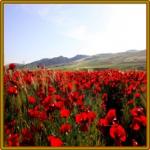
سلام به وب من خوش آمدید دوستان و همراهان عزیز از اینکه مهمان این وب هستید بسیار سپاسگزارم منتظر نظرات سازنده ی شما دوستان هستم
عنوان | پاسخ | بازدید | توسط |
![]() |
1 | 1215 | piskesvat |
![]() |
3 | 2709 | mehran99 |
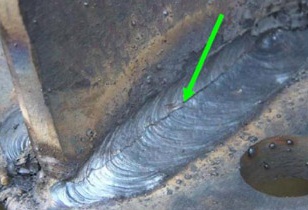
گروه شماره 1- ترکها (Cracks)
ترک (Cracks) ناپیوستگی بوجود آمده بوسیله پارگی موضعی است. که میتواند ناشی از سرد شدن یا تنش باشد. جوش و فلز مبنا زمانی ترک میخورند که تنشهای موضعی بوجود آمده است مقاومت تسلیم فلز بیشتر شوند. ترک خوردگی همواره با افزایش تنش در نزدیکی ناپیوستگیهای جوش و فلز مبنا یا نزدیک شیارهای مکانیکی که در طرح اتصال پیش بینی شدهاندهمراه است تنشهای باقیمانده هیدروژن از عومل ایجاد ترک بحساب میآیند ترکهای ناشی از جوشکاری که ذاتا شکننده هستند در مرزهای ترک تغییر شکل دائمی کمی نشان میدهند.
ترکها به دو دسته گرم سرد تقسیم میشوند. ترک گرم در خلال انجامد مذاب شکل میگیرد و ترک سرد بعد از آنکه انجماد کامل شد شروع میشود ترکهای سرد که بعضا به ترکهای تاخیری معروفند با هیدروژن اتمی ارتباط خاصی دارند.
ترکهای گرم در مرزدانهها منتشر می شوند ولی ترکهای سرد هم در مرزدانهها تشکل میشوند و هم ممکن است از مرز دانهها گذشته و گسترش یابند
محل استقرار ترکها (Crack Orientation)
ترکها بسته به امتدادشان طولی یا متقاطع خوانده میوشند وقتی ترک موازی محور جوش باشد صرفنظر از اینکه آیا ترک در مرکز جوش است یا ترک پنجه در ناحیه تاثیرحرارت ترک طولی است
ترکهای عرضی عمود بر محور جوش هستند ابعاد این ترکها محدود است و کاملا فلز جوش جای میگیرند و یا اینکه از فلز جوش به درون ناحیهای از فلز مبنا که تحت تاثیر حرارت قرار گرفته و یا حتی خود فلز مبنا رسوخ میکنند انواع ترک بشرح زیر است:
ترک طولی (Longitudinal Crack)
ترک طولی اساسا موازی با محور جوش است ترک طولی به چهار صورت واقع میوشد
در فلز جوش
در مرز جوش
در منطقه تاثیر حرارت
در فلز مبنا
ترک عرضی
ترک عرضی اساسا عمود بر محور جوش است ترک عرضی بیشتر ناشی از اعمال تنشهای فشاری عمود بر جوشی که زیاد قابلیت نرمی ندارد میباشد
ترک عرضی ممکن است بصورت زیر واقع شده باشد
درفلز جوش
در منطقه تاثیر حرارت
در فلز مبنا
ترک چاله جوش
ترک چاله ترک اتنهای جوش است و زمانی اتفاق میافتد که جوشکاری بدرستی و خوب به پایان نرسد. گاهی به این ترک ،ترک ستارهای گفته میشود.
