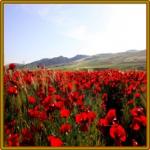
سلام به وب من خوش آمدید دوستان و همراهان عزیز از اینکه مهمان این وب هستید بسیار سپاسگزارم منتظر نظرات سازنده ی شما دوستان هستم
عنوان | پاسخ | بازدید | توسط |
![]() |
1 | 1215 | piskesvat |
![]() |
3 | 2709 | mehran99 |

بررسی خوردگی آلیاژهای آلومینیم (Corrosion of aluminium Aloys) مستلزم بررسی طبیعت شیمیایی آلومینیم است. آلومینیم فلز فعالی است که مقاومت آن به خوردگی به پسیو شدن با لایه سطحی محافظ بستگی دارد. در محلول های آبی، شرایط ترمودینامیکی که تحت آن لایه رشد می کند معمولا با دیاگرام پتانسیل – pH پوربه نمایش می دهند. این نمودار نشان می دهد که آلومینیم تنها در محدوده برابر با 4 pHتا 9 پسیو است. اکثر آلیاژهای آلومینیم مقاومت به خوردگی به اتمسفر طبیعی، آب شیرین، آب شور، بسیاری از روغن ها و مواد شیمایی و هم چنین مواد غذایی دارند. لوله های آلومنیمی در خنک کننده های فریونی مورد استفاده قرار می گرفتند.
خوردگی آلیاژهای آلومینیم در آب
آلیاژهای سری 1xxx، 3xxx، 5xxx و 6xxx مقاومت به خوردگی را در آب های با خلوص بالا، آب های طبیعی و آب دریا نشان می دهند. هنگامی که این آلیاژها برای نخستین بار در معرض آب با خلوص بالا قرار می گیرند، واکنش ملایمی رخ می دهد اما با گذشت زمان و تشکیل لایه محافظ اکسیدی سرعت واکنش کاهش می یابد.
آلیاژهای آلومینیم از سری های 1xxx ،3xxx، 5xxx و 6xxx مقاومت خوبی به اکثر آب ها طبیعی نشان می دهند. اگر خوردگی رخ دهد، به شکل حفره دار شدن خواهد بود. اجزای اصلی آب طبیعی که منجر به خوردگی حفره دار شدن آلومینیم می شوند، یون های مس، بی کربنات، کلراید، سولفات و اکسیژن هستند.این آلیاژها در آب های سخت تمایل بیشتری به حفره دار شدن دارند.
اشکال خوردگی آلیاژهای آلومینیم
-خوردگی یکنواخت:
اکثر آلیاژهای آلومینیم مقاومت عالی به خوردگی اتمسفری دارند. اگر لایه اکسید سطحی در محیط محلول مانند اسید فسفریک یاهیدروکسید سدیم، آلومینیم قرار بگیرد، به طور یکنواخت و پیوسته حل می شود.
- خوردگی گالوانیک:
آلومینیم و آلیاژهایش نسبت به سایر فلزات به جز روی و منیزیم آندی هستند. در محیطی که آلومینیم در معرض حفره دار شدن قرار دارد باید از اتصال آلومینیم با فلزات کاتدی تر جلوگیری کرد. معروف ترین مثال خوردگی گالوانی آلیاژهای آلومینیم در حین کار هنگامی است که آن ها در تماس با فولاد یا مس بوده و در معرض محیط مرطوب شور قرار گیرند. هم چنین استفاده از مس در مخازن آلومینیم و مبدل های حرارتی مورد استفاده در سیستم های خنک کننده آب مطلوب نیست زیرا حضور چند بخش در میلیون مس در آب ورودی احتمال حفره دار شدن آلومینیم را افزایش می دهد.
موقعیت آلومینیم در سری گالوانی که آلومینیم و آلیاژهایش را نسبت به به اکثر فلزات آندی می کند، سبب می شود تا از این فلز به عوان آند فدا شوند برای حفاظت کاتدی از آلیاژ پایه استفاده شود.
