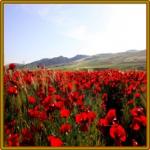
سلام به وب من خوش آمدید دوستان و همراهان عزیز از اینکه مهمان این وب هستید بسیار سپاسگزارم منتظر نظرات سازنده ی شما دوستان هستم
عنوان | پاسخ | بازدید | توسط |
![]() |
1 | 1215 | piskesvat |
![]() |
3 | 2709 | mehran99 |

انواع چسب ها:
تقسیم بندی چسب ها از دو دیدگاه صورت می گیرد: یکی از نقطه نظر ماهیت و طبیعت چسب ها و دیگری از نظر نحوه انجماد و چگونگی خود گیری و سفت شدن چسب ها .
از نقطه نظر ماهیت چسب ها به دو گروه چسب های آلی و غیر آلی و یا دو دسته قابل حل در آب یا غیر قابل حل در آب تقسیم می شوند.
از نقطه نظر نحوه انجماد و چگونگی سفت شدن و خود گیری ،چسب ها به سه نوع برگشت ناپذیر، میانه و برگشت پذیر تقسیم می شوند.
چسب های آب دار و چسب های غیر آب دار نباید با هم دیگر مخلوط شوند زیرا هر زمان که این عمل صورت پذیرد ، استحکام مخلوط ماسه در حالت تر و در حالت خشک کاهش می یابد. و به خصوص اگر چسب آب دار ، خاک رس باشد ، کاهش استحکام شدید تر است.
یک چسب مناسب باید ذرات ماسه را به یکدیگر اتصال دهد و استحکام قالب و ماسه ماهیچه را در حالت تر و خشک افزایش دهد.
همچنین باید شرایط زیر را فراهم سازد:
1- در خلال تهیه مخلوط های قالب گیری یا ماهیچه به طور یکنواخت بر روی سطوح ماسه پایه گسترده شود.
2- در هر دو حالت تر و خشک ، استحکام کافی مخلوط را فراهم سازد.
3- شکل پذیری مناسب در مخلوط ایجاد نماید ،به طوری که مخلوط قادر باشد همه بخش های قالب را پر کند.
4- کمترین چسبندگی را به سطح مدل و جعبه ماهیچه داشته باشد تا انجام فرایند قالب گیری و ماهیچه سازی امکان پذیر شود.
5- امکان خشک کردن سریع قالب و ماهیچه را فراهم سازد و در خلال مونتاژ قالب و نگه داری ماهیچه رطوبت جذب نکند.
6- در خلال مرحله خشک کردن و به هنگام ریخته گری فلز به داخل قالب ، حد اقل گاز را تولید و آزاد سازد.
7- به دیرگدازی ماسه لطمه نزند و سوختن زودرس ماسه را پدید نیاورد.
8- امکان آسان خارج سازی ماهیچه را فراهم سازد.
9- برای افرادی که عملیات تهیه مخلوط ،قالب و ماهیچه را انجام می دهند ، مضر نباشد و گازهای سمی تولید نکند.
10- ارزان و قابل دسترسی باشد.
معمولا چسب های مورد استفاده در ریخته گری را به دو گروه عمده چسب های قالب گیری و چسب های ماهیچه تقسیم بندی می کنند.
از خاک های رسی می توان به عنوان چسب های قالب گیری نام برد و چسب های سیلیکات سدیم ،اتیل و نیز انواع رزین های مورد مصرف در قالب گیری پوسته و....از جمله چسب های ماهیچه هستند.
خاک رس ها معمولا دارای سه مشخصه هستند:
1- همراه با مقدار معینی آب ، خودگیر شده و خاصیت پلاستیکی پیدا می کنند.
2- این مخلوط پس از خشک شدن و دوباره مخلوط کردن با آب ، خود گیر شده و خاصیت پلاستیکی خود را حفظ می کند(درجه حرارت خشک شدن بسیار بالا نیست).
3- اگر درجه حرارت از مقدار معینی افزایش یابد، خاک رس کلسینه شده(مرده شده) و خاصیت خود گیری و پلاستیکی خود را از دست می دهد.درجه حرارت کلسینه شدن با توجه به نوع خاک رسی متغیر می باشد.
در ریخته گری ،خاک رس ها به سه صورت هستند:
1- کائولین: کائولین سیلیکات خالص آلومینیوم با فرمول شیمیایی Al2O3SiO2.H2O می باشد که به خاک چینی معروف است و به خاطر داشتن آلومین زیاد ، خاک نسوز هم نامیده می شود. ناخالصی هایی مانند سدیم، پتاسیم،آهن و کلسیم که به صورت سیلیکات در این خاک ها پدید می آید ، رنگ آن را از صورتی روشن به قهوه ای تیره مبدل می سازد.کائولین خاصیت خودگیری و چسبندگی کمتری نسبت به خاک های رس دیگر دارد. در صورت استفاده در ماسه قالب گیری مقدار زیادی بین 10 تا 20 درصد کائولین لازم است.
2- بنتونیت : مونت موریونیت نوعی سیلیکات آلومینیوم به فرمول شیمیایی Al2O3.4SiO2.nH2O.می باشد که در بعضی موارد یون های منیزیم نیز به جای یون های آلومینیوم حضور دارند.بنتونیت معروف ترین چسب خاک رسی مورد استفاده در ریخته گری است، از خانواده مونت موریونیت می باشد.در صنعت ریخته گری دو نوع بنتونیت مشخص و معروف وجود دارد. یکی بنتونیت غربی یا سدیمی است که از یون های سدیم اشباع شده و می تواند مقدار زیادی آب جذب نماید و افزایش حجم بسیاری دارد. نوع دوم ، بنتونیت جنوبی یا کلسیمی است که نسبت به بنتونیت سدیمی کمتر فعال می باشد. بنتونیت کلسیمی قالب هایی با استحکام تر بیشتر تولید می کند ، در صورتی که استحکام خشک در درجه حرارت های بالای سدیمی بیشتر است. به طور کلی مقدار افزایش بنتونیت به ماسه 2 الی 5 درصد است.
3- خاک رس ایلیت:در اثر تغییرات میکا و تجزیه پوسته های معینی به دست می آید.این خاک ، مواد چسبی اصلی ماسه با چسب طبیعی می باشد.
چسب های مورد استفاده در ماهیچه سازی:
چسب های ماهیچه بسیار متنوع بوده و انواع مختلفی دارند و هر کدام از این چسب ها به منظور معین و ارائه خواص به خصوصی به ماسه ماهیچه اضافه می شوند.
بیشتر چسب های ماهیچه (که در بسیاری از موارد در ساخت قالب نیز به کار میروند)بعد از یک بار استفاده به دلیل تغییرات ساختمانی قابلیت استفاده مجدد را ندارند.
در هر صورت چسب های مورد استفاده در ماهیچه سازی را می توان به چهار گروه تقسیم کرد:
1- چسب هایی که در حالت یخ زدن سخت و محکم می شوند.آب تنها ماده چسبنده است که در دسته فوق در عملیات ریخته گری مورد استفاده قرار می گیرد.در قطعاتی که در کشور روسیه به کمک این نوع ماهیچه ساخته شده ،ادعا شده که مک های داخلی در پوسته های موتور با استفاده از ماهیچه های یخ زده حذف شده است.
2- چسب هایی که در درجه حرارت اتاق سخت و محکم می شوند:
از این دسته می توان سیلیکات سدیم و سیلیکات های مضاعف آلومینیوم و کلسیم یا سیمان را نام برد که در مورد چسب سیلیکات سدیم در بخش جداگانه ای به طور کامل تشریح شده است.
از چسب های سیمان مورد استفاده می توان سیمان پرتلند ، سیمان کائوچوئی و سیمان شیمیایی را نام برد که مهم ترین این نوع سیمان ها ( به عنوان چسب)، سیمان پرتلند است.
عیب ماهیچه های ساخته شده از این چسب های سیمانی این است که قابلیت از هم پاشیدگی آن قالب ساخته شده کم است.
3- چسب هایی که پس از پختن سخت و محکم می شوند:
این چسب ها به سه گروه فرعی زیر تقسیم می شوند:
1-3 - چسب هایی که در حرارت خشک می شوند(روغن ماهیچه) :
در روغن ها سخت کردن از طریق پلاریزاسیون و ایجاد ملکول های بزرگ تر به کمک جذب اکسیژن هوا در درجه حرارت های 200 تا 240 درجه سانتی گراد انجام می گیرد. این چسب ها مرکب از سه نوع چسب های روغنی به نام های روغن های گیاهی ،روغن های معدنی و روغن های جانوران دریایی می باشد.
2-3 – چسب هایی که بعد از حرارت دیدن و در موقع سرد شدن سخت می شوند:
انواع رزین ها یا به عبارتی صمغ ها در این گروه قرار دارند.صمغ به دو نوع طبیعی و مصنوعی تقسیم می شوند.که از صمغ های طبیعی می توان از شیره درختان نام برد. صمغ های مصنوعی نیز با ترکیبی از اوره و فنل فرمالدئید به وسیله پلیمریزاسیون و از دست دادن آب سخت می شوند.چنین چسب هایی بیشتر در ماهیچه سازی گرم و قالب های پوسته ای به کار می روند.
رزین ها از نوع اوره فرمالدئید بهترین مشخصات و بیشترین کاربرد را در تهیه ماهیچه های کوچک و نازک و آن هایی که پس از ریختن مذاب قابلیت از هم پاشیدگی زیادی لازم دارند ،را ارائه می دهند. فنل فرمالدئید قابلیت از هم پاشیدگی کمتری داشته و در تهیه قطعات بزرگ و فولادی به کار می رود. این صمغ به صورت جامد ومایع در بازار وجود دارند و برای مدت زیادی نباید انبار شوند.