ترک چاله جوش ترک انقباضی بوده و معمولا از قطع ناگهانی قوس ناشی میشود ترک چاله جوش معمولا به سه صورت دیده میشود
طولی
عرضی
ستارهای
ترک گلویی (Thrat Crack)
ترکهای طولی هم جهت با محور جوش در روی سطح آن هستند ترک گلوئی نه همیشه ولی اکثرا جزو ترک گرم به حساب میآید
گروه شماره 2- حفرهها
حفره گازی بوسیله حباب گاز در جوش تشکیل میوشد
منفذ گازی
منفذ تکی حبس شده در جوش اساسا به شکل کروی است
تخلخل (Porosity)
تخلخل در نتیجه حبس گاز به هنگام سرد شدن جوش بوجود میآید تخلخل معمولا کروی است ولی احتمالا تخلخل طولی نیز وجود دارد حفرههای گازی در قطعات چدنی شاید به شکل لایه به لایه هم پیدا شود تخلخل هر چقدر هم زیاد باشد خطرش به اندازه ناپیوستگیهای تیز که موجب تمرکز تنش میشوند نیست
تخلخل زیادی نشانه آنست که عوامل جوشکاری مواد مصرفی یا طرح اتصال به درستی کنترل نشدهاند یا فلز مبنا کثیف و الوده بوده یا فلز مبنا با فلز جوش ناسازگار است
تخلخل منصرا ناشی از هیدروژن نیست ولی وجود تخلخل بیانگر وجود هیدروژن در جوش و ناحیه حرارت دیده است که در فلزات آهنی احتمال ترک خوردن قطعه را زیادتر میکند
تخلخل با پخش یکنواخت
تخلخل با پخش یکنواخت تعدادی منفذ گازی پخش شده بصورت یکنواخت سرتاسر فلز جوش است اگر این تخلخل در جوش بیش از حد وجود داشته باشد بیشتر به علت عیب تکنیک جوشکاری یا نقص در مواد است.
روش آماده سازی اتصال یا مواد مصرفی میتوانند در مواردی موجب بروز تخلخل شوند اگر جوشی آهستهتر از حد لازم سرد شود حجم زیادی از گازها در حین انجماد خارج میشوند و در نتیجه حفرههای کمی در جوش باقی خواهد ماند
تخلخل خوشهای (Cluster porosity)
تخلخل موضعی یا تخلخل خوشهای حفرههایی هستند که در یک محل مجتمع شدهاند و اکثرا از برقراری و قطع نادرست قوس میباشند
تخلخل خطی (Linear porosity)
یکسری حفرهها باریک میباشند که بیشتر در طول سطوح میان جوش گرده جوش یا نزدیک ریشه جوش بوجود میآیند تخلخل خطی یک خط از منفذهای گازی میباشد که بصورت موازی با محور جوش واقع شده است
تخلخل لولهای (Piping porosity)
تخلخل لولهای یا حرفه طویل شده حفرهای گازی و طویل است
تخلخل لولهای در جوشهای گوشهای از ریشه بطرف سطح جوش امتداد دارد وقتی که یک یا دو حفره در سطح جوش مشاهده شوند سنگ زنی دقیق میتواند تخلخل زیر سطحی را اشکار سازد قسمت اعظم تخلخلهای لولهای کاملا تا سطح جوش امتداد پیدا نمی کنند
سوراخ کرمی (Worm Hole)
سوراخ کرمی حرفه لولهای شکل در فلز جوش ناشی از آزاد شدن گاز است شکل و موقعیت سوراخهای کرمی بوسیله حالت انجماد و منابع گاز تعیین میشود عموما حفرههای لولهای به خوشهای و جناغی دسته بندی میشوند.
منفذ سطحی
منفذ سطحی منفذ گازی کوچک در سطح جوش است
گروه شماره 3- آخال توپر (Solid Inclusion)
آخال توپر مواد خارجی توپر حبس شده در فلز جوش است. آخالها عبارتند از ناخالصیها یا مواد خارجی که حین فرایند جوشکاری داخل حوضچه مذاب میشوند. آخال موجب تضعیف جوش میگردد.