- حفره دار شدن:
از آلیاژهای تجاری، سری های 1xxx، 3xxx و 5xxx مقاومت به حفره دار شدن عالی دارند. اگرچه، با مقدار مس بیشتر از 0.04 درصد، آلیاژهای سری 3xxx به حفره دار شدن حساس هستند. در 0.15% مس، این آلیاژها به خصوص در آب دریا بیشتر دچار حفره می شوند. آلیاژهای 2xxx، 6xxx و 7xxx معمولا روکش می شوند تا در برابر حفره دار شدن حفاظت شوند.
عوامل موثر بر خوردگی حفره دار شدن:
حفره دار شدن معمولا به دلیل حضور مس، جیوه و یون های هالید است که کلرید مخرب ترین آن هاست و معمولا در محل کار وجود دارد.
می توان با حذف عوامل کاهنده مورد نیاز برای واکنش کاتدی از حفره دار شدن جلوگیری کرد. در غیاب اکسیژن محلول یا سایر واکنشگرهای کاتدی، آلومینیم دچار حفره نمی شود زیرا به پتانسیل حفره دار شدن نمی رسد. حفره دار شدن در محلول های خنثی معمولا به وسیله اکسیژن ایجاد می شود.
رفتار خوردگی:
سرعت حفره دار شدن آلومینیم به رفتار پلاریزاسیون بستگی دارد. مانند سایر فلزات پسیو، خوردگی آلومینیم در محدوده پسیو که pH آن 4–9 است ممکن است به صورت حفره دار شدن باشد. حفره دار شدن آلومینیم در ورای این محدوده کم شده و خوردگی به صورت یکنواخت پیش می رود.
خوردگی تنشی:
خوردگی SCC در آلیاژهای خالص تجاری 1xxx، آلیاژهای آلومینیم – منگنز 3xxx و آلیاژهای آلومینیم – منیزیم حاوی 3 درصد منیزیم سری 5xxx و مستحکم شده با کار سرد رخ نمی دهد. در مواقع خاص، خوردگی تنشی در آلیاژهای آلومینیم – منیزیم – سیلیسیم 6xxx رخ می دهد.
آلیاژهای حساس به خوردگی تنشی:
خوردگی تنشی در آلیاژهای آلومینیم ریختگی معمولا به آلیاژهایی که حاوی مقادیر قابل توجهی عنصر آلیاژی مس، منیزیوم، سیلیسیم و روی محدود می شود. آلیاژهایی که می توان با کار سرد استحکام آن ها را افزایش داد نسبتا به خوردگی تنشی مصون هستند. آلیاژهای ریختگی که در معرض خوردگی تنشی قرار دارند شامل موارد زیر می شوند:
- سری 2xxx شامل مس با مقادیر کمتر منیزیم، منگنز و سایر عناصر هستند.
- سری 7xxx حاوی روی با مقدار کمی منیزیم، منگنز، مس و سیلیسیم هستند
- سری 5xxx که بیش از 3 درصد منیزیم دارند با یا بدون عناصر آلیاژی
در آلیاژهای آلومینیم، این ترک خوردگی بین دانه ای است. عواملی که مقاومت به خوردگی تنشی را تحت تاثیر قرار می دهند عبارتند از:
خواص جهت دار آلومینیم: خوردگی تنشی آلیاژ ریختگی آلومینیم در تمپر با اندازه و زمان اعمال تنش کششی و نیز با جهت اعمال تنش مشخص می شود. اثر تنش در جهات مختلف با ساختار جهت دار دانه که در آلیاژهای ریختگی آلومینیم معمول است، ایجاد می شود. مقاومت که با مقدار تنش کششی مورد نیاز برای ایجاد ترک اندازه گیری می شود زمانی بیشترین حد خود را دارد که تنش وارده در جهت طولی است، کمترین حد در جهت عرضی و در سایر جهات متوسط است.
محیط: آب یا بخار آب برای خوردگی تنشی آلومینیم لازم است و در غیاب آن ترک خوردگی ایجاد نمی شود. میان گونه هایی که به ترک خوردن شتاب می دهند، کلرید بیشترین اثر را دارد.
