیمتر مربع) و ازدیاد طول نسبی حدود ۲۵ درصد است. مصرف اصلی این نوع فولاد ها در صنایع الکتریکی و صنایع ماشین سازی نظیر ریل راه آهن، بدنه پاتیل ها و قاب بدنه موتور ها می باشد. این نوع فولاد ها به دلیل نرمی، بدون عملیات حرارتی مورد مصرف قرار می گیرند. سطح این نوع فولاد ها را می توان از طریق کربوره کردن سخت نمود.
فولاد های کربن متوسط
محتوی ۰/۲ تا ۰/۵ درصد کربن، ۰/۳۵ تا ۰/۸ درصد منگنز، ۰/۲ تا ۰/۴۵ درصد سیلیسیم، ۰/۰۳ تا ۰/۰۵ درصد فسفر و ۰/۰۳ تا ۰/۰۵ درصد گوگرد می باشند. این نوع فولاد ها دارای مشخصه ریخته گری بهتری از فولاد های کم کربن بوده، سیال تر و تمایل کمتری به ایجاد ترک های گرم در قطعات ریختگی دارند. دارای استحکام کششی بین ۴۲ تا ۵۵ کیلوگرم بر میلیمتر مربع (۴۱۰ تا ۵۴۰ نیوتن بر میلیمتر مربع) و ازدیاد طول نسبی ۱۲ تا ۲۳ درصد می باشند. مصرف اصلی این نوع فولاد ها در صنعت ماشین سازی و در تولید قطعات ریختگی کوچک، متوسط و بزرگ، صنایع حمل و نقل، دستگاههای نورد و ماشین های راه سازی و ساختمانی است. در میان انواع فولاد های ساده کربنی این نوع فولاد ها بیشترین مقدار مصرف را دارا می باشند.
فولاد های پر کربن
این نوع فولاد ها محتوی ۰/۵ تا ۱/۶ درصد کربن، ۰/۵ تا ۰/۸ درصد منگنز، ۰/۰۴ تا ۰/۰۵ درصد فسفر و ۰/۰۴ تا ۰/۰۵ درصد گوگرد هستند. همچنین دارای سیالیت بالا و عدم تمایل به ترک های حرارتی گرم است. مصرف عمده این نوع فولاد ها در تولید قطعاتی نظیر غلتک های نورد گرم، چرخ دنده ها، قالب های اکستروژن و قطعات مقاوم در مقابل سایش است.
فولاد های آلیاژی
۱- مقدمه
در مواردی که به استحکام و خواص مکانیکی بالایی نیاز نباشد فولاد های ساده کربنی بسیار مطلوبند. این نوع فولاد ها به خوبی در دماهای معمولی و در محیط هایی که چندان خورنده نیستند به کار می روند، ولی سختی پذیری کم، مستحکم شدن آنها را به استثنای قطعاتی با مقطع نازک، محدود می کند. تقریباً تمام فولاد های سخت شده را برای رفع تنش های پسماند باز پخت می کنند. در بخش قبل گفته شد که فولاد های ساده کربنی، با افزایش دما بسیار نرم می شوند. این رفتار، محدودیت هایی در کاربرد این نوع فولاد ها در دمای های بالا به وجود آورده است. بیشتر محدودیت های فولاد های ساده کربنی را می توان با افزودن عناصر آلیاژی برطرف نمود.
فولاد آلیاژی را می توان به عنوان فولادی تعریف کرد که خواص مشخصه آن از عنصر دیگری به غیر از کربن ناشی می شود. گرچه فولاد های ساده کربنی هم مقداری منگنز (تا حدود ۰/۹ درصد) و سیلیسیم (تا حدود ۰/۳ درصد) دارند، ولی آنها را فولاد آلیاژی نمی نامیم، زیرا این عناصر برای اکسید زدایی به فولاد افزوده شده اند و وظیفه آنها ترکیب شدن با اکسیژن و گوگرد به منظور کاهش اثرات مضر آنهاست.
۲- هدف از آلیاژی کردن
عناصر گوناگون با اهداف مختلفی به فولاد افزوده می شوند که مهمترین آنها عبارتند از:
۱- افزایش سختی پذیری
۲- افزایش استحکام در دماهای معمولی
۳- افزایش خواص مکانیکی در دماهای بالا و پایین
۴- افزایش چقرمگی در هر سختی و استحکام
۵- افزایش مقاومت سایشی
۶- افزایش مقاومت در برابر خوردگی
۷- بهبود خواص مغناطیسی
عناصر آلیاژی بسته به نحوه توزیع در اجزای مختلف فولاد تابکاری شده به دو دسته تقسیم می شوند: عناصری که در فریت حل می شوند و عناصری که با کربن ترکیب شده و کاربید های ساده یا پیچیده تشکیل می دهند.
۳- اثر عناصر آلیاژی بر فریت
می توان گفت همه عناصر تا حدودی در فریت حل می شوند، ولی همه آنها کاربید تولید نمی کنند. عناصری مانند نیکل، آلومینیوم، سیلیسیم، مس و کبالت به مقدار زیادی در فریت حل می شوند. عناصر دسته دوم نیز در غیاب کربن به مقدار زیادی در فریت حل می شوند. تمایل به تولید کاربید زمانی به وجود می آید که کربن کافی موجود باشد.
طبق اصول کلی سخت گردانی محلول جامد، هر عنصری که در فریت حل شود، سختی و استحکام آن را افزایش می دهد. نقش عناصر زیر در افزایش استحکام، با درصد وزنی یکسان به ترتیب افزایش می یابد: کروم، تنگستن، وانادیوم، مولیبدن، نیکل، منگنز و سیلیسیم. در واقع اثر سخت کنندگی عناصر حل شده کم است و مستحکم کردن فریت در استحکام کلی فولاد سهم اندکی دارد.