بعنوان نمونه آخال سرباره را میتوان نام برد یعنی سربارهای که بطور طبیعی برای محافظت فلز داغ روی جوش تشکیل میشود ممکن است در داخل جوش محبوس گردد.
اگر الکترود بدرستی نوسان داده نشود نیروی قوس بعضی از ذرات سرباره را به داخل حوضچه مذاب میدهد . بهنگام انجماد فلز مذاب چنانچه این آخالها به خارج حوضچه مذاب شناور نشود در فلز محبوس گردیده و جوش را معیوب میسازند. وجود آخال در جوشکاری سقفی احتمال بیشتری دارد زیر در جوشکاری سقفی بمنظور جلوگیری از ریزش فلز مذاب سعی میشود حوضچه مذاب خیلی سیال نباشد و سریعتر منجمد گردد
معهذا چنانچه الکترود بدرستی نوسان داده شود از الکترود مناسبی استفاده گردد و شدت جریان جوشکاری بدرستی تنظیم گردد میتوان از آخال جلوگیری نمود یا مقدار آنرا تقلیل داد
اخال سرباره
آخال سرباره مواد غیر فلزی جامدی است که در فلز جوش یا بین فلز جوش و فلز مبنا حبس شده باشد و بیشتر در جوشهایی که با فرآیندهای قوسی دستی یا قوسی زیر پودری جوشکاری شدهاند یافت میشود. در کل آخالهای سرباره بر اثر عیوب تکنیک جوشکاری، طراحی نامناسب طرح اتصال یا عدم تمیزکاری سطح جوش در بین دو پاس پدید میآیند معمولا سرباره مذاب به سمت سطح جوش حرکت نمیکند شیارهای تیز درسطوح میان جوش یا بین پاسها سبب حبس سرباره در زیر فلز مذاب جوش میشوند آخال سرباره بسته به وضعیت تشکیلش ممکن است بصورت زیر باشد
خطی
منفرد
اخال پودر (Flux Inclusion)
اخال پودر پودر حبس شده در فلز جوش است آخال پودر بسته به وضعیت میتواند بصورت زیر باشد
خطی
منفرد
گروه مشاره 4- ذوب ناقص(Lack of fusion) و
نفوذ ناقص (Lack of penetration)
ذوب ناقص یا نفوذ ناقص در ریشه جوش یکی از عیبهای مهم بشمار میآید این عیب حاکی از آنست که فلز ذوب شده با فلز مبنا در ناحیه ریشه جوش نخورده است وجود این عیب مقاومت جوش را شدیدا کاهش داده و اتصال را غیر قابل اعتماد میسازد و بعلاوه خود تنشهائی را تولید میکند که بیش از پیش مقاومت جوش را در مقابل نیروی خارجی میکاهد
ذوب نشدن و نفوذ نکردن ریشه نشانه آن است که شدت جریان جوشکاری کافی نبوده یا حرکت الکترود سریع بوده است یعنی در هرحال فلز حرارت کافی ندیده تا در محل مورد نظر ذوب شود
اگر زاویه پخ لبهها کوچک باشد گرم کردن فلز مبنا در ناحیه ریشه جوش مشکل است و ممکن است باعث بروز این عیب شود
همچنین پاک نبودن لبه کار و نفوذ ناخالصیها در جوش ممکن است سبب ذوب شدن و نفوذ نکردن ریشه شود اینعیب را با نگاه کردن پشت جوش در صورت دسترسی میتوان دید اگر این عیب از اندازه مجاز بیشتر باشد بایستی محل معیوب تعمیر گردد.