روش تست استاندارد برای تعیین حساسیت به خوردگی تنشی در آلیاژهای آلومینیم با استحکام بالا ASTM G47 است. این استاندارد حساسیت SCC آلیاژ با استحکام بالای 2xxx و 7xxx است هنگامی که جهت تنش وارده عمود بر ساختار دانه ها باشد.
پوسته شدن :
خوردگی سطحی است که از سطح آغاز شده و پخش می شود. این خوردگی در آلیاژهای آلومینیم و مس-نیکل دیده می شود. حمله با حفره دار شدن در این متفاوت است که ظاهر آن به صورت پوسته است و معمولا در طول مرزدانه ها رخ می دهد. حمله های خوردگی منجر به ورقه ورقه شدن و گاهی اوقات سطح تاول دار می شود. به دلیل لایه برداری تمام لایه های ماده خورده می شوند. انتهای نمونه مشابه با دسته ای از کارت می شود که برخی از آنها جدا شده اند.
آلیاژهای حساس به پوسته شدن:
در تمپر های خاص، محصولات ریخته گری شده آلیاژهای آلومینیم در معرض خوردگی لایه ای قرار می گیرند، که منجر به ایجاد محصولات ورقه شده می شود. این خوردگی در محصولاتی پیشروی می کند که ساختار جهت دار دارند و در آن دانه ها کشیده شده اند. آلیاژهای سری 2xxx، سری 5xxx با مقادیر بالاتر منیزیم و سری 7xxx بیشتر در معرض خوردگی لایه ای قرار می گیرند.
این خوردگی در آلیاژهای ریختگی غیر قابل عملیات حرارتی مانند سری 1xxx، 3xxx و تیپ های غیر قابل عملیات حرارتی 6xxx به ندرت دیده می شود. می توان برای غلبه کردن بر این مشکل از عملیات حرارتی و آلیاژ سازی استفاده کرد. روش تست استاندارد برای تعیین حساسیت به خوردگی لایه ای ASTM G34، روش تست غوطه وری برای تعیین ورقه ورقه شدن در آلیاژهای آلومینیم سری 2xxx و 7xxx یا تست EXCO است. این روش تست برای محصولات ریختگی مانند پلیت ها، ورق ها، اکستروژن ها و فورجینگ ها به کار می رود. استاندارد ASTM G66 نیز تست غوطه وری آلیاژهای آلومینیم سری 5xxx برای ورقه ورقه شدن است که به تست ASSET معروف است.
خوردگی بین دانه ای :
آلیاژهای آلومینیم که فاز ثانویه در مرزدانه ها تشکیل نمی دهند یا آلیاژهایی که در آن ها اجزای تشکیل دهنده پتانسیل خوردگی مشابه با زمینه دارند، نسبت به خوردگی بین دانه ای حساس نیستند. آلیاژهای آلومینیم مانند 1100، 3003، 3004 آلیاژهای آلومینیم – منیزیم سری 5xxx که حاوی کمتر از 3 درصد منیزیم هستند دچار خوردگی بین دانه ای نمی شوند. آلیاژهای سری 6xxx معمولا در برابر این نوع خوردگی مقاومت می کنند. عملیات حرارتی در سری 2xxx ،5xxx با بیش از 3 درصد منیزیم و آلیاژهای سری 7xxx که رسوب مرزدانه در آن ها رخ می دهد به خوردگی بین دانه ای حساس هستند. درجه حساسیت به خوردگی با موارد زیر افزایش می یابد:
1- مقدار منیزیم
2- مقدار کار سرد
3- مقدار زمانی که آلیاژ در معرض دما قرار می گیرد.
مقاومت به خوردگی بین دانه ای با استفاده از عملیات حرارتی که منجر به یکنواخت تر شدن رسوب درون ساختار دانه می شود یا با محدود کردن عناصر آلیاژی که خوردگی بین دانه ای را ایجاد می کنند، حاصل می شود.