۴- فولاد های نیکلی (سری xxx2)
نیکل یکی از قدیمی ترین و اصلی ترین عناصر آلیاژی فولاد محسوب می شود. حلالیت این عنصر در آستنیت نامحدود و در فریت زیاد است و باعث افزایش استحکام و چقرمگی این فاز می گردد. نیکل، دمای بحرانی فولاد را پایین آورده، گستره دمایی عملیات گرمایی را وسعت می بخشد، تجزیه آستنیت را به تأخیر می اندازد و از تشکیل کاربید که حل شدن آن در هنگام آستنیتی کردن مشکل است جلوگیری می کند. نیکل مقدار کربن یوتکتوئید را هم کاهش می دهد؛ بنابراین ساختار فولادنیکلی سخت نشده بیشتر از فولاد ساده کربنی با ترکیب مشابه پرلیت دارد. همچنین پرلیتی که در دمای پایین تری شکل گرفته ظریف تر و چقرمه تر از پرلیت فولاد های غیر آلیاژی است. این عوامل باعث دست یافتن به استحکام بالاتر با کربن کمتر و همچنین افزایش چقرمگی، مومسانی و مقاومت در برابر خستگی می شود. فولاد های نیکلی در زمره فولاد های سازه ای پر استحکامی اند که می توان آنها را به حالت نوردیده مصرف نمود و برای تولید قطعات آهنگری شده بزرگ که با آب دادن سازگاری ندارند بسیار مناسب اند. از فولاد هایی با ۳/۵ درصد نیکل (سری ۲۳xx ) و کم کربن، به طور وسیعی برای کربن دهی چرخدنده ها، پیچ های میل-رابط (شاتون)، پرچ ها و شاه پین ها استفاده می شود. چقرمگی فولاد هایی که ۵ درصد نیکل دارند (سری ۲۵xx) بیشتر است و در مواردی مانند چرخ دنده ها، بادامک ها و میل لنگ های اتوبوس و کامیون کاربرد دارند. اثر نیکل بر سختی پذیری کم است ولی در افزایش چقرمگی به ویژه در دماهای پایین نقش برجسته ای دارد. هر چند فولاد های نیکلی سری ۲xxx از دسته بندی AISI/SAE حذف شده اند، ولی این امر به معنای تولید نشدن این فولاد ها نیست، بلکه مقدار تولید آنها از حداقل معینی کمتر است. در بسیاری از کاربرد ها، فولاد های این سری با فولاد های ارزان قیمت آلیاژی سه تایی سری ۸۶xx جایگزین شده اند.
۵- فولاد های کروم دار (سری xxx5)
کروم عنصری ارزان تر از نیکل است که کاربید های ساده (Cr7C3 ,Cr3C2 , Cr23C6) و پیچیده (۲۳C6(Cr,Fe)) تولید می کند. این کاربید ها سختی بالا و مقاومت سایشی خوبی دارند. کروم تا ۱۳ درصد در آهن و به طور نامحدود در فریت حل می شود. در فولاد های کم کربن، کروم تمایل به حل شدن و افزایش استحکام و چقرمگی فریت دارد. در صورتی که مقدار کروم فولاد از ۵ درصد بیشتر باشد، خواص مقاومت در برابر خوردگی دما بالای آن بسیار افزایش می یابد.
فولاد های ساده کروم دار یعنی سری ۵۱xx حاوی ۰/۶۴ – ۰/۱۵ کربن و ۱/۱۵ – ۰/۷ کروم اند. فولاد های آلیاژی این سری عموماً کربن دهی می شوند. وجود کروم باعث افزایش مقاومت سایشی سطح می شود، ولی چقرمگی مغز فولاد همچون فولاد های نیکلی بالا نیست. در صورت وجود کربن به مقدار متوسط، این فولاد ها در روغن سخت می شوند و برای ساختن فنر ها، پیچ موتور ها، پرچ، محور و غیره به کار می روند. سختی و مقاومت سایشی فولاد آلیاژی پر کربن (۱ درصد) و پر کروم (۱/۵ درصد) سری (۵۲۱۰۰) زیاد است. از این فولاد به طور گسترده ای در ساخت بلبرینگ، رولبرینگ و سنگ شکن ها استفاده می شود. نوع ویژه ای از این فولاد ها که حاوی ۱ درصد کربن و ۴-۲ درصد کروم است، خواص مغناطیسی عالی داشته و برای ساختن مغناطیس های دایمی به کار می رود. فولادهای پر کروم که بیش از ۱۰ درصد کروم دارند در برابر خوردگی مقاوم اند.
۶- فولاد های نیکل – کروم (سری xxx3)
در این نوع فولاد ها نسبت تقریبی نیکل به کروم ۲/۵ به ۱ است. ترکیب خواص چند عنصر آلیاژی معمولاً تلفیقی از خواص هر یک است. اثر نیکل افزایش چقرمگی و داکتیلیته و اثر کروم افزایش سختی پذیری و مقاومت سایشی است. اثر ترکیبی دو یا چند عنصر بر سختی پذیری، معمولاً از جمع آثار همان عناصر به طور مجزا بیشتر است.
فولاد های آلیاژی کروم- نیکلیکم کربن، کربن دهی می شوند. کاربید کروم مقاومت سایشی سطح را افزایش می دهد و هر دو عنصر باعث افزایش چقرمگی مغز می شوند. از فولاد های سری (۳۱xx)که ۱/۵ درصد نیکل و ۰/۶ درصد کروم دارند برای ساختن دنده های مارپیچی، پین، پیستون و غیره استفاده می شود. برای کاربرد های سنگین همانند چرخ دنده ها، محور ها و بادامک های هواپیما مقدار نیکل به ۳/۵ و میزان کروم به ۱/۵ درصد (۳۲xx) افزایش می یابد. از فولاد های کروم – نیکلی با کربن متوسط برای ساختن میل رابط های اتومبیل و محور های محرک استفاده می شود.