ذوب ناقص
ذوب ناقص عدم یکپارچگی بین فلز و جوش و فلز مبنا یا فلز جوش با فلز جوش است این عیب به یکی از صورتهای ذیل خواهد بود
ذوب ناقص دیواره جانبی
ذوب ناقص بین پاسی
ذوب ناقص در ریشه جوش
ذوب ناقص نتیجه تکنیک نادرست جوشکاری آماده سازی غلط فلز مبنا یا طرح اتصال نامناسب است علت ذوب ناقص (عدم ادغام کامل) عبارتست از کمی حرارت جوشکاری یا فقدان راهیبای به همه سطوح ادغام یا هر دو چسبندگی شدید اکسیدها حتی اکر مسیر مناسبی جهت دستیابی به سطوح فراهم شود و حرارت کافی تامین گردد بازهم مانع ادغام کامل خواهد شد.
ذوب نشدن لبه جوش
این عیب ممکن است در نتیجه جوشکاری با شدت جریان کم یا حرکت سریع الکترود پدید آید یعنی فلز الکترود ذوب شده و روی فلز مبنا که هنوز بقدر کافی گرم نشده میریزد و در حال نتیجه لبههای فلز مبنا خوب جوش نمیخود
در این محلها نیروی جسبندگی بین فلز جوش و فلز مبنا ناچیز بوده و گرده ذوب شده ممکن است به آسانی از لبه قطعه جداشود
این عیب را میتوان با پرتو نگاری با اشعه ایکس یا گاما اشکار نمود
نفوذ ناقص
نفوذ ناقص عدم ذوب بین فلز مبنا و فلز مبنا بخاطر نرسیدن فلز جوش به داخل ریشه اتصال است
نقطهای که عدم نفوذ و ادغام در آن روی داده با ناپیوستگی بنام نفوذ ناقص معرفی میشود حرارت ناکافی طرح اتصال نامطلوب یا هدایت جانبی قوس جوشکاری به شکل نادرست از جلمه عواملی هستند که موجب نفوذ ناقص میشوند بعضی فرآیندها نسبت به بعضی دیگر قادرند نفوذ بیشتری ایجاد کنند
اتصالاتی که باید از هر دو طرف جوشکاری شوند، بعد از جوشکاری یک طرف و قبل از جوشکاری طرف دیگر، برای اطمینان از عدم نفوذ ناقص آن را میتوان شیارزندی نمود.
مقدار نفوذ لازم در هر اتصال در نقشهها معین میشود. بدست آوردن نفوذ لازم بستگی به قابلیت دسترسی منبع حرارت و فلز پر کننده به محل جوشکاری دارد
نفوذ ناقص ممکن است از طراحی نادرست درزجوش ناشی شود بسیاری از طراحان برای اطمینان از عدم وجود نواحی با نفوذ ناقص در ریشه جوش شیارزنی صد در صد پشت جوش و جوشکاری مجدد از پشت جوش را تجویز مینمایند.
در سالختمان پل اتصال جوشی با مقدار معینی نفوذ از نظر طراحی قبول نیست مگر آنکه با انجام آزمایش غیر مخرب از سلامت جوش اطمینان حاصل شود.
نفوذ اضافی
نفوذ اضافی فلز جوش اضافی بیرون زده از ریشه جوش یک طرف یا بیرون زده از فلز جوش قبلی اتصال یک یا چند پاسه است
بیرون زندگی موضعی نفوذ اضافی موضعی است
نیمرخ نادرست جوش
نیمرخ نادرس جوش خیلی کوچک بودن زاویه بین سطح فلز مبنا و سطح مماس به گرده جوش در پنجه جوش است
رویهم افتادگی
رویهم افتادگی فلز جوش اضافی در پنجه جوش است که روی سطح فلز مبنا را پوشانیده ولی با ان نیامیخته است یا بعبارت دیگر به حالتی گفته میشود که لبه کناری جوش بیش از حد متعارف بر رروی سطح قطعه کار و لبه اتصال پیشروی نماید و بر اثر عواملی همچون عدم کنترل عوامل جوشکاری انتخاب نادرست مواد جوشکاری یا اماده سازی نامناسب فلز مبنا روی میدهد اگر هم اکسید ها محکم به فلز مبنا چسبیده باشد بطوری که از ادغام جلوگیری کنند این حالت قابل پیش بینی است.