خوردگی شیاری :
خوردگی شیاری آلومینیم در آب شیرین قابل چشم پوشی است. در آب شور خوردگی به شکل حفره دار شدن رخ داده و سرعت خوردگی پایین است.
خوردگی سایشی، خوردگی حباب زایی و خوردگی برخوردی:
آلومینیم و آلیاژهایش به خوردگش حباب زایی، برخوردی و سایشی حساس هستند.
خوردگی خستگی:
آلیاژهای آلومینیم، مانند بسیای از فولادها، مقاومت کمی در برابر خوردگی خستگی دارند. خوردگی خستگی آلیاژهای آلومینیم مشخصا درون بلوری بوده و با تخریب ناشی از خوردگی تنشی متفاوت است که معمولا بین دانه ای هستند. خوردگی موضعی سطح آلومینیم افزایش تنش را ایجاد کرده و استحکام خستگی و در نتیجه عمر خستگی را به شدت کاهش می دهد.
خوردگی آلومینم در موتور دیزلی با سیستم خنک کننده آب
خوردگی یکنواخت ممکن است در برخی از مخلوط های آب/گلیکول رخ دهد که ممانعت کننده مناسب ندارند. خوردگی موضعی با شکست لایه پسیو توسط یون کلرید آغاز می شود. حفره دار شدن و خوردگی شیاری می تواند با استفاده از ممانعت کننده ها جلوگیری شود. آنیون هایی که برای کاهش اثر خوردگی رایج هستند را می توان به دو دسته تقسیم بندی کرد:
1- اکسید کننده. ممانعت کننده هایی که لایه پسیو روی سطح فلز ایجاد می کنند.
2- غیر اکسید کننده. ممانعت کننده هایی که با تشکیل رسوبات نامحلول با یون های آلومینیم به عنوان عامل مسدود کننده به کار می روند.
بنزوات، فسفات و سیلیکات مثال هایی از ممانعت کننده های غیر اکسید کننده هستند. نیترات ها و کرومات ها از ممانعت کننده های اکسید کننده هستند.
جلوگیری از خوردگی و اقدامات کنترل کننده
روش های مهم جلوگیری از خوردگی آلومینیم شامل موارد زیر می شود:
- انتخاب آلیاژ و عملیات تمپر
2- ملاحظات طراحی تجهیزات
3- ممانعت کننده ها
4- حفاظت کاتدی
5- استفاده از محصولات الکلد Alclad
6- تغییر محیط
7- ضخیم ساختن لایه اکسیدی و پوشش های آلی
- انتخاب آلیاژ و تمپر
در کل، آلیاژهای سری 5xxx آلومینیم – منیزیم بهترین مقاومت به خوردگی را دارند، پس از آن ها آلیاژهای سری 1xxx، 3xxx و 6xxx با خلوص تجاری قرار دارند. آلیاژهای سری 2xxx و 7xxx معمولا لایه محافظ مانند روکش دارند. انتخاب تمپر مقاومت بهتری به خوردگی بین دانه ای و لایه لایه شدن برای آلیاژهای سری 5xxx بدست می دهد در حالی که در آلیاژهای سری 7xxx مقاومت بهتری به خوردگی تنشی ایجاد می شود.
- ملاحظات طراحی
جنبه های طراحی که رفتار خوردگی را تحت تاثیر قرار می دهند شامل انتخاب نادرست آلیاژ یا تمپر، زوج گالوانی، عدم وجود آب بندی در شیارها برای جلوگیری از خوردگی شیاری و انتخاب روش اتصال و فلز پر کننده.
- ممانعت کننده ها
فسفات ها، سیلیکات ها، نیترات ها، فلوریدها و غیره برای استفاده با آلومینم در برخی کاربردها توصیه شده است. اگر مس در سیستم های بسته مد نظر باشد، از مرکاپتوبنزوتیازول برای جلوگیری از خوردگی مس و خوردگی رسوبی آلومینیم استفاده می شود.