فولاد های این سری نیز همانند فولاد های نیکلی از طبقه بندی حذف شده اند. در بعضی موارد، این فولاد ها با فولاد های سه آلیاژی سری های ۸۸xx و ۸۷xx که ارزان ترند جایگزین شده اند.
۷- فولاد های منگنزی (سری xx31)
منگنز یکی از ارزان ترین عناصر آلیاژی است که در تمام فولاد ها به عنوان اکسید زدا وجود دارد. منگنز تمایل به شکنندگی گرمایی(سرخ شکنندگی) ناشی از وجود گوگرد را کاهش می دهد و در نتیجه می توان بر روی فلز کار گرم انجام داد. در صورت کم بودن یا نبودن منگنز در فولاد، فاز سولفیدی FeS تشکیل خواهد شد که در حین انجماد فولاد، قشر نازکی از ترکیب یوتکتیکی در پیرامون دانه های اولیه تشکیل می دهد. در دمای نورد فولاد، این قشر ذوب می شود و در هنگام انجام کار، در طول مرز دانه ها تمایل به ترک خوردگی به وجود می آورد. منگنز برجسته ترین عنصری است که با گوگرد ترکیب می شود. نقطه ذوب سولفید منگنز خیلی بالاتر از نقطه ذوب سولفید آهن یوتکتیک است، لذا در هنگام نورد، سولفید منگنز جامد مانده و اثر منفی کمی بر خواص نورد گرم فولاد ها دارد.
تنها در صورتی که میزان منگنز از ۰/۸ درصد فراتر رود، فولاد را به عنوان فولاد آلیاژی منگنزی می شناسیم. منگنز در افزایش سختی و استحکام فولاد نقشی موثر دارد، لکن تأثیر آن از کربن کمتر است ولی در فولاد های پر کربن موثرتر است. این عنصر، کاربیدزای ضعیفی است و اثر متوسطی بر سختی پذیری دارد. همچون نیکل، منگنز نیز در پایین آوردن گستره بحرانی و کاهش مقدار کربن یوتکتوئید اثر دارد.
فولاد های منگنزی ریز دانه استحکام و چقرمگی غیر عادی دارند. از این فولاد ها برای ساختن چرخدنده ها، هزار خارها، محور ها و لوله های تفنگ استفاده می شود. با افزودن مقدار متوسطی وانادیوم، می توان از فولاد منگنزی برای ساختن قطعات آهنگری شده بزرگ که باید در هوا خنک شوند استفاده کرد. بعد از یکنواخت سازی، خواص این فولاد مانند خواص فولاد ساده کربنی کاملاً سخت و باز پخت شده خواهد بود.
اگر مقدار منگنز از ۱۰ درصد فراتر رود، با آهسته سرد کردن فولاد آستنیتی خواهد شد. فولادی مخصوص که فولاد هادفیلد منگنزی نامیده می شود دارای ۱۲ درصد منگنز است. بعد از عملیات گرمایی کاملاً کنترل شده، استحکام و داکتیلیته این فولاد افزایش می یابد و مقاومت سایشی آن زیاد می شود. فولاد هادفیلد ماده ای مناسب برای کاربردهایی است که نیاز به مقاومت در برابر سایش و فرسایش دارند. نمونه این کاربردها در ساخت ظرف بیل های مکانیکی، ناخنک بولدوزر، سنگ شکن ها، آسیاب ها و ریل های راه آهن است. اگر این فولاد از دمای ۹۴۰ درجه سانتیگراد به آهستگی خنک شود، ساختار آن از کاربید های ترد و بزرگی که دانه های آستنیت را احاطه کرده اند تشکیل خواهد شد. استحکام و داکتیلیته این ساختار کم است. در این حالت استحکام کششی به حدود kg/mm250 و درصد ازدیاد طول نسبی به کمتر از ۱ درصد کاهش می یابد. اما اگر آلیاژی با ترکیب مشابه پس از حل شدن همه کاربید ها، از دمای۹۵۰ درجه سانتیگراد آب داده شود، ساختاری کاملاً آستنیتی با استحکام کششی حدود kg/mm285و درصد ازدیاد طول نسبی ۴۵ درصد و سختی ۱۸۰ برینل خواهیم داشت. در این حالت مقدار استحکام و داکتیلیته آلیاژ خیلی بیشتر از خواص ساختارهایی نظیر ساختار تابکاری شده است. فولاد معمولاً تا زیر ۲۴۵ درجه سانتیگراد باز گرم می شود تا تنش های ناشی از آب دادن کاهش یابند. پس از سریع سرد کردن و در شرایط آستنیتی، فولاد خیلی سخت نیست ولی با قرار گرفتن در محیط کار و تحمل ضربه های مداوم، سختی آن به حدود ۵۰۰ برینل افزایش می یابد. دلیل این افزایش سختی، کار سختی پذیری سریع فولاد های منگنزی و تبدیل مقداری از آستنیت به مارتنزیت است.
۸ – فولاد های مولیبدونی (سری xxx4)
مولیبدن عنصر آلیاژی نسبتاً گرانبهایی است، حلالیت محدودی در آهن دارد و کاربید زای قویی است. مولیبدن اثر شدیدی بر سخی پذیری دارد و نظیر کروم ، استحکام و سختی را در دماهای بالا حفظ می کند. حساسیت فولاد مولیبدنی نسبت به تردی باز پختی از دیگر فولاد های آلیاژی کمتر است. این عنصر غالباً همراه با نیکل یا کروم و یا هر دو به کار می رود. در صورت کربن دهی این فولاد، سطحی سخت و مغزی چقرمه ایجاد می شود.