سر رفتن جوش، انفصالی سطحی است که شیار مکانیکی تشکیل میدهد و تقریبا همیشه نظر بازرسین غیر قابل قبول است.
عدم همترازی خطی
عدم همترازی خطی عدم همترازی بین دو قطعه جوش داده شده است بطوری که یا وجود موازی بودن پلانها سطحشان دو قطعه هم تراز نیستند
عدم همترازی زاویهای
عدم همترازی زاویهای عدم همترازی بین دو قطعه جوش داده شده است بطوری که پلانهای سطوحشان موازی نیستند.
گود افتادگی
گود افتادگی فروریختگی فلز جوش بخاطر ثقل است بسته به وضعیت گود افتادگی به یکی از صورتهای زیر است:
- گود افتادگی در حالت افقی- عمودی
- گود افتادگی در حالت تخت یا سقفی
- گود افتادگی در جوش گوشهای
- گود افتادگی (ذوب کردن) لبه
نامتقارنی اضافی جوش گوشهای
اسم عیب گویا است و توضیح لازم ندارد.
پهنای نامنظم
پهنای نامنظم تغییر اضافی پهنا است
سطح نامنظم
سطح نامنظم ناهمواری اضافی سطح است
تقعر ریشه
تقعر ریشه شیار کم عمق بخاطر انقباض جوش لب بلب در ریشه است
تخلخل ریشه
تخلخل ریشه اسفنجی شدن ریشه جوش بخاطر حبابی شدن فلز جوش در لحظه انجماد است
شروع مجدد ضعیف
شروع مجدد ضعیف نامنظمی سطحی موضعی در شروع مجدد جوش است
گروه 6- عیوب متفرقه (MISCELLANEOUS IMPERFECTION)
عیوب متفرقه به تمامی عیوبی گفته میشود که در گروههای شماره یک لغایت شماره نمیتواند گنجانیده شود
جرقه هرز یا لکه قوس (Stray Flash or Arc Strike)
جرقه هرز یا لکه قوس، آسیب دیدگی موضعی سطح فلز مبنای مجاور جوش ناشی از قوس زنی یا روشن کردن قوس خارج از شیار جوش است.
جرقه (Spatter)
جرقه، گلولهای فلز جوش یا فلز پر کننده است که حین جوشکاری پرتاب شده و به سطح فلز جوش منجمد شده چسبیده است.
سطح پاره شده (Torn Surface)
سطح پاره شده، آسیب دیدگی سطح بخاطر برطرف کردن یا شکستن اتصال جوش موقت است.
علامت سنگ زنی (Grinding Mark)
علامت سنگ زنی، اسیب دیدگی موضعی بخاطر سنگ زنی است.
علامت چکش سرباره پاک کنی (Chipping Mark)
علامت چکش سرباره پاک کنی، آسیب دیدگی موضعی بخاطر استفاده از قلم تیزبر یا ابزار دیگر است
سنگ زنی اضافی (Under Flushing)
سنگ زنی اضافی، کاهش ضخامت فلز بخاطر سنگ زنی اضافی است.