3-3 - چسب هایی که خاصیت چسبندگی را در حرارت به دست می آورند:
این گروه از چسب ها شامل چسب های سولفیدی ، چسب های نشاسته ای (دکسترین )، ملاس چغندر قند و چسب های پروتئینی هستند. چسب های نشاسته ای یا دکسترین ها جزو چسب های ماهیچه ای می باشند و معمولا جهت افزایش استحکام تر در مخلوط ماسه ماهیچه مصرف می شوند.مقدار 5/. تا 2 درصد وزنی آن ها استحکام فشاری تر ماسه را به اندازه 1 تا 5/2 پوند بر اینچ مربع افزایش می دهد.
ملاس چغندر قند نیز محصول فرعی کارخانه های تولید قند می باشد که اصولا همراه با چسب های دیگر (به جز چسب های روغنی) به ماهیچه اضافه می شوند.چسب های پروتئینی که انواع خالص تجاری آن ژلاتین،کازئین و سریشم می باشد.
4- چسب های خاک رس:
این دسته از چسب ها اصولا به خاطر افزایش استحکام تر ماسه ماهیچه به مخلوط ماسه ماهیچه اضافه می شوند و مهم ترین آن ها خاک رسی نسوز (کائولین)و بنتونیت می باشند که در چسب های قالب گیری نیز به آنها اشاره شد.
در قسمت سوم و پایانی به مواد افزودنی اشاره خواهد شد.
منبع:
فتحی،محمدحسین:مواد قالبگیری برای ریختهگری فلزات،نشر اركان اصفهان.
مواد قالبگیری-قسمت اول "ماسه"
مواد قالبگیری
در این بخش به تشریح اجزای اصلی مخلوط ماسه قالبگیری یعنی ماسه،چسب،آب و مواد افزودنی پرداخته میشود.
ماسه:
طبق تعریف ماسه عبارت است از ذرات ریز مواد معدنی که قطر آنها از 0.05 تا 1 میلیمتر تغییر می کند.ماسه های مورد استفاده در انواع مختلف با توجه به:
• ترکیب شیمیایی
• درجه دیرگدازی
• نحوه توزیع دانه ها
• در دسترس بودن به کار گرفته می شوند.
انواع ماسه:
ماسه ها انواع مختلفی دارند که از آن جمله میتوان به موارد زیر اشاره کرد:
ماسه سیلیسی:
این ماسه به طور گستردهای در ریخته گری به کار میرود و عمدهترین ماسه مصرفی محسوب می شود.ترکیب اصلی آن سیلیس SiO2 است.
ماسه زیرکن:
ماسه زیرکن که با فرمول شیمیایی ZrSiO4 مشخص می گردد و به عنوان یک ماسه با نقطه گداز بسیار بالا مورد توجه است.
ماسه کرومیتی:
کرومیت یا FeCr2O4ترکیب اصلی این ماسه است و از آن در ریخته گری فلزات با نقطه ذوب بالا استفاده می شود.
ماسه اولوین:
ترکیب این ماسه Fe2SiO2 یا Mg2SiO2 است و مخلوطی است از سیلیکات منیزیم و به عنوان ماسه جایگزین در بسیاری نقاط مورد توجه است.ماسه شاموتی:
ماسه شاموتی نوعی کوارتز دانه ریز است که حرارت زیاد دیده است و به عبارت دیگر ماسه ای است که از زینتر کردن ذرات خاک رس به دست می آید.نگرشی به ماسه های سیلیسی مصرفی ایران
ماسه های مصرفی به دو نوع ماسه های با چسب طبیعی و ماسه های مصنوعی تقسیم میگردند.
1)ماسه با چسب طبیعی:
ماسه با چسب طبیعی محتوی تا 20 درصد خاک ریز و مواد ناخالصی می باشد.کیفیت این نوع ماسه برای قالبگیری ماهیچه سازی بستگی به:
• مقدار چسب
• ترکیب شیمیایی ناخالصی
• نوع مذاب ریختگی دارد.
این ماده در طبیعت بصورت پیش آماده شده وجود دارد.برای استفاده از این نوع ماسه ها تنها مرطوب کردن آنها کافیست از این نوع ماسه در ریخته گری فلزات غیر آهنی با نقطه ذوب پایین نظیر آلومینیوم،برنج ها،برنز ها و قطعات کوچک چدنی استفاده میشود.بطور قطع اینگونه ماسه ها برای ریخته گری قطعات بزرگ چدنی مناسب نیست معایب عمده این نوع ماسه ها عبارت از:
• پایین بودن درجه دیرگدازی
• همراه داشتن درصد تقریبا زیادی اکسید های قلیایی و آهک می باشد.
وجود اسیدهای قلیایی در این نوع ماسه باعث پایین آوردن درجه دیرگدازی آن گشته و در نهایت باعث ایجاد عیوبی نظیر ماسه سوزی و چسبیدن ماسه به قطعات ریختگی می شود.از طرف دیگر مواد آهکی در اثر حرارت دیدن به صورت گاز درآمده و در صورتیکه قطعات ریختگی بزرگ و دارای ضخامت زیاد باشند فرصت ورود به مذاب را داشته و در قطعات ریختگی به صورت مک و حفره های گازی باقی می مانند.
از آنجائیکه این ماسه در نقاط مختلف ایران به وفور یافت می شود و نسبتا ارزان در دسترس ریخته گران قرار می گیرد.لذا در اکثر واحدهای کوچک و متوسط ریخته گری ایران به طور وسیعی در مواد قالبگیری و ماهیچه سازی مصرف دارد. ماسه های گرگان ،رشت،گرمسار،اردکان یزد،حسن آباد قم،عین آباد ،محلات و اطراف یزد جزء این گروه ماسه ها هستند.
ماسه های طبیعی بر حسب میزان خاک رس موجود در آنها به سه دسته تقسیم میشوند:
• ماسه ضعیف که حداکثر تا 8% خاک رس دارد.
• ماسه متوسط که بین 8 تا 18 % خاک رس دارد.
• ماسه خاک یا ماسه ملات که بیش از 18% خاک رس دارد.
معمولا خاک ماسه های طبقات زیرین بیشتر از لایه های سطحی می باشد و ریختگران بایستی پس از آزمایشات دقیق،ماسه مطلوب خود را تهیه نمایند.در ریخته گری معمولا از ماسه های متوسط استفاده می شود.
2)ماسه های مصنوعی:
ماسه مصنوعی از شکستن ،خرد کردن و غربال کردن سنگهای سیلیس به دست می آیند که با اضافه کردن چسب و مواد دیگر قابلیت قالبگیری در آنها ایجاد می گردد.ماسه مصنوعی در مقایسه با ماسه طبیعی دارای مزایای زیر می باشد:
v درجه دیرگدازی و خلوص بالاتر.
v سهولت در کنترل مشخصات فیزیکی و مکانیکی مخلوط.
v قابلیت بازسازی و مصرف مجدد.
v در دسترس بودن.
محدودیت اصلی ماسه های مصنوعی در مقابل ماسه های طبیعی بالا بودن قیمت تمام شده آنها می باشد .با این وجود این ماسه ها می توانند بخوبی نیازهای صنایع ریختگری ایران را در زمینه چدن و فولادریزی(به باستثناء فولادهای خاص که به مصرف ماسه های زیرکونی-کرومیتی و اولوینی نیاز دارند) تامین کنند.
ماسه ها ی سیلیس مصنوعی رایج ترین ماسه ها قالب گیری در واحدهای ریختهگری می باشد و انواع ذرات سیلیسی به عنوان ماده اصلی و دیر گداز ماسه ریخته گری به کار می رود .بیشتر ماسه های قالب گیری از کوارتز معدنی که میتواند تا دمای 1700 درجه سانتیگراد را تحمل کند تشکیل شده است.شکلهای دیگر سیلیس تریدیمیت و کریستومالیت میباشد.
وجود اکسید های آلومینیوم و آهن خاصیت دیرگدازی ماسه را افزایش میدهند و حضور اکسید های پتاسیم و سدیم و ترکیبات میکا چسبندگی و شکل پذیری ماسه را زیاد و قابلیت دیرگدازی آن را کاهش می دهد و لذا در ترکیبات ماسه سیلیس وجود اکسید های قلیایی و قلیایی خاکی مضر تشخیص داده میشود. علاوه بر مسئله فوق وجود انواع اکسید ها باعث ایجاد رنگهای قرمز و قهوه ای،اکسید های سدیم و پتاسیم رنگ ماسه را متمایل به آبی می نماید .علاوه بر ترکیبات شیمیایی که خاصیت دیرگدازی ماسه را تحت تاثیر قرار میدهد مشخصات فیزیکی ماسه مانند اندازه ،پخش و شکل ذرات نیز باید مناسب باشد.
نگرشی به ماسه های کرومیتی و اولیونی ایران
کرومیت و اولوین در صنایع ریخته گری دارای مصارف متعدد و متنوع بوده و لذا ضرورت شناخت منابع آن در ایران و جایگزینی مواد بومی به جای منابع وارداتی وجود دارد.
موارد اصلی مصرف کرومیت و اولیوین در صنایع ریخته گری به قرار زیر است:
1.در ساخت جداره کوره ها-پاتیل ها و ابزارهای کمکی ذوب و استفاده از آنها به عنوان یک دیرگداز مناسب از منابع داخلی.
2.به عنوان یك ماسه مناسب ریخته گری در تولید.
• انواع فولادهای ریختگی بویژه فولادهای استنیتی منگنزی.
• قطعات بزرگ چدنی.