از فولاد های ساده مولیبدنی ( سری های ۴۴xx و ۴۰xx) کم کربن، پس از کربن دهی برای ساخت هزار خارها، چرخ دنده های انتقال حرکت و قطعات مشابهی که شرایط کاری خیلی سختی ندارند استفاده می شود. در صورت وجود کربن بیشتر، از این فولاد برای ساختن فنر های مار پیچ و شمش اتومبیل ها استفاده می گردد. فولاد کروم – مولیبدنی (سری ۴۱xx) نسبتاً ارزان و دارای خواص سخت شدن تا عمق، داکتیلیته و جوش پذیری است. از این فولاد به طور گسترده در ساخت مخازن تحت فشار، قطعات اسکلت هواپیما، محور اتومبیل و دیگر کاربرد های مشابه استفاده می شود. فولاد های نیکل – مولیبدنی (سری های ۴۸xx و ۴۶xx) دارای مزایایی مانند استحکام بالا و داکتیلیته ناشی از وجود نیکل، همراه با سخت شدن تا عمق و سهولت ماشین کاری حاصل از مولیبدن اند. آنها چقرمگی خوب، استحکام خستگی و مقاومت سایشی بالا دارند. از این فولاد ها در ساخت چرخ دنده های انتقال قدرت، پین های زنجیر، محور ها و یاتاقان ها استفاده می شود. فولاد های سه آلیاژی نیکل – کروم – مولیبدنی ( سری های ۴۷xx و ۴۳xx) دارای خواص خوب فولادهای نیکل – کرومی بعلاوه سختی پذیری بالای حاصل از مولیبدن اند. از این فولاد ها به طور گسترده در ساخت قطعات سازه ای بدنه و بال و دم هواپیما و هم چنین ارابه فرود استفاده می شود.
۹ – فولاد های تنگستنی
تنگستن اثر زیادی بر سختی پذیری دارد و کاربید زای قویی است، همچنین نرم شدن مارتنزیت در هنگام باز پخت را به تأخیر می اندازد. نقش کلی تنگستن در فولاد شبیه مولیبدن است، هر چند که در شرایط مشابه به مقدار بیشتری از آن نیاز است. تقریباً ۲ تا ۳ درصد تنگستن معادل ۱ درصد مولیبدن است. به دلیل گران تر بودن تنگستن و نیاز بیشتر به آن، کاربرد تنگستن در فولاد های عمومی مهندسی کمتر بوده و بیشتر در فولاد های ابزار به کار می رود.
۱۰- فولاد های وانادیومی
وانادیوم در میان عناصر معمولی آلیاژی گرانترین است. با افزودن حدود ۵/۰ درصد وانادیوم، ساختار قطعه ریخته گری شده یکنواخت، سالم و ریز دانه خواهد شد. وانادیوم در صورت حل شدن اثر زیادی بر سختی پذیری دارد و فولاد با سرد شدن در هوا به خواص مکانیکی بالایی می رسد. فولاد های کربن – وانادیومی در قطعات سنگین آهنگری شده لوکوموتیو ها و ماشین ها ، که یکنواخت سازی می شوند، مصرف دارند.
فولاد های کم کربن کروم- وانادیومی (سری ۶۱xx) در شرایط سطح سخت شده در ساخت قطعاتی چون پین ها و میل لنگ ها به کار می روند. فولاد های کربن متوسط کروم – وانادیومی دارای چقرمگی و استحکام بالا بوده و برای ساختن محور ها و فنر ها مناسب اند. سختی و مقاومت سایشی نوع پر کربن آنها بالاست و برای ساختن یاتاقانها و ابزار به کار می روند.
۱۱ – فولاد های سیلیسیمی(سری xx92)
سیلیسیم نیز مانند منگنز به عنوان اکسید زدای ارزان در همه فولاد ها یافت می شود. اگر مقدار سیلیسیم در فولاد از ۰/۶ درصد فراتر رود، در طبقه بندی فولاد سیلیسیمی قرار می گیرد. سیلیسیم نیز همانند نیکل، کاربید ساز نبوده و بیشتر در فریت حل می شود و استحکام و چقرمگی را افزایش می دهد. فولاد حاوی ۱ تا ۲ درصد سیلیسیم فولاد دریایی نام دارد و در ساخت قطعاتی که نیاز به نقطه تسلیم بالا دارند مصرف می گردد. فولاد هادفیلد سیلیسیمی با کمتر از ۰/۰۱ درصد کربن و حدود ۳ درصد سیلیسیم دارای خواص مغناطیسی عالی بوده و در هسته ها و قطب های ماشین های الکتریکی به کار می رود.
ترکیب متعادلی از سیلیسیم و منگنز فولادی با استحکام بالای غیر عادی و چقرمگی و داکتیلیته خوب می سازد. از فولاد سیلیسیم – منگنزی (۹۲۶۰) به طور گسترده در ساخت فنر های مارپیچ و شمش، رنده ها و منگنه ها استفاده می شود.
۱۲- فولادهای مقاوم به حرارت
امروزه فولادها در شرایط متغیر و گسترده ای، شامل محیط هایی با دمای بالا و خورنده تحت شرایط تنش استاتیکی و دینامیکی از قبیل دریچه های موتور هواپیما، حامل های کوره، روتورها ، واحدهای کراکینگ نفت و توربین های گازی بکار می روند. سه مشخصه برای فلزاتی که در دمای بالا به کار می روند مورد نیاز است :
۱- مقاومت به اکسیداسیون و پوسته شدن
۲- حفظ استحکام در دمای کاری
۳- پایداری ساختار؛ با توجه به رسوب کاربیدها، کروی شدن، کاربیدهای سیگما و تردی بازپخت
ویژگی های دیگر ی همچون مقاومت ویژه و ضریب حرارتی برای اهداف الکتریکی، ضریب انبساط برای واحدهای ساختمانی و مقاومت به نفوذ در اثر پدیده سوختن در بعضی کاربردهای کوره ای نیز ممکن است در کاربرد مهم باشند. در مورد فولادهای مخصوص توربین های گازی مشخصات دیگری نیز مانند ظرفیت میرایی داخلی و استحکام خستگی، حساسیت به فاق و استحکام ضربه ای ( سرد و گرم )، مشخصه جوشکاری و ماشینکاری، به ویژه در روتورهای بزرگ که باید با حداقل مقاطع جوشکاری شده ساخته شوند مطرح می شود.