(AWS D1.1) معیار پذیرش بازرسی چشمی
دسته بندی ناپیوستگی و معیار بازرسی بارگذاری استاتیک اتصالات غیر لولهای بارگذاری دورهای اتصالات غیر لولهای اتصالات لولهای (تمام بارها)
1- ممنوعیت ترک (CRACK)
هر نوع ترک، بدون توجه به اندازه یا موقعیت غیر قابل قبول است. × × ×
2- ذوب جوش/ فلز مبنا
ذوب سرتاسری بایستی بین لایههای مجاور فلز جوش و بین فلز جوش و فلز مبنا باشد × × ×
3- مقطع عرضی چاله جوش
بجز انتهاهای جوشهای گوشهای منقطع، خارج از طول موثرشان، تمام چالههای جوش بایستی پر شده باشند تا اندازه مشخص شده جوش را تامین کنند × × ×
4- نیمرخ جوش
نیمرخهای جوش بایستی با نمونه ارائه شده مطابقت داشته باشد × × ×
5- زمان بازرسی
بازرسی جشمی جوشهای در تمام فولادها میتواند بعد از آن که جوش کامل شده تا درجه حرارت محیط سرد شده باشد، شروع شود
معیار پذیرش فولادهای ASTM A514,A517 و A709 GRADE 10, 100W بایستی برمبنای بازرسی چشمی انجام شده حداقل 48 ساعت بعد از تکمیل جوش باشد. × × ×
6- جوشها با اندازه کمتر
اندازه جوش گوشهای در هر جوش پیوسته، بدون نیاز به اصلاح میتواندکمتر از اندازه اسمی مشخص شده (L) به مقادیر زیر (U) باشد:
L اندازه اسمی مشخص شده جوش (میلیمتر) U کاهش مجاز از L (میلیمتر)
6 5/2
3
در همه موارد، قسمت با اندازه کمتر جوش نبایستی از 10% طول جوش بیشتر باشد
در جوشهای جان به بال تیر ورقها، کمبود جوش در دو انتها به طولی معادل دو برابر عرض بال ممنوع است. × × ×
7- بریدگی کناره (UNDERCUT)
الف- برای متریال قطعات با ضخامت کمتر از 25 میلیمتر، بریدگی کناره نبایستی از یک میلیمتر بیشتر باشد به استثنای موارد زیر:
جمع بریدگیهای کناره با عمق حداکثر 6/1 میلیمتر نبایستی بیش از 50 در 300 میلیمتر باشد.
برای متریال با ضخامت بیشتر از 25 میلمتر برای هر طول جوش عمق بریدگی کنار نبایستی از 6/1 میلیمتر باشد ×
ب- در اعضای اصلی وقتی جوش عمود برتنش کششی است، تحت هر شرایط بارگذاری طرح، عمق بریدگی کناره نبایستی از 25/0 میلیمتر بیشتر باشد. در کلیه موارد دیگر، عمق بریدگی کناره نبایستی بیشتر از یک میلیمتر باشد. × ×
8- تخلخل (PORPSITY)
الف- جوشهای شیاری با نفوذ کامل در اتصالات لب بلب عمود برجهت تنش کششی محاسبه شده نبایستی تخلخل لولهای قابل دید داشته باشند. برای تمام جوشهای شیاری دیگر و برای جوشهای گوشهای مجموع تخلخل لولهای قابل دید با قطر یک میلیمتر یا بزرگتر نبایستی در هر 25 میلیمتر طول جوش از 10 میلیمتر بیشتر باشد و نبایستی در هر 300 میلیمتر طول جوش از 20 میلیمتر بیشتر شود ×
ی- تکرار تخلخل لولهای در جوشهای گوشهای نبایستی در هر 100 میلیمتر طول جوش از یکی بیشتر باشد و حداکثر قطر نبایستی از 5/2 میلیمتر بیشتر باشد مگر: برای جوشهای گوشهای متصل کننده محکم کنندهها (STRIFFENERS) به جان، مجموع قطرهای تخلخل لولهای نبیاستی از 10 میلیمتر در هر 25 میلیمتر طول جوش بیشتر باشد و نبایستی از 20 میلیمتر در هر 300 میلیمتر از طول جوش تجاوز نماید. × ×
ج- جوشهای شیاری با نفوذ کامل در اتصالات لب بلب عمود بر جهت تنشهای کششی محاسبه شده نبایستی دارای تخلخل لولهای باشند
برای تمام جوشهای شیاری دیگر، تکرار تخلخل لولهای نبایستی در هر 100 میلیمتر طول از یکی بیشتر بوده و حداکثر قطر نبایستی از 5/2 میلیمتر تجاوز نماید. × ×
یادآوری کلی: علامت (×) نشانه قابلیت کاربرد برای نوع اتصال است، ناحیه هاشور زده نشانع عدم قابلیت کاربرد است
معیار پذیرش عیوب در اسکلت فلزی
این معیار پذیرش طبق کد AWS-D1.1 برای اسکلتهای فلزی (غیر لولهای) با بارگذاری استاتیک و در بازرسی پرتونگاری ارائه میشود
تعاریف
عیوب غیر از ترک بر مبنای عیب طویل شده یا عیب مدور ارزیابی میشوند طول عیب طویل (elongated) بیشتر از سه برابر عرض آن است.