• استفاده از آنها به عنوان ماسه رویه در تولید سری قطعات چدنی(قالبگیری ماشینی و استفاده از ماسه تر) بویژه در قسمتهای فوقانی قطعات که تمایل به ماسه ریزی(ناشی از انبساط غیر پیوسته ماسه سیلیسی) دارند.
3.پودر کرومیت و اولیوین را می توان در تهیه بعضی از دوغاب های اولیه دیرگداز در ریخته گری دقیق استفاده کرد و ماسه های کرومیتی و اولوینی نیز می توانند به عنوان دیرگداز در پشت بند(بویژه در مورد قالبهای سرامیکی) مورد استفاده قرار گیرند.
منبع:
فتحی،محمدحسین:مواد قالبگیری برای ریختهگری فلزات،نشر اركان اصفهان.
مواد قالبگیری-قسمت سوم "افزودنیهای ماسه
مواد قالبگیری-افزودنیهای ماسه
علاوه بر سه جزء اصلی ماسه قالبگیری (ماسه، چسب، آب) مواد دیگری جهت ازدیاد کیفیت و برطرف کردن بعضی از عیوب خاص به مخلوط اضافه می گردند، چنین موادی بسیار زیاد هستند و لذا در اینجا به برخی از آنها که موارد استفاده زیادتری دارند اشاره می شود:
1.گرد زغال:
Fe2O3 تولید شده در مذاب تولیدات آهنی (چدن و فولاد و...) در اثر تماس با دیواره های قالب که اغلب از جنس سیلیس است وارد واکنش شده و تولید ترکیب زودگداز فایالیت را می دهد که منجر به سوختن ماسه و چسبیدن آنها به سطح قطعه ریختگی می شود(ماسه سوزی).
در اثر افزودن پودر ذغال سنگ یک محیط احیائی که ناشی از سوختن ذغال و خارج شدن گاز Co2 و هیدروژن و هیدروکاربیدهای سبک است، ایجاد می شود.در نتیجه این عمل،از اکسیداسیون سطوح مذاب و ایجاد گاز زود گداز فایالیت جلوگیری می شود. لذا در نهایت باعث نچسبیدن ماسه به قطعه و افزایش صافی سطوح قطعات ریختگی میگردد.
همچنین با افزودن این ماده از عیوبی نظیر انبساط حرارتی (ماسه اندازی)میتوان جلوگیری نمود. زیرا به وسیله منقبض شدن پودر ذغال در اثر حرارت می توان انبساط ماسه را در اثر گرما جبران نمود. نیز قابلیت خرد شدن ماسه را بهبود می بخشد زیرا ماسه کمتر کلوخه می شود و راحت تر روی shake out خرد می شود.
خواص یک پودر زغال مناسب به شرح زیر است:
الف)مواد فرار موجود در آن زیاد باشد(حدود 30-26 درصد).
ب)میزان خاکستر باقیمانده در زغال نباید از 10 درصد تجاوز کند.
ج)پارامتر مهم دیگر گوگرد موجود در زغال است، زِیرا گوگرد در چدنهای خاکستری تمایل به ایجاد chilled است و مقدار گوگرد باید از %1 تجاوز نکند.
میزان مصرف خاک زغال برای قطعات تا 1000 کیلوگرم 2 الی 4 درصد و برای قطعات سنگین که دارای گرمای بیشتری بوده عمق ماسهسوزی شدیدتر است میزان مصرف زغال تا 8 درصد نیز میرسد.
2.حبوبات، غلات(Cereals)
چسب غلهای مصرفی در ریختهگری عبارت است از پودر ذرات ریز و یا نشاسته ژلاتینی که از ذرات گرفته شده است. نشاسته را میتوان در ماسههای قالبگیری به منظور افزایش استحکام تر یا خشک یا بالا بودن قابلیت فروپاشی (Collapsibility) تا حد 2 درصد به کار گرفت. اگر مقدار نشاست در مخلوط زیاد شود خارجسازی قطعه از قالب دشوار خواهد شد. از آنجایی که نشاسته فرار است، استفاده غیر صحیح از آن میتواند باعث ایجاد عیوب گازی (Gas Defect) در قطعات شود.
3.گرد چوب(Wood Flour):
گرد چوب یا دیگر مواد سلولزی مثل گرد غله یا ذرت، پوسته حبوبات و سلولز را میتوان به مقدار 5/0 تا 2 درصد به ماسههای قالبگیری افزود. این میتوانند انبساط ماسه را کنترل کنند. مواد سلولزی پس از بالا رفتن دما مشتعل میشوند و بعد از سوختن فضای خالی ایجاد می کنند و از این طریق انبساط مخلوط ماسه قالبگیری کیترل می شود. گرد چوب و مواد سلولزی قابلیت پاشی وقابلیت جاری شدن (Flowability) را نیز اصلاح می کنند و به همین ذلیل سهولت بیشتری در خارج سازی قطعه از قالب ایجاد می کنند.
4.پودر سیلیس:
سیلیس سائیده شده و نرم که ریزتر از 200 مش باشد پودر سیلیس (Silica Flour) نامیده می شود. پودر سیلیس را می توان تا 35 درصد به منظور افزایش استحکام گرم ماسه به کار گرفت.پودر سیلیس چگالی توده (bulk-density)ماسه را افزایش می دهد و به همین دلیل ماسه قالبگیری به دلیل فشردگی بیشتر مقاومت بیشتری در برابر نفوذ فلز مذاب دارد.
5.اکسید آهن:
اکسید آهن ریز به مقدار اندک در برخی ماسه های قالبگیری به منظور افزایش استحکام گرم به کار می رود.
6.ملاس(molasses) ،دکسترین(dextrin).
ملاس ساقه نیشکر یا ملاس چغندر که تصفیه نشده و حاوی 60تا70 درصد شکر یا جامد باشد را میتوان برای افزایش استحکام خشک ماسه و بالا بردن سختی لبه قالب ها به کار گرفت.دکسترین یا صمغ نشاسته را می توان برای همان اهداف مورد استفاده قرار داد.
7.پرلیت:
پرلیت (perlite) یک سیلکات آلومینیم معدنی منبسط شده است.این ماده به مقدار کم و در حد 5/0تا5/1 درصد به منظور پایداری حرارتی (thermal stability) بهتر ماسه به کار می رود این ماده را ممکن است به عنوان عایق کننده تغذیه نیز مورد استفاده قرار داد.
8.آسفالت(asphilt)
یک محصول جنبی حاصل از تجزیه نفت خام است. آسفالت نیز همانند قیر به منظور افزایش استحکام گرم،بهبود سطح تمام شده قطعات ریخته گی آهنی مورد هستفاده قرار می گیرد.
9.قیر زمینی
قیر یک محصول از کک سازی است.طی عملیات کک سازی،قیر در دمای 5/3درجه سانتیگراد از ذغال جدا می شود.قیر تا حد 3 درصد و به منظور اصلاح استحکام گرم و بهبود سطح نهایی قطعات در مخلوط های ماسه برای ریخته گری قطعات آهنی به کار می رود.
10.گیلسونیت
گیلسونیت یک ماده آسفالتی جامد است که در برخی از نقاط زمین از معدن استخراج می شود. این ماده به خوبی فرار است و عملکرد آن شبیه تاثیر زغال در بهبود تمام شده قطعات است.
11.روغن سوخت
روغن سوخت برخی از اوقات به میزان بسیار کم و در حد 01/0 تا1/0 درصد در مخلوط قالبگیری به کار می رود به نظر می رسد که این ماده قابلیت قالبگیری ماسه را بهبود می بخشد.
منبع:فتحی،محمدحسین:مواد قالبگیری برای ریختهگری فلزات،نشر اركان اصفهان.
جوشكاری فلزات غیر آهنی ( یا فلزات رنگین)
جوشکاری فلزات غیر آهنی ( یا فلزات رنگین)
فلزات غیر آهنی یا فلزات رنگی به فلزاتی گفته می شود که فاقد آهن و یا آلیاژهای آن باشند مانند مس – برنج – برنز- آلومینیوم- منگنز- روی و سرب تمام فلزات رنگین را با کمی دقت و مهارت و آشنائی با اصول جوشکاری می توان جوش داد و برای جوشکاری این نوع فلزات بایستی خواص فلز را در نظر گرفت.
جوشکاری مس
با گاز بهترین طریقه برای جوشکاری مس جوشکاری با اکسیژن است( جوش اکسیژن = اتوگن= استیلن= کاربید اصطلاحات مختلف متداول می باشند) ضمناً می توان جوشکاری مس را با قوس الکتریک یا جوش برق نیز انجام داد. ورقه های مس را مانند ورقه های آهنی برای جوشکاری آماده می کنند یعنی سطح بالائی را تمیز نموده و از کثافات و روغن پاک نموده و در صورت لزوم سوهان می زنند. ولی چون خاصیت هدایت حرارت مس زیادتر است باید مقدار آمپر را قدری بیشتر گرفت. بهتر است همیشه با قطب مستقیم جوشکاری را انجام داد ( با جریان مستقیم و الکترود مثبت) زاویه الکترود نسبت به کار مانند جوشکاری فولاد است. طول قوس حداقل باید 10 تا 15 میلی متر باشد, برای جوشکاری مس می توان از الکترودهای ذغالی استفاده کرد. الکترودهای جوشکاری مس بیشتراز آلیاژ مس و قلع و فسفر ساخته شده اند و گاهی نیز از الکترودهای که دارای فسفر- برنز- سیلکان یا آلومینیوم هستند استفاده می کنند چون انبساط مس در اثر گرم شدن زیاد است فاصله درز جوش را در هر 30 سانتیمتر در حدود 2 تا 3 سانتیمتر زیادتر در نظر می گیرند. خمیر روانساز مس معمولاً در حرارت 700 تا 1000 درجه ذوب می شود و به صورت تفاله (گل جوش) سبکی روی کار قرار می گیرد و از تنه کار به علت کف کردن در روی کار نباید استفاده شود. بدون روانساز هم می توان مس را جوش داد و معمولاً از براکس استفاده می گردد. مس را به وسیله شعله خنثی جوش دهیم تا تولید اکسید مس نکند چون ضریب هدایت حرارت مس زیاد است باید *****ک جوشکاری مشعل 1 تا 2 نمره بیشتر از فولاد انتخاب شود. بهتر است مس را قبل از جوشکاری گرم نمائیم و با سیم جوشکاری مخصوص جوش داد برای جوشکاری صفحه 5 میلیمتری سیم جوش 4 میلیمتری کافی است و از وسط ورق شروع به جوشکاری می نمائیم و وقتی فلز هنوز گرم است روی آن چکش کاری می شود تا استحکام درز جوش زیاد شود.