پوسته اکسیدی که بر روی آهن شکل می گیرد متخلخل بوده و چسبنده نیست، اما این پوسته در اثر اضافه کردن عناصر ویژه ای به فولاد، چسبنده و محافظ می شود. این عناصر شامل کروم، سیلیسیم و آلومینیوم اند که به وسیله میل ترکیبی زیاد با اکسیژن توصیف می شوند؛ اما واکنش به واسطه شکل گیری فیلم اکسیدی خنثی به سرعت متوقف می شود. مقاومت به اکسیداسیون فولاد نرم به وسیله شکل گیری آلیاژ آهن – آلومینیوم در سطح، به مقدار زیادی بهبود می یابد. این عمل به وسیله حرارت دادن در ۱۰۰۰ درجه سانتیگراد و تماس با پودر آلومینیوم (Calorising ) یا اسپری حرارتی انجام می شود.
بهبود مقاومت خزشی نیز به وسیله روش های زیر بدست می آید :
– بالا بردن دمای نرم شدن به وسیله انحلال عناصر آلیاژی
– استفاده معقول از رسوب سختی در دمای کاری بدون پدیده فراپیری. سختی فاز ثانویه شدیداً به درجه یکنواختی و پراکندگی بدست آمده و ضریب خزش به دامنه فاصله اجزا وابسته است .
– کنترل درجه کارسختی در بازه دمایی مناسب که اغلب اندازه خزشی اولیه را کاهش می دهد.
– تغییرات در پروسه تولید ، اکسیژن زدایی و ذرات درون مرزهای کریستالی نیز می توانند روی خواص خزشی تأثیر گذار باشند.
– ذوب در خلأ مزایایی دارد که در روش های معمول نمی توان به آنها دست یافت .
خواص مکانیکی نیز بوسیله اضافه کردن عناصر گوناگون بهبود می یابد. کبالت، تنگستن و مولیبدن باعث افزایش مقاومت فولاد در برابر عمل تمپر می شوند. فولادهای آستنیتی آلیاژی هیچ تغییری ندارند و بنابراین بوسیله سرد کردن در هوا سخت نمی شوند، لذا مقاومت به سایش آنها خوب نیست. مقدار کافی از عناصر آلیاژی همچون سیلیسیم و کروم خط Ac را بالا می برند. فولاد با درصد بالای نیکل نباید در دمای بالا در تماس با دی اکسید گوگرد و یا دیگر ترکیبات گوگردی قرار گیرد؛ زیرا فیلم های کریستالی سولفید نیکل شکل می گیرد.
در فولادهایی با کروم بالا کاربیدها به هم پیوسته و بزرگ می شوند، که این منجر به کاهش رشد دانه های فریت در دمای بالای ۷۰۰ درجه سانتیگراد می شود. رشد بیش از اندازه دانه ها باعث کم شدن تافنس می شود. رشد دانه در بالای ۱۰۰۰ درجه سانتیگراد در فولاد های آستنیتی هیچ مشکلی بوجود نمی آورد؛ زیرا این فولادها حتی در شرایط درشت دانه نیز چقرمه و داکتیل باقی می مانند.
۱۳ – فولاد های زنگ نزن
آهن خالص بسیار نرم تر از آن است که بتوان از آن استفاده نمود. اما اضافه کردن مقداری از عناصر دیگر ( مانند کربن، منگنز، سیلیسیم) به طور مشخص استحکام مکانیکی آن را افزایش می دهد. در مورد کروم اضافه شده به آهن مزیت دیگری نیز وجود دارد که باعث افزایش قابل توجهی در مقاومت به خوردگی آهن خالص می شود.
فولاد زنگ نزن یک لغت عمومی برای یک خانواده بزرگ از آلیاژهای مقاوم در برابر خوردگی است که حداقل ۵/۱۰ درصد کروم (مطابق با استاندارد اروپایی EN 10088) دارند. مهمترین ویژگی برای آلیاژهای حاوی کروم در گروه فولادهای زنگ نزن دارا بودن کروم به حدی است که آنها را نسبت به خوردگی، اکسیداسیون و گرما مقاوم می سازد.
فیلم اکسید کروم نازک ولی فشرده که روی سطح فولاد زنگ نزن تشکیل می شود باعث ایجاد مقاومت به خوردگی در آن می شود. از جمله ویژگی های دیگر این آلیاژها شکل پذیری عالی، چقرمگی زیاد در دمای پایین و مقاومت خوب در برابر پوسته شدن، اکسایش و خزش در دماهای بالاست.
ممکن است عناصر دیگری نظیر نیکل، مولیبدن، کربن، منگنز، نیتروژن، گوگرد، فسفر، سیلیکون و… نیز در این فولاد به کار رود. نیکل عمدتاً موجب بهبود انعطاف پذیری و فرم پذیری فولاد زنگ نزن می گردد. مولیبدن نیز باعث افزایش مقاومت به خوردگی در محیط های کلریدی و کاهش احتمال ترک برداشتن در آلیاژهای Fe-Cr و آلیاژهای Fe-Cr-Ni می شود. حضور منگنز در فولادهای زنگ نزن باعث افزایش سختی پذیری و نیتروژن نیز باعث افزایش مقاومت در برابر خوردگی حفره ای فولادهای زنگ نزن می گردد. کربن نیز یک عنصرآستنیت زای قوی است که استحکام فولاد را افزایش می دهد. اثر کربن در مقاومت به خوردگی در تمام آلیاژهایی که کربن حضور دارد دیده می شود. اگر کربن با کروم یک ترکیب جداگانه مثل کاربید کروم بسازد، با مصرف کروم از محلول جامد اثر نامطلوبی بر روی مقاومت به خوردگی آلیاژ خواهد گذاشت. این اثر زمانی بوجود می آید که آلیاژ به آرامی پس از کار گرم یا آنیل سرد شود. این رسوب کاربید در مرزدانه ها تشکیل شده و باعث کاهش مقاومت به خوردگی فولاد می شود.