حفاظت کاتدی
در برخی کاربردها، قسمت هایی از آلیاژ آلومینیم به وسیله حفاظت کاتدی به وسیله آند فدا شونده یا با جریان اعمالی محافظت می شود. از آنجایی که واکنش کاتدی یون های هیدروکسیل تولید می کند، جریان این آلیاژها نباید به اندازه ای بالا باشد تا محلول را به گونه ای قلیایی کند که خوردگی قابل توجهی ایجاد کند.
آلیاژهای الکلد (Alclad)
استفاده از محصولات الکلد برای مقاومت در برابر خوردگی به خوبی ثابت شده است. آلیاژهای الکلد محصولی کامپوزیتی است که در آن لایه سطحی نازکی از آلیاژ آلومینیم (آندیک)، معمولا 5 الی 10 درصد ضخامت کل به شکل متالورژیکی با آلیاژ اصلی (کاتدیک) پیوند برقرار کرده که برای ایجاد استحکام مورد نیاز و روکش برای ایجاد ماکزیمم مقاومت به خوردگی به خصوص در برابر حفره دار شدن انتخاب می شود. اختلاف پتانسیل بین آلیاژ پایه و روکش حفاظت کاتدی را برای هسته ایجاد می کند. روکشی که معمولا استفاده می شود آلیاژ 7072 است که حاوی 1 درصد روی بوده و پتانسیل محلول آن −0.96 V است که حداقل 100 mV آندی تر از آلیاژهای هسته مانند 3003 و 6951 است. از آنجایی که روکش ها نسبت به هسته آندی هستند، خوردگی انتخابی روکش تا فصل مشترک روکش و هسته اتفاق می افتد. پس از رسیدن به فصل مشترک، خوردگی به صورت عرضی گسترش می یابد و از خوردگی موضعی جلوگیری می شود. محصولات الکلد به شکل ورق و تیوب که در یک طرف یا طرف دیگر پوشش داده شده اند، در دسترس هستند.
به عنوان مثال، تیوب های الکلد برای رادیاتورهای آلومینیمی لحیم شده برای ممانعت از خوردگی لوله در بخشی که در تماس با آب است، استفاده می شوند. ترکیب معمول محصولات الکلد معمولا در کاربردهای مبدل حرارتی مورد استفاده قرار می گیرد که در جدول زیر آورده شده است.
آلیاژهای الکلد | |
آلیاژ روکش | آلیاژ پایه |
7072 | 3003 |
7072 یا 7013 | 3004 , 6061 |
7072 | 6951 |
7072, 7008, 7011 | 7075 |
7072 | 7178 |
تغییر محیط
چنین تغییراتی عبارتند از:
کاهش خوردگی محیط
تنظیم pH محلول
هوازدایی آب برای کاهش مقدار اکسیژن
و در نتیجه کاهش تمایل به حفره دار شدن آلومینیم
- ضخیم کردن لایه اکسید سطحی و پوشش آلی
پوشش هایی با روکش نفوذی یا پاشش حرارتی مشابه با لایه روکش عمل کرده و به صورت فدا شونده خورده می شوند تا از آلیاژ هسته محافظت کنند.
فولادهای نفوذ داده شده با آلومینیم مورد استفاده در مبدل های حرارتی پالایشگاه نفت خام
نفوذ بخار آلومینیم به سطح آلیاژهای پایه آهن یا پایه نیکل یکی از روش های حفاظت از تیوب های فولادی (نام این فرآیند آلونایزینگ است) و سایر اجزای مبدل های حرارتی از اثر مخرب اکسیداسیون دما بالا، سولفیداسیون و کربوریزاسیون است. در نتیجه، این فرآیند کاربردهای وسیعی در مبدل های حرارتی مورد استفاده در پالایشگاه های شیمیایی و پالایشگاه های نفت خام یافته است.
منابع و پیوندها
گردآوری شده توسط دپارتمان پژوهشی شرکت پاکمن
Heat Exchanger Design Handbook 2nd edition, Kuppan Thulukkanam, CRC Press, 2013