جوشکاری سرب
در این نوع جوشکاری بیشتر از گاز هیدروژن و اکسیژن استفاده می گردد. در جوشکاری سرب احتیاج به گرد مخصوص نیست ولی باید قطعات کار را قبل از جوشکاری کاملاً صیقلی نموده سیم جوش سرب باید کاملاً خالص باشد چون سرب مذاب بسیار سیال می باشد. لذا جوشکاری درزهای قطعات سربی که به وضع قائم قراردارند بسیار دشوار و مستلزم مهارت و تجربه زیاد است.
جوشکاری چدن با برنج یا لحیم سخت برنج
چدن را می توان با برنج جوش داد. قطعات چدنی را باید همان طوری که برای جوشکاری با سیم جوش چدنی آماده می شوند برای برنج جوش آماده ساخت. لبه های درز جوش را باید به وسیله سوهان یا ماشین تراشید و هیچگاه لبه های درز قطعات چدنی را با سنگ سمباده پخ نزنید. زیرا ذرات گرافیت روی ذرات آهن مالیده می شوند و لحیم سخت خوب به چدن نمی چسبد. قطعات چدنی را قبل از شروع به جوش دادن حدود 210 تا 300 درجه سانتی گراد گرم کنید و گرد جوشکاری مخصوص چدن به کار برید تا بهتر به هم جوش بخورد.
نقطه ذوب سیمهای برنجی باید در حدود 930 درجه سانتی گراد باشد. سیمهای برنجی که برای جوش دادن قطعات چدنی به کار می روند دارای مقدار زیادی مس است و کمی نیکل نیز دارند . نیکل اتصال لحیم را به چدن آسان می کند و نقطه ذوب زیاد آن موجب سوختن گرافیت درز جوش می شود . در جوشکاری چدن با برنج از شعله ملایم *****ک بزرگ با فشار کم استفاده کنید. اگر فشار شعله زیاد باشد گرد جوشکاری از درز خارج می شود و در نتیجه قطعات چدنی خوب به هم جوش نمی خورند. قطعات چدنی را باید پس از جوشکاری در محفظه یا جعبه ای پر شن یا گرد آسپست قرار داد تا بتدریج خنک شود و سبب شکنندگی و ترک و سخت شدن چدن نگردد.
جوشکاری منگنز
از منگنز به صورت خالص استفاده نمی شود در جهت عکس از آلیاژهای ماگنزیوم استفاده می شود که برای ریختگی فشاری از آن استفاده می گردد . به جای آلیاژهای Mg. Mn و Mg. Al و Mg AlZn امروزه از آلیاژهای مخصوصاً محکم Zr و Th استفاده می شود. برای جوشکاری ماگنزیوم و آلیاژهای آن از همان شرایط جوشکاری آلومینیوم استفاده می گردد. قابلیت هدایت حرارت زیاد و انبساط سبب پیچش زیاد کار می شود. ماگنزیوم در درجه حرارت محیط به سختی قابل کار کردن است و در 250 درجه می توان به خوبی کار گرد.
جوشکاری برنج با گاز
برنج مهمترین آلیاژ مس است و از مس و روی و گاهی قلع و مقداری سرب تشکیل می شود، این فلز در مقابل زنگ زدگی و پوسیدگی مقاوم است. چون روی در حرارت نزدیک ذوب برنج تبخیر می گردد بنابراین جوشکاری با این فلز مشکل می باشد. برنج از 60 درصد مس و 40% روی و گاهی مقداری سرب تشکیل شده است. درموقع جوشکاری روی به علت بخار شدن و اکسید روی محل جوش را تیره کرده و عمل جوشکاری را مشکلتر می نماید. ضمناً گازهای حاصله خطرناک بوده و باید از محل کار تخلیه گردند. درموقع جوشکاری روی حرکت دست بسیار مهم است و باید حتی الامکان سرعت دست را زیاد کرده وگرده جوش کمتری ایجاد نمود تا فرصت زیادی برای تبخیر روی نباشد. برنج را می توان با الکترودهای گرافیتی و معمولی جوشکاری نمود، درجوشکاری برنج از قطب معکوس استفاده می شود. فاصله قوس الکتریکی باید حداقل 5 تا 6 میلیمتر باشد. برنج ساده تر از فولاد و چدن و مس جوش داده می شود و استحکام و قابلیت انبساط آن درمحل درز جوش بسیار خوب است. توجه شود چون انقباض و انبساط برنج زیاد است نمیتوان به وسیله چند نقطه جوش به هم وصل کرد بلکه بایستی به کمک بست هائی که در حین جوشکاری می توان آنها را به هم متصل نمود از پیچیدگی جلوگیری شود.
منبع:
http://www.mohandesan1ta.ir/
کاربردهای نانوتکنولوژی در کنترل خوردگی
روشهای کنترل خوردگی 6 روش میباشد:
طراحی، انتخاب مواد، پوشش، استفاده از بازدارنده، حفاظت کاتدی و آندی.
در دنیا بر روی نانوپوششها بسیار کار شده است و نانوپوششهای بسیاری گسترش پیدا کرده است. اما نفوذ نانوتکنولوژی در روشهای دیگر کنترل خوردگی بسیار ضعیف بوده است.
نانوپوششها
پوششهای نانوهیدروکسی آپاتید
برای ایمپلنتهای مورد استفاده در بدن انسان شرکت (InformatCorporation) IMCO با استفاده از تکنیک الکتروفورتیک در دمای محیط نانوساختار هیدروکسی آپاتید را بر روی انواع ایمپلنتها پوشش میدهد. این ایمپلنتها از جنس Ti6Al4V است که کاربردهای مختلف در دندانپزشکی و اورتوپدی دارد. پوشش هیدروکسی آپاتید به روشهای قدیمی پاشش حرارتی و رسوبدهی شیمیایی روی سطح اعمال میشد.
فواید استفاده از این پوششها
افزایش استحکام باند: در روشهای قبلی اعمال هیدروکسی آپاتید، استحکام چسبندگی پوشش بسیار پایین است. در روش پاشش حرارتی MPa30 و در رسوبدهی شیمیایی MPa 14 است. اما این روش باعث میشود که استحکام چسبندگی به حدود MPa60 برسد.
بهبود مقاومت خوردگی:
این پوششهای نانویی 100% فشرده و 100% کریستالی است، که باعث میشود مشکل انحلال آمورفی این پوشش حل شود و البته فشرده بودن باعث میشود که مایعات بدن تحت تماس با فلز قرار نگیرند. جریان پلاریزاسیون خوردگی در این حالت 300 بار کمتر از حالتی است که به دو روش قدیمی پاشش حرارتی و رسوبدهی شیمیایی پوشش داده شده است.
پوششهای چند لایهای نانویی برای مصارف نظامی و غیرنظامی
اخیراً پوششهایی گسترش پیدا کردند که دارای چندین لایه هستند که هر لایه در این پوشش هدف خاصی را دنبال میکنند. این پوششها با توجه به گزارشهایی که شده است دارای مصارف نظامی و غیرنظامی است. این پوششها هدفهای چندی را دنبال میکند که عبارتند از:
کاهش هزینه چرخه – عمر .
کاهش هزینه نگهداری تجهیزات .
کاهش آلودگیهای محیطی (پوششهای کروماته که آلودهکننده محیط زیست هستند).
این پوششها در چرخندهها، موتورها، سوئیچهای الکترونیکی و سنسورها کاربرد فراوان دارد. یکی از خصوصیات منحصر به فرد این پوشش این است که اگر لازم باشد براحتی از روی سطح برداشته میشود (زمانی که پوششها آسیب دیده و باید عوض شوند). همچنین در بین لایههای این پوشش از لایههای حسگر استفاده میشود که قادر است آسیبدیدگی مکانیکی و خوردگی را تشخیص دهد.
شرکت NANOMAG، پوششهایی از جنس نانو کامپوزیت که مقاوم در برابر خوردگی میباشد، تولید میکند که این پوششها جایگزین پوششهای پایه کروم خطرناک میشود که برای آلیاژهای منیزیم مخصوصاً برای احتیاجات صنایع خودروسازی، هوا – فضا و هوانوردی مناسب میباشد. کاهش وزن موتور وسایل نقلیه، یک شیوه اساسی برای کاهش مصرف سوخت آنها میباشد. با کم کردن 100 کیلوگرم از وزن، امکان ذخیره سوخت km100/51/0 فراهم میشود و بدین وسیله انتشار مواد نابودکننده محیط زیست کاهش مییابد. منیزیم که یک سوم از آلومینیوم و 80 درصد از فولاد سبکتر است به طور فزایندهای از زمان اولین حضورش در ماشینهای مسابقه در طول سالهای 1920، برای این هدف استفاده شده است. کاربردهای آلیاژهای پایه منیزیم هماکنون تا پوششهای دنده، لولههای چندشاخه ورودی، و پوششهای سرسیلندرها نیز امتداد پیدا کرده و حتی چرخها، بخشهای بدنه و قسمتهای اصلی فرمان را نیز در بر گرفته است. خواصی مانند قدرت بالا نسبت به وزن (در مقایسه با ضریب وزن) و ارتعاشگیری خوب (جذب ارتعاش) صدا و لرزش، با استفاده از تکنیکهای ریختهگری تحت فشار، تولید آسان قطعات را به همراه دارد و استفاده متداول و رایجی در بخشهایی مانند هوا – فضا و دستگاههای الکترونیکی قابل حمل میباشد.