فولادهای زنگ نزن به پنج گروه تقسیم می شوند: مارتنزیتی، فریتی، آستنیتی، آستنیتی- فریتی یا دوفازی و رسوب سختی شونده.
فولادهای زنگ نزن مارتنزیتی (( Fe-Cr-C-(Ni-Mo) حاوی ۱۱/۵تا ۱۸ درصد کروم و حدود ۰/۱۵تا ۱/۲ درصد کربن است و در مقایسه با دیگر فولادهای زنگ نزن، مولیبدن هم می تواند در ترکیب آن استفاده شود. بیشترین کاربرد این فولادها در تیغه های چاقو، ابزار جراحی، شفت ها و … است.
فولادهای زنگ نزن فریتی(Fe-Cr-Mo) دارای ۱۰/۵ تا ۳۰ درصد کروم و ۰/۸ درصد کربن است. این فولاد به دلیل افزایش مقاومت به خوردگی در محیط های کلریدی در سیستم های اگزوز و قسمت های داخلی خودرو استفاده می شود. این گروه زمانی انتخاب می شوند که چقرمگی ضرورت اولیه نباشد و مقاومت به خوردگی در مقابل تنش های کلریدی مورد نیاز باشد.
در فولادهای زنگ نزن آستنیتی(Fe-Cr-Ni-Mo) کربن در حد پایین و کمتر از۰/۸ درصد نگه داشته می شود وکروم در محدوده ۱۶ تا ۲۸ درصد متغیر بوده و میزان نیکل ۳/۵ تا ۳۲ درصد است. این آلیاژها با عملیات حرارتی سخت نمی شوند و خواص کلیدی مانند مقاومت به خوردگی، انعطاف پذیری و چقرمگی در این فولادها بسیار عالی است. کاربرد این فولادها در تجهیزات مواد غذایی، تجهیزات محصولات شیمیایی، کاربردهای خانگی و ساختمانی است.
در فولاد زنگ نزن دو فازی آستنیتی – فریتی(Fe-Cr-Ni-Mo-N) نیز میزان کربن در حد پایین و کمتر از ۰/۳ درصد در نظر گرفته می شود. کروم نیز در محدوده ۲۱ تا ۲۶ درصد و میزان نیکل در بازه ۳/۵ تا ۸ درصد متغیرند. این آلیاژها ممکن است بیش از ۴ درصد مولیبدن داشته باشند. این آلیاژها دارای خاصیت مغناطیسی بوده و استحکام کششی و تسلیم بالاتری نسبت به فولادهای زنگ نزن آستنیتی دارند. کاربردهای متداول این آلیاژها در کارخانه های پتروشیمی، تولید نمک، مبدل های حرارتی و صنعت کاغذسازی است.
آخرین گروه از فولادهای زنگ نزن فولاد رسوب سختی شونده(PH) (Fe-Cr-Ni-(Mo-Al-Cu-Nb)-N) می باشند. استحکام بالا، مقاومت به خوردگی متوسط و تولید آسان از مزیت های اولیه این آلیاژها است. بعد از عملیات حرارتی در دمای پایین حدود (۶۶۰-۵۰۰) درجه سانتیگراد استحکام بسیار افزایش می یابد. در دماهای کمتر اعوجاج کمتری در قطعه رخ می دهد، لذا آنها را برای مصارف با دقت بالا می توان به کار برد.
فولادهای زنگ نزن رسوب سختی شونده دارای ریزساختار مارتنزیتی یا آستنیتی می باشد. فولادهای آستنیتی می توانند با عملیات حرارتی تبدیل به نوع مارتنزیتی شوند البته قبل از اینکه رسوب سختی رخ دهد. رسوب سختی زمانی رخ می دهد که عملیات حرارتی باعث تشکیل شدن ترکیبات بین فلزی شود. رایج ترین موارد استفاده از این آلیاژ در صنایع هوافضا و دیگر صنایع با تکنولوژی بالاست.
انواع چدن
چدن سفید
تمامی کربن موجود در آن به حالت ترکیب و به صورت سمنتیت وجود دارد. چدن سفید هیپویوتکتیک شامل پرلیت و لدبوریت است.سطح مقطع این چدن دارای ظاهری سیاه و سفید است. این چدن مصرف صنعتی کمتری داشته و عمدتاً در ساخت چدن مالیبل از آن استفاده می شود.
چدن خاکستری
قسمت عمده یا تمام کربن موجود درساختمان آن به صورت ورق های آزاد کربن (گرافیت) می باشد. چدن خاکستری دارای مقطعی به رنگ خاکستری تیره یا تقریباً سیاه است. تمام چدن هایی که کربن به صورت آزاد در آنها به صورت ورقه ای یا لایه ای وجود دارد در زمره چدن های خاکستری قرار می گیرند.
وقتی که چدن ازحالت مذاب منجمد می شود، گرافیت با فوق تبرید پایین شکل می گیرد. سرد کردن آهسته، شکل گیری گرافیت را تشدید می نماید. سرد کردن سریع (تا اندازه ای یا حتی بطورکامل) مانع تشکیل گرافیت (گرافیتی شدن) گشته و منجر به شکل گیری سمنتیت می گردد.
گرافیت ثانویه وگرافیت یوتکتو ییدی بر روی ذراتی که قبلاً شکل گرفته اند. نشسته و ابعاد آنها را زیاد می کنند. وقتی که چدنی را که کربن موجود در آن به صورت کاربید است تا درجه حرارت بالا گرم کرده و برای مدت طولانی در آن درجه نگه داریم عمل گرافیتی شدن صورت می گیرد (یعنی سمنتیت به گرافیت تبدیل می شود). در این مرحله ذرات فاز پایدارگرافیت جوانه زایی کرده و رشد می نمایند درحالیکه کریستالهای سمنتیت حل می شوند. بدین ترتیب پس از مدتی فاز ناپایدار (سمنتیت) ناپدید می شود.