وقتی طول عیب مساوی یا کمتر از سه برابر عرض آن باشد، به ان عیب مدور (Rounded) گفته میشود.
عیب مدور ممکن است دایرهای، بیضی شکل، مخ9روطی یا بشکل نامنظم باشد، ممکن است دم داشته و دانسیته آن متغیر باشد. در ارزیابی، دم هم جزو اندازه عیب بحساب میآید.
تعداد چهار عیب مدور یا بیشتر موقعی ریدف شده (Aligned) بحساب میآیند که با خطی که از میان دو علامت مدور بیرونیتر به موازات طول جوش کشیده شود، در تماس باشند.
تعداد چهار عیب مدور یا بیشتر که با تعریف فوق بصورت ردیف شده به حساب نیایند، عیوب پراکنده (Scattered) نامیده میشود
انبوهی از تخلخل یا عیوب مدور، عیب خوشهای (Cluster) گفته میشود.
معیار پذیرش
جوشهای اسکلتهای فلزی که علاوه بر بازرسی چشمی تحت بازرسی پرتونگاری قرار میگیرند نبایستی ترک داشته باشند و اندازه عیبهای موجود در آنها نبایستی از محدودیتهای مشخص شده زیر بیشتر باشد:
1- عیوب طویل شدهاز اندازه حداکثر نشان داده شده در شکل بیشتر نباشد
2- فاصله عیوب از یکدیگر از حداقل مجاز فاصله نشان داده شده در شکل کمتر نباشد.
3- عیوب مدر بزرگتر از یک سوم E از 6 میلیمتر بیشتر نباشد. گرچه وقتی ضخامت قطعه بیشتر از 50 میلیمتر است، علامت مدور میتواند حداکثر تا 10 میلیمتر باشد فاصله چنین عیبی (عیب مساوی یا بزرگتر از 2 میلیمتر) تا عیب قابل قبول بعدی (طویل یا مدور) یا تا یک لبه یا انتهای جوش متقاطع بایستی حداقل سه برابر بزرگترین بعد عیب بزرگتر از میان عیوب مورد نظر باشد.
4- جمع اندازه نشانههای مدور خوشهای یا عیب منفرد از اندازه مجاز عیب تکی در شکل بیشتر نباشد. فاصله بین این نوع عیب تا عیب خوشهای دیگر یا تا عیب طویل شده دیگر یا تا عیب مدور دیگر، یا تا لبه انتهای جوش متقاطع نبایستی از سه برابر بعد عیب بزرگتر بین عیوب مورد نظر کمتر باشد
5- جمع عیوب انفرادی کمتر از 2 میلیمتر در هر 25 میلیمتر طول جوش نبایستی از دو سوم E یا 10 میلیمتر (هرکدام کمتر است) بیشتر شود. این خواسته مستقل از بندهای 2.1 و 3 فوق است
6- جمع اندازه عیوب خطی نبایستی در طول 6E از E بیشتر باشد اگر طول جوش مورد نظر کمتر از 6E باشد مجمع اندازه عیوب خطی مجاز به همان نسبت کمتر خواهد بود.
منبع:taniansooleh.ir