از هدفهای رشد و توسعه پروژه NaNoMAG فراهم آوردن امکانی میباشد که از طریق آن روکشهای نانوکامپوزیتی (مرکب) که تمیز و سازگار با طبیعت هستند شکل گیرد که اقتصادیتر و مقرون به صرفهتر نیز خواهد بود. همچنین این پوششها مقاومتهای بهتری هم برای خوردگی و ساییدگی خواهند داشت.
برای ایجاد این پوششها از روشهای پلاسمایی رسوب شیمیایی بخار (PECVD)، پلاسمایی رسوب فیزیکی بخار (PEPVD) و همچنین تکنولوژی Sol-gel استفاده می شود.
پوششهای نانو با یونهای بازدارنده خوردگی
شرکت نامادیکس (Namadics) بر روی پوششهای کامپوزیتی فعالیت میکند که اثر حفاظت بسیار خوبی از خود نشان میدهد. این پوششها با استفاده از تکنیک Layer-by-Layer assembly یا electrostatic self assembly ساخته میشود. در این پوششهای نانوکامپوزیتی لایه لایه، یونهای بازدارنده خوردگی قرار داده میشود تا بتواند با نفوذ به سطح فلز پایه آنها را در برابر خوردگی محافظت کند و لایه انتهایی یک لایه سدکننده سیلیکاتی است. این پوششها نیز حفاظت خوردگی خوبی در مقایسه با پوششهای کروم نشان میدهد و میتواند جایگزین مناسبی برای آنها باشد(با توجه به اینکه پوشش¬های کروم به علت آلودگیهای زیست محیطی در حال انقراض هست).
پوششهای استثنایی آلیاژی با ساختار نانو مقاوم در برابر خوردگی
تحقیقات انستیتوی شیمی در کنار همکارانشان از انستیتوی Semicondactors (نیمه رساناها) باعث خلق و ابداع تعداد زیادی پوششهای جدید از آلیاژهای فلزی با ساختار نانو شدهاند که برای مقاومت در برابر خوردگی فوقالعاده بالایشان، مورد توجه قرار گرفتهاند. این پوششها از طریق پاشش مغناطیسی فلز شکل گرفتهاند. ساختار نانوکریستالهای این پوششها لایههای اثرناپذیر پایدار را به وجود می آورند که ویژگیهای ناقص و معیوب پوششهای قدیمی را ندارند. مشاهده شده است که پوششها با ساختار نانوکریستال، نسبت به پوشش ها دارای ساختار بیشکل مقاومت بالایی در برابر خوردگی دارند. پاشش مغناطیسی فلز، این امکان را فراهم میآورد که آلیاژهایی از فلزات را که با استفاده از روش های قدیمی قابل تولید نبودند، به وجود آورد، مانند وقتی که نقطه ذوب یک فلز بالاتر از درجه جوش دیگری میباشد. اخیراً خواصی از آلیاژهای زیر مطالعه شدهاند:
Al-Mg-Cu, Cr-Cr-Mo, Au-Pd-In, Fe-Cr–Ni-Ta, Ni-Cr-Mo
انتخاب مواد
فولاد ضدزنگ با مقاومت خوردگی فوقالعاده بالا
فولادهای ضدزنگ کاربردهای مختلفی میتواند داشته باشد، مشکل اصلی این آلیاژ استحکام پایین آن است که مصرف آن را در کاربردهای مقابله با خوردگی کاهش میدهد. شرکت Sandvik با استفاده از تکنولوژی نانو و با اضافه کردن نانو ذرات در مرحله ذوب توانسته آلیاژهای فولاد ضدزنگ با مقاومت خوردگی بالا، انعطافپذیری مناسب قبل از عملیات حرارتی و استحکام بالا بعد از عملیات حرارتی تولید کند. با استفاده از این تکنولوژی میتوان فولاد ضدزنگ را جایگزین آلومینیوم کرد. با این آلیاژ قادریم با هزینه کمتر همان استحکام و وزن را بدست آوریم. کاربردهای قابل تصور برای این آلیاژ در شاسی (بدنه ماشین) سبک وزن، ابزار ورزشی و تجهیزات پزشکی است.
دیگر حوزه ها
در دنیا بر روی حوزههای حفاظت کاتدی، آندی و ممانعت کننده کار قابل ملاحظهای انجام نشده است. برروی آندهای فدا برای پیشرفت در این حوزهها نیازمند ایدهپردازی و تشکیل جلساتی با حضور متخصصین خوردگی و نانوتکنولوژی میباشد. به عنوان مثال می توان برروی آندهای فداشونده تکنولوژی نانو را اعمال کرد(در دانشگاه تهران در پروژه ای در این راستا تعریف شده است) تا بتوان بازده جریان این آندها را افزایش داد.
منبع :شبكه تحلیلگران تكنولوژی ایران (حسین توكلی)
روش طراحی قالبهای فورج با كامپیوتر( CAD-CAM)
طراحی قالبهای فورج با استفاده از نرم افزارها و كامپیوتر ، صنعت قالبسازی را دچار تحولهای جدیدی نموده است و استفاده از كاربردهای تكنولوژیكی این پروسه یكی از كوتاهترین و با صرفه ترین روشهای طراحی قطعات صنعتی و قالبهای صنعتی میباشد .
در طول دهه گذشته از كامپیوترها به شكل گسترده ای برای كارهای پتك كاری و طراحی قالبهای فورجینگ استفاده شده است .
پیشرفتهای اولیه در عملیات تراشكاری كنترل شده عددی یا NC در ساخت قالبهای پتك كاری ( فورجینگ ) متمركز شده است . در اواسط دهه 1970 نقشه كشی به كمك كامپیوتر و تراشكاری NC برای پتك كاری قطعات صنعتی مانند تیغه های توربین معرفی شد . در اوایل دهه 1980 در كشورهای پیشرفته صنعتی بعضی كمپانی ها استفاده از سیستمهای CAD-CAM كه به طور معمول برای طراحی مكانیكی نقشه كشی و تراشكاری NC از آن استفاده می نمودند را برای طراحی و ساخت قالبهای فورج به صورت بهینه تكنولوژیكی مورد استفاده قرار دادند .
سیستمهای CAD-CAM از نظر عملیات تجاری و قابل دسترس بودن و كیفیت های بروز داده دارای جنبه های اقتصادی مفید میباشند .
1- CAD-CAM تشكیل شده از یك میكروكامپیوتر یا مینی كامپیوتر یك ترمینال نمایش گرافیكی ، یك صفحه كلید و یك پردازشگر رقمی با قسمت مربوط به ورود اطلاعات و یك ماشین اتوماتیك نقشه كشی و سخت افزاری برای ذخیره اطلاعات و نوار NC پانچ یا فلاپی دیسك است از نظر پیشرفتهای علمی و تكنولوژیكی جدید این سیستمها می توانند در سطوح مختلف اتوماسیون مفید واقع شوند و قادر هستند عملیات پتك كاری (فورجینگ) را به صورت سه بعدی نمایش داده و امكان زوم كردن و ودوران نمایشی هندسی عملیات فورج را بر روی صفحه ترمینال گرافیكی به منظور بررسی دقیق مهندسی فراهم سازند این سیستمها میتوانند عملیات پتك كاری داده شده را از هم مجاز كنند یعنی مقاطع عرضی پتك كاری مورد نظر را تشریح ،ترسیم و نمایش دهند كه آن كار برای تحلیل فشارهای قالب و جریان فلز صورت میگیرد .بنابراین برای سهولت تاثیر متقابل بین طراح و سیستم كامپیوتری میتوان نتایج را نمایش داد و محاسبات مهندسی را روی آنها انجام داد و تغییرات اعمال شده در طراحی قالب میتواند به سهولت انجام گرفته و در صورت لزوم طرحهای جدیدتر جایگزین آن شود و مورد بررسی و تحلیل قرار گیرد .
امروزه در كشورهای صنعتی پیشرفته این امر بعنوان یك اصل بسیار مهم و با بكار گیری جدیدترین متدهای علمی و كامپیوترها انجام میگیرد .مزیت نهایی طراحی قالبهای فورج به كمك كامپیوتر وقتی معلوم میشود كه نرم افزار كامپیوتری به صورت ارزان و دقیق در دسترس مهندسین و طراحان باشد و بتوانند برای شبیه سازی جریان فلزی در طول عملیات پتك كاری فورجینگ مورد استفاده قرار گیرد . در این مورد آزمایشات عملیات ماشینكاری و اهنگری میتواند به شكل شبیه سازی نهایی ، پتك كاری بر روی كامپیوتر انجام شود كه ناشی از طرح بلوكر فرضی یا انتخابی باشد و نتایج میتواند روی ترمینال گرافیكی نمایش داده شود اگر طرح شبیه سازی به این نكته اشاره كند كه طرح بلوكر انتخاب شده قالب فینیشر را پر نمیكند یا مقدار زیادی از مواد هدر میرود یك طرح بلوكر جدید انتخاب میشود و شبیه سازی كامپیوتری و آزمایشها مجدداٌ تكرار میشود تا به نتایج مثبت برسد . نكته مهمی كه حائز اهمیت میباشد این است كه این پروسه شبیه سازی و طراحی به كمك كامپیوتر تعداد دفعات آزمایشهای پرهزینه و گران قیمت قالبهای فورج را كه باید انجام گیرد كاهش میدهد كه این مسئله باید مورد توجه مهندسین و طراحان قالب قرار گیرد .