مکانیزم گرافیتی شدن هنوز کاملاً روشن نشده است. طبق نظر بونین این فرآیند شامل مراحل زیر است:
۱- حل شدن سمنتیت در آستنیت
۲- نفوذ اتم های کربن به طرف مراکز تجمع گرافیت
۳- اتم های آهن مناطقی از محلول جامد را که ذرات گرافیت در آنجا هسته سازی و رشد می نمایند، ترک می کنند. این موضوع را خودنفوذی آهن یا Self-Diffusionمی نامند.
۴- کربن از محلول رسوب می کند یعنی ذرات گرافیت تشکیل می شوند. سرعت گرافیتی شدن بوسیله آهسته ترین قسمت فرآیند که همان خودنفوذی آهن است (یعنی مرحله ای که در آن مناطقی را که گرافیت در آنجا تشکیل می شود ترک می کنند) محدود می گردد.
حرکت اتم های آهن در آستنیت (یا فریت) تاحد قابل ملاحظه ای کندتر از نفوذ اتم های کربن است و این به واسطه کوچکترین بودن نسبی اتم های آهن می باشد. بنابراین اغلب هنگامیکه آلیاژهای آهن-کربن درحالت جامد سرد می شوند پدیده گرافیتی شدن نمی تواند رخ دهد درحالیکه سمنتیت نسبتاً ساده شکل می گیرد زیرا فقط مستلزم نفوذ کربن و مرتب شدن مجدد اتم های آهن به مقدار جزئی است.
عناصر آلیاژی اضافه شونده به چدن را به دوگروه دسته بندی کرده اند:
۱- عناصر گرافیت زا (شامل C,Ni,Al,Si و غیره) که باعث تسریع در عمل تجزیه سمنتیت می شوند.
۲- عناصر کاربیدزا (شامل Mo,V,W,Cr,Mn و غیره) که در سمنتیت حل شده و مانع تجزیه آن می شوند.
با تغییر مقدار عناصر گرافیت زا و کاربیدزا در چدن می توان درجات مختلفی از تجزیه سمنتیت را بدست آورد. در عمل ساده ترین راه برای این کار تغییر مقدار سیلیسیم است. ساختمان هر ترکیب چدن بستگی به سرعت سرد کردن قطعه ریختگی (ضخامت دیواره) دارد.
ارتباط بین خواص و ساختمان آن بسیار پیچیده تر از ارتباط بین خواص و ساختمان فولاد است. چدن خاکستری شامل یک شبکه فلزی است که ذرات گرافیت در آن توزیع شده اند. بنابراین خواص چدن را می توان به وسیله ساختمان شبکه و وضعیت ذرات گرافیت آن تعیین کرد. تأثیر وضعیت ذرات گرافیت بر خواص چدن را فقط می توان به صورت کیفی اندازه گیری کرد. هر چه این ذرات بزرگتر بوده و مقدار آنها کمتر باشد فلز ضعیف تر خواهد بود.
ذرات گرافیت موجود در چدن را می توان به صورت ترک ها یا شکاف های داخلی در نظر گرفت که مانع پیوستگی فلز می گردند. شبکه فلزی چدن های ریختگی معمولی شامل پرلیت و فریت است. افزایش پرلیت باعث بهبود خواص مکانیکی آنها می شود.
چدن های معروف به چدن های پرلیتی وسیع ترین کاربرد را در صنایع مهندسی دارند. ریزساختار این چدن ها شامل یک زمینه پرلیتی است که در آن گرافیت به صورت ورقه های نازکی گسترده شده است. مقدار ورقه ها باید تا حد امکان کم بوده وکاملاً از یکدیگر جدا باشند. تجمع گرافیت در شبکه نامطلوب است زیرا معمولاً گرافیت به وسیله فریت احاطه شده و به دست آوردن یک شبکه پرلیتی خالص که خواص مکانیکی بالایی داشته باشد را مشکل می سازد. تمام چدن های خاکستری که درحال حاضر مورد استفاده قرارمی گیرند را می توان به گروههای زیر طبقه بندی کرد:
چدن های با استحکام پایین
مقاومت کششی این چدن ها از ۱۲ تا ۲۱ کیلوگرم بر میلی متر مربع و مقاومت خمشی آنها ۲۸ تا ۴۰ کیلوگرم بر میلی متر مربع است. آنالیز شیمیایی تقریبی این چدن ها به صورت زیر می باشد:
Si =1.7-3.0 C =3.2-3.6 p < 0.5 Mn < 0.5 S < 0.12
ریزساختار این چدن ها شامل”فریت + گرافیت” یا “پرلیت + فریت + گرافیت” است. گرافیت دراین چدن ها به شکل ورقه ای است. این چدن ها برای اجزائی از ماشین ها که در عمل تحت تأثیر بارهای سبک قرار می گیرند بکار برده می شوند.
چدن های با استحکام متوسط
این گروه چدن ها در ریخته گری اجزاء ماشین آلات پر قدرت، پیستون ها، سیلندرها و غیره به کاربرده می شوند. این گروه شامل چدن های پرلیتی است. به هنگام ذوب این چدن ها حدود۱۰ تا ۳۰ درصد قراضه به بار کوره کوپل اضافه می شود. این قراضه ها دارای مقدار کربن کمتری هستند و به دست آوردن یک زمینه پرلیتی با توزیع ذرات گرافیت روی آنها امکان پذیر است. ترکیب تقریبی این چدن ها به صورت نشان داده شده در زیر می باشد:
Si =1.5-1.7 C =2.8-3.0 Mn =0.8-1.0 P < 0.3 S < 0.12
مقدار سیلیسیم در این چدن ها باید در حدی باشد که از ایجاد کربن به صورت ترکیبی (Fe3c) جلو گیری نماید. این گروه شامل چدن های تلقیح شده نیز می باشد. این چدن ها با افزودن مواد مخصوصی به نام مواد تلقیحی (فروسیلیس با ۷۵ درصد سیلیسیم، کلسیم سیلیسید و غیره)به چدن مذاب قبل از ریختن به داخل قالب تهیه می شوند.
هدف اصلی از تلقیح عبارت است از تسریع شکل گیری ترکیب یوتکتیکی و سمنتیت ثانویه، ازبین بردن تجمع گرافیت در شبکه و به دست آوردن یک زمینه پرلیتی با ذرات ریز گرافیت. عمل تلقیح معمولاً بر چدن های کم کربن که محتوی مقدار نسبتاً کمی سیلیسیم و مقدار زیادی منگنز هستند اعمال می شود. بدون مواد تلقیحی ساختمان بدست آمده به صورت ساختمان چدن خالدار (یعنی پرلیت + گرافیت + سمنتیت) خواهد بود. در این نوع چدن ها هر چه مقدار کربن کمتر باشد مقدار گرافیت هم کمتر خواهد بود. هر چه مقدار سیلیسیم،کربن و منگنز زیاد باشد، شکل گیری پرلیت آسان تر می شود. ترکیب تقریبی این چدن ها به صورت زیر است:
Si =1.0-1.5 C =2.9-3.2 S < 0.12 P < 0.3 Mn < 0.8-1.0
مصرف مواد تلقیحی باعث پایین آمدن درجه فوق تبرید، اکسیژن زدایی چدن و تولید جوانه های فراوان در مذاب می شود. با کم شدن درجه فوق تبرید می توان از سخت شدن و تجمع مناطق گرافیتی جلوگیر ی نمود. چدن های تلقیحی برای قطعاتی از ماشین که تحت سایش قرار دارند مانند چرخ دنده ها، سیلندرهای ترمز، سیلندرهای ماشین بخار و غیره به کار برده می شوند.
عاملی که در انتخاب گروه چدن باید به خاطر سپرده شود این است که هنگامی که سرعت سرد شدن کم می شود (با افزایش ضخامت دیواره های قالب) خواص مکانیکی پایین می آید. این امر مربوط به درشت تر شدن پرلیت در مقاطع ضخیم و تشکیل مقدار قابل ملاحظه ای فریت + پرلیت است.
چدن های با استحکام زیاد
این گروه را چدن های نشکن یا داکتیل و یا چدن های با گرافیت کروی (SG) می نامند. این چدن ها با اضافه کردن مقدار کمی منیزیم (در دمای ۱۴۵۰- ۱۴۰۰ درجه سانتی گراد) به مذاب چدنی که دارای ترکیبی مشابه با ترکیب شیمیایی چدن خاکستری معمولی است به دست می آیند. هر چه قطعه ریختگی بزرگتر باشد مقدار منیزیم اضافه شونده نیز بیشتر خواهد بود معمولاً مقدار منیزیم را ۰/۳ تا ۱/۲ درصد وزن کل چدن انتخاب می کنند. رسوب منیزیم طی انجماد در ریزساختار چدن سبب می شود که گرافیت به جای آنکه به صورت ورقه ای رسوب کند (مانند چدن خاکستری) به شکل گرد و کروی در آید. وجود گرافیت به این شکل باعث افزایش خواص مکانیکی می گردد. لذا منیزیم علاوه بر تغییر شکل گرافیت استحکام زمینه را نیز بالا برده و باعث افرایش ظرفیت چدن تحت فوق تبرید و در نتیجه سخت شدن آن می شود.
چدن انعطاف پذیر دارای ریزساختاری شامل پرلیت + فریت + گرافیت کروی شکل است وگاهی نیز شامل فریت + گرافیت کروی می باشد دراین حالت تشکیل فریت مطلوب است زیرا بدون کم شدن استحکام، قابلیت نیز زیاد می شود. وجود گرافیت کروی اثر عملیات حرارتی را به شدت افزایش می دهد.
در اینجا یاد آور می شویم که نوع دیگری از دسته بندی چدن ها به صورت چدن های کم آلیاژ و پرآلیاژ است که امروزه کاربرد های وسیعی درصنعت پیدا کرده اند. در گروه چدن های کم آلیاژ، مقدار عناصر آلیاژی از ۳ درصد تجاوز نمی کند. مقصود اصلی ما از آلیاژ کردن عبارت است از افزایش استحکام، مقاومت به خوردگی، مقاومت حرارتی، مقاومت به پوسته شدن حرارتی، مقاومت به سایش و نیز بدست آوردن خواص مغناطیسی مورد نیاز و غیره.
آلیاژ کردن مرکب که در آن مجموعه ای از عناصر کار بیدزا وگرافیت زا مانند کروم، نیکل، منگنز، سیلیسیم و… به چدن اضافه می شود، موثرترین نوع آلیاژ کردن است.
چدن مالیبل
چدن مالیبل نیز مانند چدن خاکستری شامل یک زمینه پرلیت یا فریت وگرافیت های شبه کروی است. در چدن خاکستری گرافیت ها طی انجماد وسرد کردن بعدی بصورت ورقه هایی ته نشین می شوند. چدن مالیبل شامل گرافیت شبه کروی (به نام کربن حرارتی) است وافزایش قابل ملاحظه خواص مکانیکی چدن در نتیجه همین امر می باشد. چدن مالیبل در نتیجه فرآیند آنیل کردن مخصوص (به نام چکش خوار کردن) از چدن سفید بدست می آید. در تولید قطعات ریختگی از جنس چدن مالیبل دو نوع چدن سفید از انواع دیگر مناسب تر است:
۱- نوع کم کربن با ترکیب:Si = 1.4-1.6 C = 1.7-2.7 Mn = 0.4-0.7 P = 0.2-1 S = 0.12
۲- ترکیب کوپل معمو لی با آنالیز:Si=1.4-1.6 C=2.8-3.2 Mn=0.4-0.7 p=0.2 S=0.12
مراجع
http://rasekhoon.net
http://sokan.blogfa.com