از سیستمهای CAD در طراحی قالبهای فروج استفاده بهینه میشود . سیستم كلی CAD-CAM از یك كامپیوتر با كاربردهای پردازشی و ذخیره ای و بازیابی تصویری شكلهای گرافیكی بوجود آمده است كه برای اپراتورسیستم امكان انجام عملیات طراحی قالب با كامپیوتر را فراهم می كند .
كاربردهای تكنولوژیكی سیستمهای CAD-CAM به سه گروه اصلی طبقه بندی میشوند كه عبارتند از :
1- انجام طراحی قطعات صنعتی و قالبهای صنعتی و ماشین آلات و غیره .
2- انجام محاسبات و تجزیه و تحلیل
3- تولید
استفاده از سیستمهای CAD-CAM در طراحی و ساخت قالبهای فورج مزایای فراوانی بدنبال داردو از كامپیوتر میتوان برای تجزیه و تحلیل عوامل شكست در قالبهای فورج استفاده كرد یا در طراحی قالب با استفاده از قابلیتهای كامپیوتری میتوان براحتی فرمهای نرو مادگی در بلوكهای قالب فورج را طراحی كرد و در هم جفت نمود و حتی این كار را با تلرانسهای بسیار كم انجام داد و قطعات نروماده قالب را در هم درگیر كرد .تلرانسهای لازم را به انها داد و كل قالب را مورد بررسی و تحلیل قرار داد و یا در مواردی كه در قالب دو قطعه باید دقیقاٌ با هم میزان و جفت شوند ، كامپیوتر میتوانداین كار را به اسانی انجام دهد و ابعاد دقیق را مشخص كند و با دادن برنامه به ماشین ابزار CNC یا NC عملیات ماشینكاری دقیق قالب انجام میگیرد .
در طراحی و ساخت مدلهای الكترود اسپارك برای عملیات اسپارك اورژن قالبهای فورج میتوان از كامپیوتر نهایت استفاده را كرد و مدلهای مسی با فرمهای فوق العاده پیچیده و شكلهای غیر هندسی را طراحی كرد و ابعاد آن را مشخص نمود و با استفاده از عملیان ماشینكاری NC یا CNC مدلهای الكترود اسپارك را ماشینكاری كرد .
از سیستمهای پیشرفته مجتمع CAD-CAM میتوان برای كنترل و برنامه ریزی های وسیعتر در پروسه طراحی و تولید صنعتی استفاده كرد كه باعث افزایش كیفیت محصولات تولیدی و تیراژ بالا در تولید انبوه و برنامه ریزی های اقتصادی در تولید میشود .
منبع:http://www.moldmaker.blogfa.com/post-116.aspx
خواص مكانیكی(تعریف مفاهیم اولیه)
تنش، كشش و قابلیت الاستیكی Stress, Strain, and Elasticityخواص میكانیكی فلزات شامل عكس العمل های الاستیكی فلزات بواسطه ی اعمال نیرو یا ارتباط بین تنش و تغییر طول نسبی آنان می باشد.
قبل از این كه به بحث خواص مكانیكی بپردازیم، سه اصطلاح را كه برای درك دانشجو مهم هستند تعریف می كنیم این اصطلاحات عبارتند زا: تغییر طول نسبی والاستیسیته، اگر چه مردم تنش و تغییر طول نسبی را به جای یكدیگر بكار می برند، ولی حقیقت این است كه دو كمیت را كاملاً با یكدیگر متفاوتند.
تنش
تنش مقدار نیروئی است كه بر واحد سطح وارد می شود و بر حسب پوند بر اینچ مربعی اندازه گیری می گردد.
تنشی كه باعث می شود تا جسم كشیده شود به تنش كششی موسوم است. تنشی كه موجب كوتاهتر شدن طول جسم می شود، به تنش فشاری و تنشی كه جسم را به لایه های متناوب تقسیم می كند، به تنش برشی مشهور می باشد. نیروهای خمشی و نیروهای پیچشی تنشهائی ایجاد می كنند كه تركیبی از سه تنش فوق می باشد.
كشش (تغییر بعد)
تغییر طول نسبی، مقدار درصد تغییراتی است كه در واحد طول به هنگام ازدیاد یا كاهش طول نمونه رخ می دهد و اندازه ی تغییر شكل حاصل از اثر نیرو را نشان می دهد.
الاستیسیته (قابلیت ارتجاعی)
الاستیسیته در سال 1678 بوسیله رابرت هوك دانشمند معروف انگلیسی بر اساس آزمایشهائی بصورت یك تئوری بیان گردید. امروزه این تئوری به قانون هوك معروف است. این قانون را بدین صورت می توان بیان كرد: مقداری كه یك جسم الاستیك خم و یا كشیده می شود. ازدیاد طول جسم (تغییر طول نسبی) با نیروی وارد بر آن (تنش) نسبت مستقیم دارد. بعداً دریافتند كه این قانون فقط در حدود مشخص از تنشها صادق است. بالاتر از این تنش نقطه ای وجود دارد كه حد الاستیك موسوم است. اگر میزان بار از این نقطه تجاوز كند جسم به طور دائم تغییر شكل می دهد. در حقیقت حتی بارهای كم نیز كاملاً اسلاستیك نیستند لذا بایستی از یك روش دلخواه برای تعیین حد الاستیك تجارتی استفاده كرد.
استحكام (تاو) Strength
استحكام همواره با قابلیت پلاستیكی شاید مهمترین تركیب خواص یك فلز باشد. استحكام عبارتست از مقاومت جسم در برابر تغییر شكل ولی قابلیت پلاستیكی به قابلیت تغییر شكل جسم بدون آنكه بشكند گفته می شود. برای این كه كاملاً به ویژگی های استحكام فلز واقف باشیم، بایستی تعدادی از انواع استحكام یك فلز را بشناسیم. از انواع استحكام
می توان مقاومت كششی، مقاومت فشاری، مقاومت خستگی و مقاومت تسلیم (روانی) را نام برد.
استحكام كششی (تاوكششی)Tensie strength
مقاومت كششی بیشترین نیروی كششی است كه جسم قبل از شكست تحمل خواهد كرد. این مقدارمعمولاً برای استحكام یك ماده داده می شود و واحد آن بر حسب پوند بر اینچ مربعن بیان می شود. مقاومت كششی ماده را می توان با آلیاژی كاری، سردكاری، و گاهی اوقات بوسیبله ی عملیات حرارتی، افزایش داد.
استحكام تراكمی (مقاومت فشاری) Compressive strength
مقاومت فشاری، بیشتریین فشاری است كه یك ماده قبل از مقدار فشار تعیین شده جهت تغییر شكل تحمل می كند. مقاومت های فشاری چدن و بتون بزرگتر از مقاومت های كششی شان هستند در صورتی برای اكثر مواد، این موضوع كاملاً برعكس است.
مقاومت (تاو) خستگی Fatigue strength
مقاومت خستگی بیشترین باری است كه یك جسم می تواند بدون شكست در برابر ضربه های متعدد برگشت بار تحمل كند. مثلاً یك میله ی چرخان كه وزنه ای را نگهداری می كند، نیروهای كششی روی قسمت بالائی میله و نیروهای فشاری روی قسمت پائینی¬اش وارد می شوند.
وقتی میله می چرخد، تنش های كششی و فشاری بطور متناوب تغییر می كنند. از مقاومت خستگی در طرح بالهای هواپیما و سایر قطعات اسكلتی كه در معرض بارهای نوسانی قرار دارند، استفاده می كنند مقاومت خستگی به عواملی نظیر ساختمان میكروسكپی، حالت سطحی، محیط خورنده، كار سرد و غیره بستگی دارد.
استحكامل تسلیم (مقاومت روانی) Yield strength
مقاومت تسلیم حداكثر باری است ماده تغییر فرم معینی را از خود بروز می دهد. اكثر محاسبات مهندسی ساختمانها براساس مقادیر مقاومت تسلیم استوارند تا مقادیر مقاومت كششی. استحكام یك فلز به ساختمان داخلی آن، تركیب، عملیات حرارتی و درجه ی كار سرد مربوط می شود.
سختی Hardness
سختی خاصیت اصلی یك ماده نیست ولی به خواص الاستیك و پلاستیك آن مربوط
می شود. بطور كلی، سختی جسم عبارتست از مقاومت به نفوذ آن. هر چه سختی بیشتر باشد مقاومت نفوذ نیز بیشتر می شود. این آزمایش سختی به سبب سادگی آن و نیز به این علت كه چون می توان آن را به سهولت به مقاومت كششی و تسلیم فولادها ارتباط داد كاربرد وسیعی پیدا كرده است. آزمایشهای سختی خراشی و یا سایشی گاهی اوقات برای موارد بخصوصی مانند آزمایش های سختی الاستیكی و یا ارتجاعی بكار می روند.
سفتی (چقرمگی) Toughness
اگرچه روش مستقیم و صحیحی برای اندازه گیری سفتی فلزات وجود ندارد، ولی سفتی هر دو خاصیت قابلیت كشش (قابلیت مفتول شدن) و استحكام را در بر دارد و می توان تعریف كرد كه سفتی عبارتست از قابلیت یك فلز به جذب انرژی بدن آنكه بشكند.
سفتی را می توان بصورت سطح زیر منحنی تنش- تغییر طول نسبی بیان كرد. غالباً مقاومت به ضربه ای یك ماده را بعنوان نشانه ای از سفتی آن بحساب می آورند.
قابلیت پلاستیكیPlasticity
یكی از خواص بسیار مهم فلزات پلاستیكی آنها است. قابلیت پلاستیكی عبارتست از قابلیت تغییر شكل بسیار زیاد یك فلز بدون آنكه بكشند.
قابلیت مفتول شدن یا انعطاف پذیری Ductility
قابلیت مفتول شدن عبارتست از قابلیت پلاستیكی كه بوسیله ی یك ماده تحت نیروی كششی نمایش داده می شود. این خاصیت را با مقداری كه ماده می تواند بطور دائم ازدیاد طول پیدا كند، اندازه گیری می كنند. این قابلیت به ازدیاد طول موجب می شود تا بتوان یك فلز را از یك اندازه ی بزرگتر بصورت یك سیم با اندازه ی كوچكتر كشید. مس و آلومینیم قابلیت كشش زیادی دارند.
قابلیت چكشخواری (چكش كاری) Malleability
قابلیت چكش كاری كه شكل دیگری از قابلیت پلاستیكی است به قابلیت تغییر شكل دائم یك فلز تحت نیروی فشاری بدون آنكه گسیخته شود، گفته می شود. بخاط همین خاصیت است كه می توان فلزات را به صورت ورقهای نازك چكش كاری و نورد كرد. طلا، نقره، قلع و سرب از جمله فلزاتی هستند كه قابلیت چكش خواری بالائی از خود نشان می دهند. طلا قابلیت چكشخواری استثنائی دارد و می تواند بصورت ورقهای نازكی كه برای عبور نور كافی است نورد شود.
شكنندگی Brittleness
شكنندگی خاصیتی است كه بر عكس قابلیت پلاستیكی می باشد یك فلز شكننده فلزی است كه نمی تواند بنحو قابل ملاحظه ای تغییر شكل دادئم بدهد، بعبارت دیگر، فاقد قابلیت پلاستیكی است. فلزات شكننده، مانند فولاد كاملاً سخت شده، ممكن است قابلیت پلاستیكی بسیار اندكی را از خود نشان دهند، لذا می توان آنها را جزو گروه فلزات شكننده بحساب آورد، با وجود این سختی مقیاسی از قابلیت پلاستیكی نیست. فلزات شكننده مقاومت به برخورد یا ضربه ی بسیار كمی دارند و بدون هیچگونه اخطار و علائم قبلی
می شكنند.
ضریب انبساط خطی گرمایی Expansion Coefficient of Linear Thermal
خواص فیزیكی فلزات خامی هستند كه به ساختمان اتم بستگی دارند و عبارتند از: وزن مخصوص، قابلیت هدایت الكتریكی و گرمائی، ذوب، قابلیت مغناطیسی، قابلیت انعكاس و ضریب انبساط خطی.
به استثناء بعضی موارد، جامدات وقتی گرم می شوند، انبساط و وقتی سرد می شود انقباض حاص می كنند. جامدات نه تنها از لحاظ طول بلكه از لحاظ عرض و ضخامت نیز افزایش می یابند. هر گاه یك جامد را یك درجه گرم كنیم میزان افزایش واحد طول را ضریب انبساط خطی آن می گویند.
وزن مخصوص Specific Gravity
بعضی مواقع لازم است كه زون مخصوص یك فلز را با فلز دیگر مقایسه كنیم. برای این منظور، به یك استاندارد احیتاج داریم. آب استانداردی است كه فیزیكدانها برای مقایسه وزن مخصوص های جامدات و مایعات انتخاب كرده اند. بنابراین وزن یك ماده نسبت به وزن حجم مساوی از آب دانسیته ی مخصوص یا چگالی آن نامیده می شود.
نقطه ذوب Melting Point
نقطه ی ذوب درجه حرارتی است كه یك ماده از حالت جامد به حالت مایع تبدیل
می شود. برای یخ، این نقطه 32 درجه ی فار نهایت است. موارد خالص نقطه ی مشخص دارند یعنی آنها از حالت جامد به حالت مایع، بدون تغییر درجه ی حرارت تبدیل می شوند، به هنگام ذوب مقداری گرما جذب و به هنگام انجماد مقداری گرما آزاد می كنند.
وقتی ماده تغییر حالت می دهد، جذب یا آزادی گرما به گرمای نهان آن معروف است.
تبدیل از یك مقیاس درجه حرارت به مقیاس دیگر بوسیله ی رابطه ی زیر امكان پذیر است.
قابلیت رسانایی الكتریكی و گرمایی Electrical and Thermal Conductivity
قابلیت یك فلز به سهولت هدایت الكتریسیته و گرما یكی از خصوصیات بارز آن محسوب می شود.
مقاومت به جریان برق از درون یك سیم به مقاومت آن سیم معروف است.
بایستی در نظر داشت كه چندین عامل وجود دارند كه می توانند مقاومت فلزات را اصلاح كنند. برخی از آنها عبارتند از:
1-مقاومت فلزات نسبت به جریان الكتریكی و گرمائی با درجه ی حرارت زیاد
می شود.
2-مقاومت به جریان الكتریكی با ناخالصی ها و آلیاژ كردن افزایش می یابد.
3-سردكاری (تعییر شكل) فلز مقاومت الكتریكی را زیاد می كند.
4- رسوب از محلول جامد به هنگام عمل پیر سختی مقاومت الكتریكی را زیاد می كند.
5- فلزات یك ظرفیتی (مس، نقره، طلا) و فلزات قلیائی (لیتیم، سدیم، پتاسیم، روبیدیوم، سزیم) دارای مقاومت پائین و فلزات قلیایی خاكی دو ظرفیتی (بریلیوم، منیزیم، كلسیم، باریم، رادیم) دارای مقاومت بالاتر و فلزات انتقالی (واسطه)، (نظیر كبالت، نیكل، رادیوم، روبیدیم، سرب، اوسمیوم، اریدیوم و پلاتین) مقاومت بالائی دارند.
هنگام عبور جریان از داخل یك هادی، مقاومت موجب آزاد شدن گرما می شود و هر چه مقاومت بزرگتر باشد، حرارت بیشتری به ازای عبور یك جریان معین آزاد می گردد. برای گرم كردن الكتریكی به فلزات با مقاومت الكتریكی بالا مانند آلیاژهای نیكل و كروم نیاز داریم. یك هادی خوب حرارت، مانند مس، اغلب برای مبدل های گرمائی، سیم پیچیهای گرم كننده و آهن های لحیم كاری مصرف می شود. ظروف آشپزخانه را معمولاً از آلومینیم می سازند زیرا هدهایت گرمایی زیاد داشته و در مقابل خوردگی ناشی از مواد غذایی مقاومت می كند.
حساسیت مغناطیسی Magnetic Susceptibility
هر گاه جسمی را در میدان مغناطیسی قرار دهیم، نیرویی بر روی آن اعمال می شود. در این حالت می گویند كه جسم مغناطیسی می شود. شدت مغناطیسی شدن به حساسیت K بستگی دارد و آن خاصیتی از فلز است كه به جنس ماده وابسته می باشد. اكثراً مقدار K یك فلز با فلز دیگر فرق می كند و بر حسب علامت و مقدار K آنرا به سه دسته تقسیم
می كنند:
فلزات دیامانیتیك (دی مغناطیس):
فلزهای دیامانیتیك، فلزهائی هستند كه در آنها K كوچك و منفی است بنابراین بوسیله ی یك مغناطیسی خیل ضعیف دفع می شود. نمونه هائی از این فلز عبارتند از: مس، نقره، طلا و بیسموت.
فلزهای پارامانیتیك (فلزهای پارامغناطیس):
فلزهای پارامغناطیس، فلزهائی هستند كه در آنها K كوچك و مثبت است. اكثر فلزها پارامغناطیس هستند كه از آن جمله می تونان لیتیم، سدیم، پتاسیم، كلسیم، استرنسیم، منیزیم، مولیبدن، و تانتالم را نام برد.
فلزهای فرومانیتیك (فرومغناطیس):
فلزهای فرومغناطیس، فلزهائی هستند كه در آنها K بزرگ و مثبت است و شامل آهن، كبالت، نیكل و گادولینیم می شوند. یكی از خصوصیات ویژه ی مواد فرومغناطیس این است كه بعد از آنكه میدان مغناطیسی برطرف شد، خاصیت مغناطیسی شان را حفظ
می كنند، لذا این مواد قابلیت مغناطیسی دائم شدن را دارند.
قابلیت بازتابش Reflectivity
یكی زا خصوصیات برجسته ی فلز، جلای فلزی آن است. این رنگ سطحی ظاهراً به سبب انعكاس خاص نوری است كه به سطح آزاد فلز تابیده شده است. قابلیت انعكاس (نسبت نور منعكس شده به نور تابیده شده) یك سطح فلز نه فقط به نوع ماده بلكه به خشنی و صافی آن نیز بستگی دارد.
قابلیت مقاومت اكسیداسیون عالی و خصوصیات ویژه ی انعكاس گرمائی آلومینیم و فولادهای باروكش آلومینیم، آنها را برای مصارفی نظیر آسترهای اجاق، بازتابنده حرارتی و المنت های حرارتی مطلوب ساخته اند.
منبع:
http://www.mohandesan1ta.ir/
خوردگی
هزینه های خوردگی
تخمین هزینه های سالانة خوردگی در ایالات متحده بین 8 بیلیون دلار تا 126 بیلیون دلار می باشد. بهر ترتیب، خوردگی زیان اقتصا دی عظیمی است و برای كاهش دادن به كارهای زیادی می توان انجام داد. اگر این نكات را در نظر بگیریم كه هر جا فلز و مواد دیگر مورد استفاده قرار می گیرند خوردگی با درجه وشدتهای متفاوتی واقع می گردد، این رقمهای بزرگ دلاری چندان غیر منتظره نخواهد بود.
در حقیقت اگر خوردگی وجود نداشت اقتصاد جامعة ما بشدت تغییر می كرد. مثلاً اتومبیلها، كشتیها، خطوط لوله زیر زمینی و وسایل خانگی احتیاج به پوشش نداشتند، صنایع فولاد زنگ نزن از بین می رفتند و مس فقط برای مقاصد الكتریكی بكار می رفت. اكثر كارخانجات و محصولاتی كه از فلز ساخته می شدند از فولاد یا چدن ساخته میشدند.
اگر چه خوردگی اجتناب ناپذیر است، ولی هزینة آنرا به مقدار زیادی میتوان كاهش داد. مثلاً یك آند ارزان قیمت منیزیم می تواند عمر تانك آب گرم خانگی را دو برابر كند. شستشوی اتومبیل برای زدودن نمكهای كه برای یخ بندان روی جاده می پاشند مفید است. انتخاب صحیح مواد و طراحی خوب، هزینه های خوردگی را كاهش میدهد. یك برنامه صحیح تعمیرات و نگهداری رنگ چندین برابر مخارجش را صرفه جویی میكند. اینجاست كه مهندسی خوردگی وارد صحنه می شود و می تواند موثر باشد – ماموریت اصلی او مبارزه با خوردگی است. جدا از مخارج مستقیم دلاری، خوردگی یك مشكل جدی است زیرا به طور روشنی باعث تمام شدن منابع طبیعی ما می گردد. مثلاً فولاد از سنگ آهن بدست می آید، میزان تولید داخلی سنگ آهن پر عیاركه مستقیماً قابل استفاده باشند بشدت كاهش یافته است. توسعة صنعتی سریع بسیاری از كشورها نشان می دهد كه رقابت و قیمت منابع فلزی افزایش خواهد یافت. ایالات متحده دیگر مصرف كنندة اصلی منابع معدنی نیست.
مهندسی خوردگی
مهندسی خوردگی كاربر دانش وفن یا هنر جلوگیری یاكنترل خسارت ناشی از خوردگی به روش اقتصادی و مطمئن میباشد. برای اینكه مهندس خوردگی به خوبی از عهده وظایف خود برآید، بایستی با اصول خوردگی و عملیات مبارزه با آن، خواص شیمیایی، متالورژیكی، فیزیكی و مكانیكی مواد، آزمایشات خوردگی، ماهیت محیط های خورنده، قیمت مواد اولیه، نحوه ساخت و تولید كامپیوتر و طراحی قطعات آشنا باشد. او همچنین بایستی خصوصیات معمول یك مهندس كه عبارت است از : توانائی ارتباط برقرار كردن با دیگران، صداقتتوانایی تفكر و تجزیه تحلیل كردن، آگاهی عمیق از اهمیت خطرات در عمل، عقل سلیم یا شعور، منظم و مرتب بودن، و مهمتر از همه احساس عمیق و صحیح مسائل اقتصادی را دارا باشد. در حل مسائل خوردگی بایستی روشی را انتخاب نماید كه بیشترین بهره را داشته باشد.
مقالات زیر كاربردهای تكنولوژی كامپیوتر در مهندسی خوردگی را نشان می دهد:
ماشینهای متفكر(هوش مصنوعی) در ژورنال مهندسی شیمی، سپتامبر 1981، صفحات 45-51 به بررسی مثالهای متعدد در مورد پیش بینی خوردگی توام با تنش پرداخته است. همچنین از دیگر كاربرهای تكنولوژی كامپیوتر در خوردگی می توان به مقالات زیر اشاره كرد.
S.N. Smith and F.E. Rizzo, Computer Assisted Corrosion
Engineering, Materials Performans, 19:21 – 23(oct 1980)
C. Edeleanu, the Efect of the Microprissors on Corrosion
Technology, Materials Performance, 22:82 – 83 (Oct 1983)
در گذشته تعداد نسبتاًكمی از مهندسین با آموزش رسمی در خوردگی وجود داشتند. اكثراً افرادی دركه این رشته كار می كردند دارای زمینه های شیمی، برق یا متالوژی بودند. خوشبختانه این وضعیت امروزه تغییر كرده است.
از فقط 3 دانشگاه در 1946، امروزه 65 دانشگاه در ایالات متحده دروس رسمی در زمینه خوردگی ارائه می كنند. مفهوم اینها آن است كه امروزه صدها مهندس در صحنه وجود دارند كه درس رسمی در این زمینة خوردگی گذرانده اند. در گذشته، و حتی امروزه، خوردگی را به عنوان "معضلی" كه بایستی آنرا تحمل كرد در نظر می گیرند. غفلت علت بسیاری از انهدام های زودرس، غیر منتظره و گران می باشد- غفلت بوسیلة افرادی كه بایستی اطلاعات بهتری داشته باشند. بطور مثال، دو فروشندة آنده های قربانی شونده، سیستم های خود راحفاظت آندی می نامند! در حقیقت این سیستم حفاظت كاتدی است كه كاملاً متفاوت است.
تعریف خوردگی
خوردگی را تخریب یا فاسد شدن یك ماده در اثر واكنش با محیطی كه در آن قرار دارد تعریف می كنند. بعضی ها اصرار دارند كه این تعریف بایستی محدود به فلزات باشد، ولی غالباً مهندس خوردگی بایستی برای حل یك مسئله هم فلزات و هم غیر فلزات را در نظر بگیرد. سرامیكها، پلاستیكها، لاستیك و مواد غیر فلزی دیگر نیز منظور شده اند. مثلاً، تخریب رنگ ولاستیك بوسیله نور وخورشید یا مواد شیمیایی، خورده شدن جدارة كورة فولاد سازی، و خورده شدن یك فلز جامد بوسیله مذاب یك فلز دیگر تماماً خوردگی نامیده می شوند. خوردگی می تواند سریع یاكندصورت گیرد. فولاد زنگ نزدن در حالت حساس شده به وسیله اسید پلی تیونیك ظرف چند ساعت بشدت خورده می شود. ریلهای راه آهن معمولاً به آهستگی زنگ می زنند- ولی سرعت زنگ زدن آنقدر نیست كه بر كارایی آنها در سالهای زیاد اثری بگذارد. ستون آهنی معروف دهلی در هندوستان حدود 2000 سال پیش ساخته شده و هنوز به خوبی روز اول است. ارتفاع آن 32 فوت است.
لكن بایستی توجه شود كه این ستون آهنی عموماً در شرایط جوی خشك قرار داشته است. خوردگی فلزات را می توان بر عكس متالوژی استخراجی در نظر گرفت. در متالوژی استخراجی در نظر گرفت. در متالوژی استخراجی، هدف عمدتاً بدست آوردن فلزاز سنگ معدن و تصفیه یا آلیاژسازی آن برای مصارف مختلف می باشد. اكثر سنگ معدنهای آهن حاوی اكسید های آهن هستند و زنگ زدن فولاد به وسیله آب واكسیژن منجر به تشكیل اكسید آهن هیدارته می گردد. اگرچه اكثر فلزات موقعی كه خورده میشوند تشكیل اكسیدهایشان را می دهند ولی لغت زنگ زدن فقط در مورد آهن و فولاد بكار می رود. بنابراین میگوئیم فلزات غیر آهنی خورده می شوند و نمی گوییم زنگ می زنند. محیطهای خورنده عملاً كلیه محیطها خورنده هستند، لكن قدرت خوردگی آنها متفاوت است. مثالهایی در این مورد عبارتند : از هوا و رطوبت، آبهای تازه، مقطر، نمكدار، و معدنی، آتمسفرهای روستائی، شهری، و صنعتی، بخار و گازهای دیگر مثل كلر، آكونیاك، سولفور هیدروژن، دی اكسیدگوگرد، و گازهای سوختنی، اسید های معدنی مثل اسید كلریدریك، سولفوریك، و نیتریك، اسیدهای آلی مثل اسید نفتنیك، استیك، و فرمیك، قلیائی ها، خاكها، حلالها، روغن نباتی و نفتی، و انواع و اقسام محصولات غذائی. بطور كلی مواد "معدنی" خورنده تر از مواد " آلی" می باشند. مثلاً خوردگی در صنایع نفت بیشتر در اثر كلرور سدیم، گوگرد، اسید سولفوریك و كلریدریك و آب است تا بخاطر روغن، نفت و بنزین. كاربر درجه حرارتها و فشارهای بالا در صنایع شیمیایی باعث امكان پذیر شدن فرایند جدید یا بهبود فرایند قدیمی شده است، به عنوان مثال راندمان بالاتر، سرعت، تولید بیشتر، یا تقلیل قیمت تمام شده. این مطلمب هم چنین در مورد تولید انرژی از جمله انرژی هسته ای، صنایع فضائی و تعداد بسیار زیادی از روشها و فرایند ها صادق است. درجه حرارتها و فشارهای بالاتر معمولاً باعث ایجاد شرایط خوردگی شدیدتری می گردند. بسیاری از فرایند ها و عملیات متداول امروزه بدون استفاده از مواد مقاوم در برابر خوردگی غیر ممكن یا غیر اقتصادی میباشد.